Automated Intralogistics for Manufacturing Environments
We develop scalable intralogistics solutions for manufacturing factories – designed to control, secure, and optimize internal material flows. Our systems reduce manual effort, prevent supply bottlenecks, and enable seamless, digitally integrated production logistics.
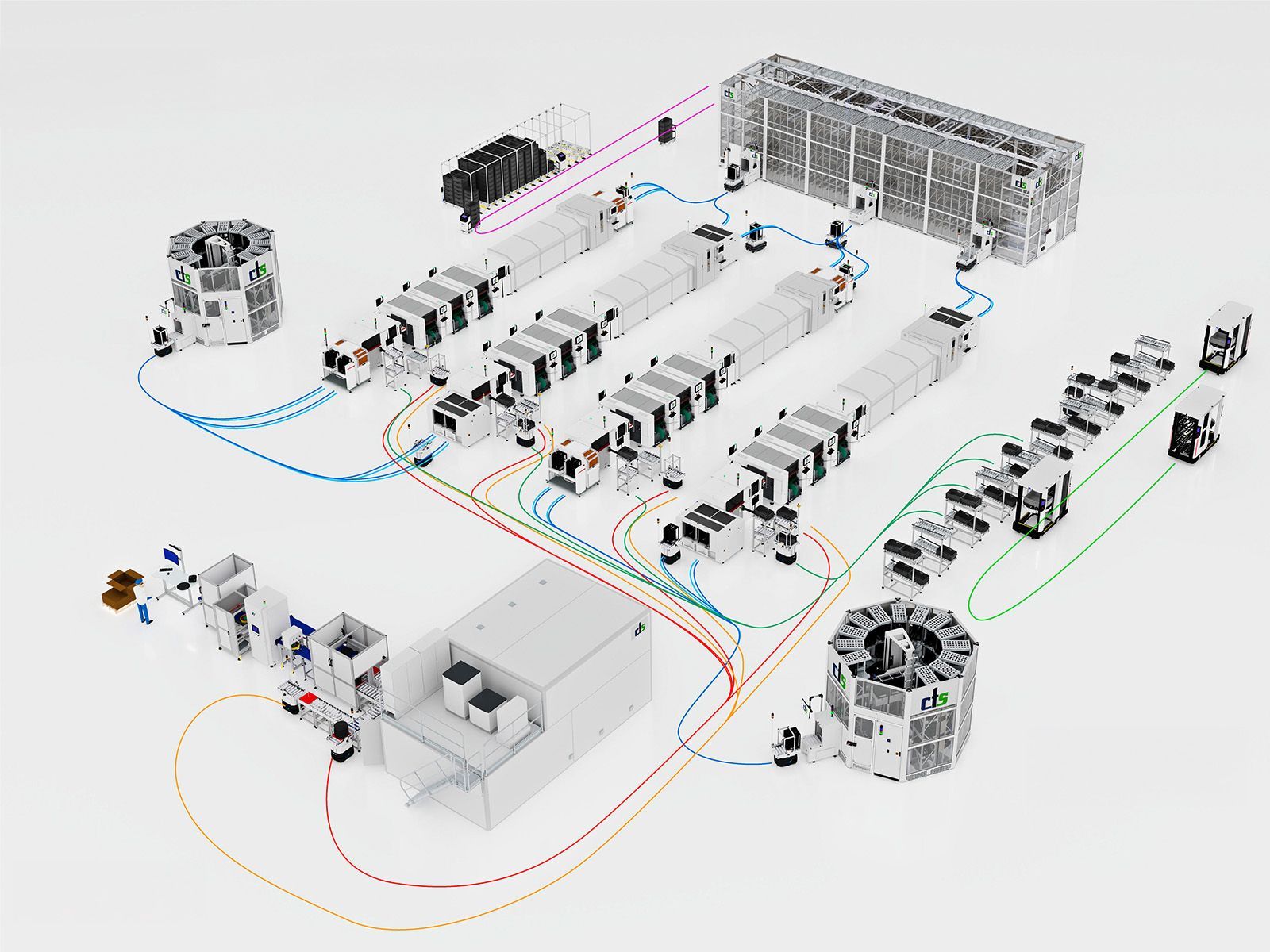
Automated Intralogistics for Manufacturing Environments
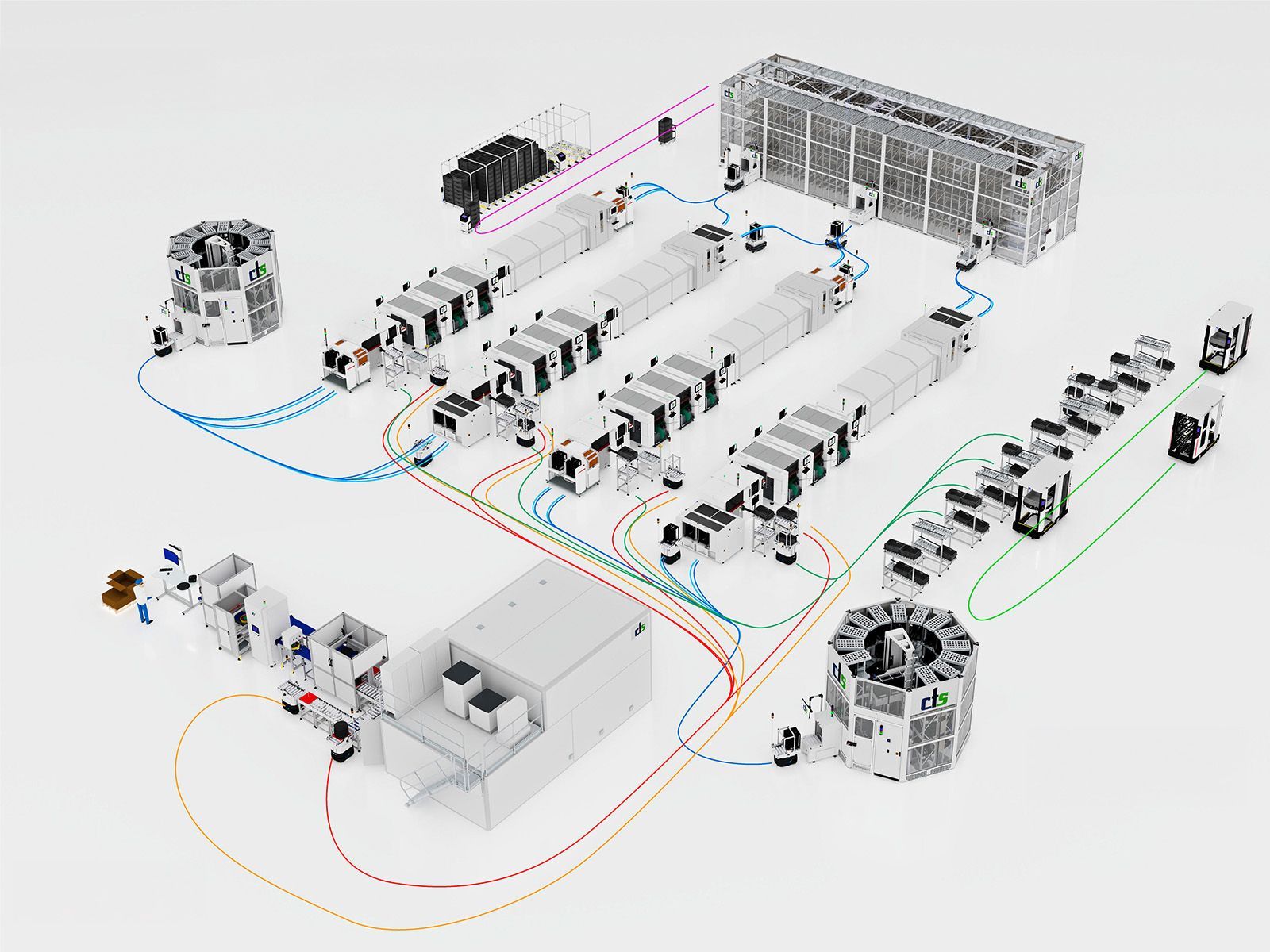
We develop scalable intralogistics solutions for manufacturing factories – designed to control, secure, and optimize internal material flows. Our systems reduce manual effort, prevent supply bottlenecks, and enable seamless, digitally integrated production logistics.
SMART FACTORY INTRALOGISTICS
Automated Intralogistics for Manufacturing Environments
We develop scalable intralogistics solutions for manufacturing factories – designed to control, secure, and optimize internal material flows. Our systems reduce manual effort, prevent supply bottlenecks, and enable seamless, digitally integrated production logistics.
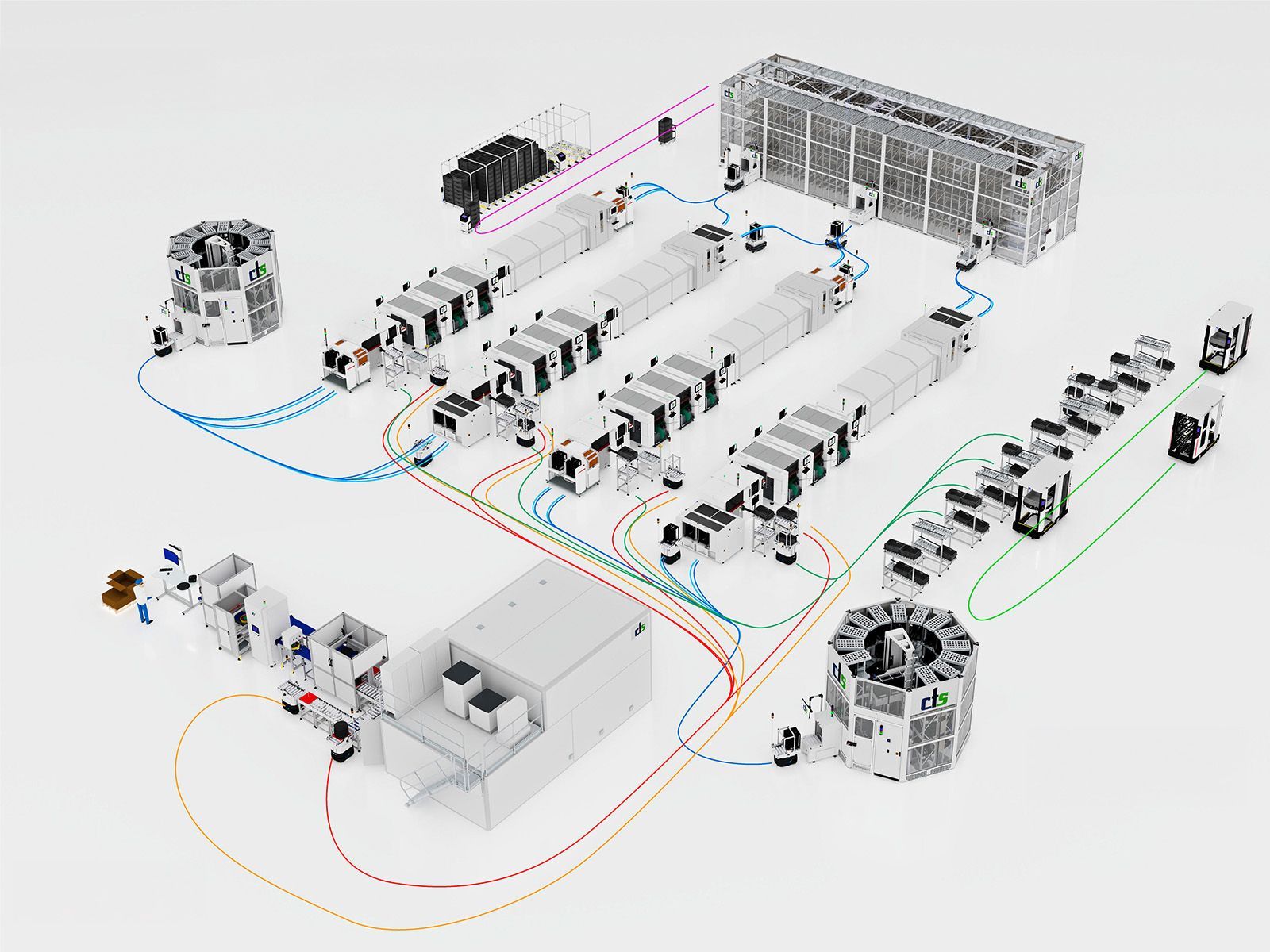
Increased Throughput
Automated intralogistics processes ensure a continuous material flow – fast, reliable, and synchronized with your production cycle.
Accurate Picking & Staging
Ensure that every component is available exactly where it's needed. Digitally managed material flows enable precise and error-free provisioning.
Real-Time Inventory Visibility
Maintain full control over your production inventory at all times. Our systems provide end-to-end transparency across all material movements.
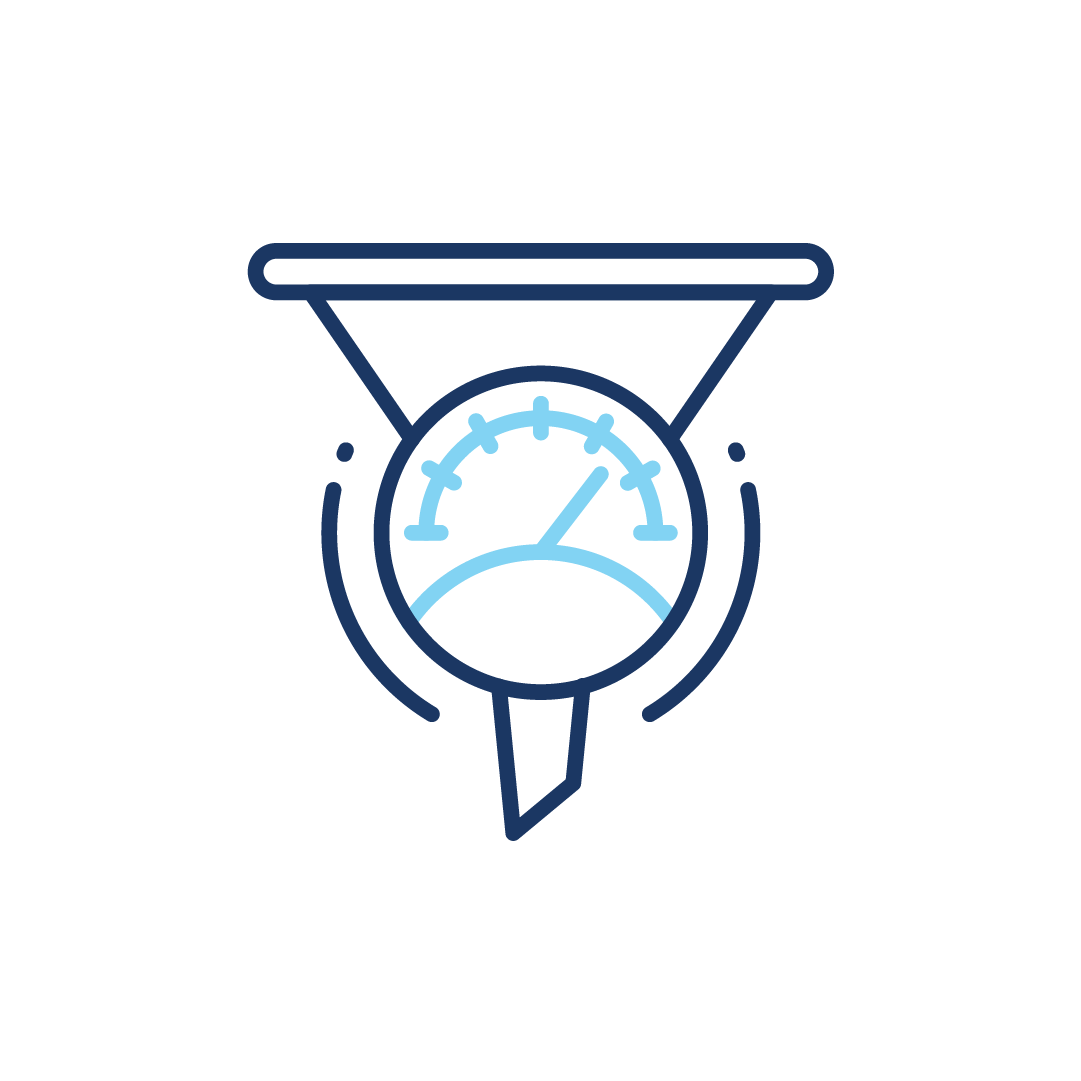
Increased Throughput
Automated intralogistics processes ensure a continuous material flow – fast, reliable, and synchronized with your production cycle.
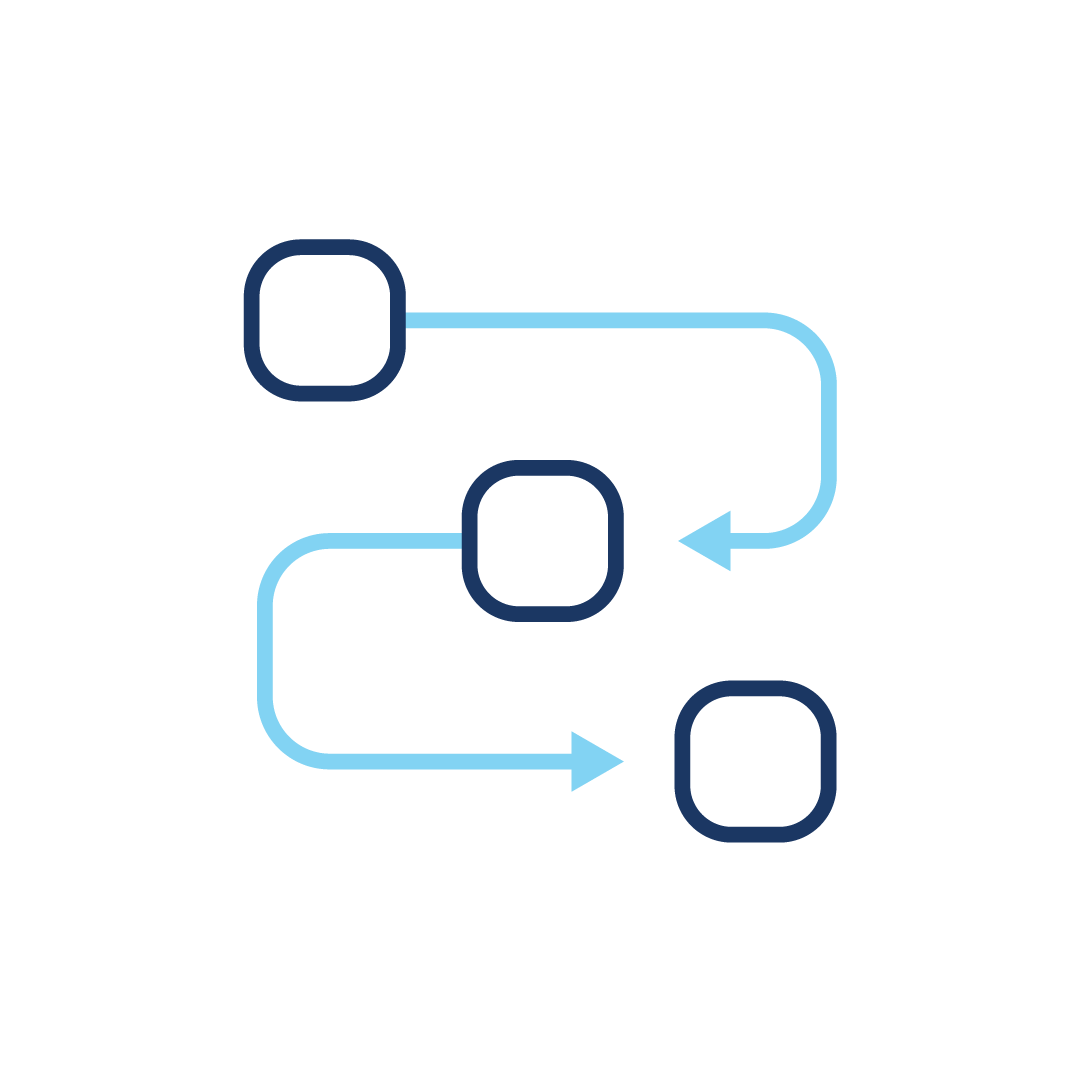
Accurate Picking & Staging
Ensure that every component is available exactly where it's needed. Digitally managed material flows enable precise and error-free provisioning.
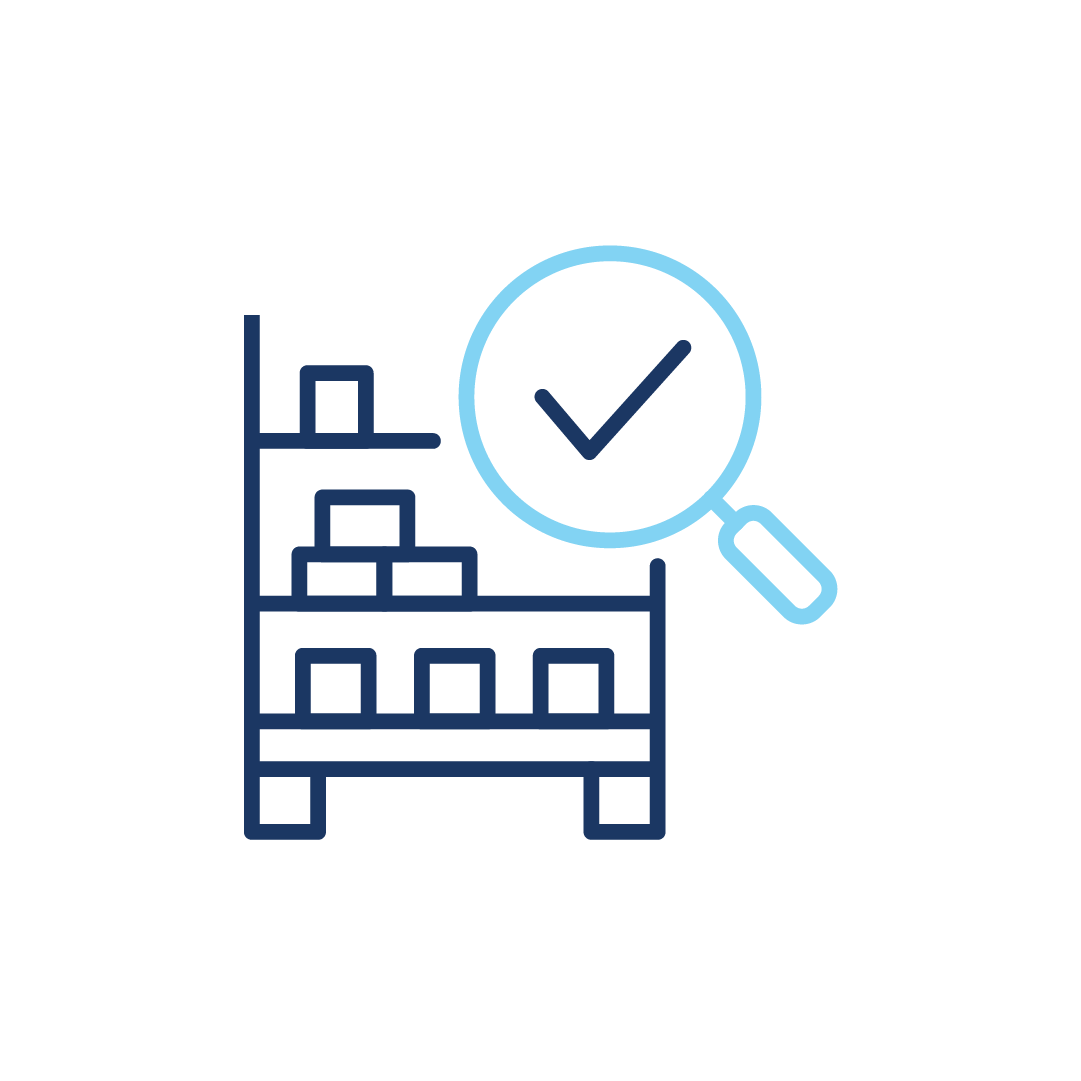
Real-Time Inventory Visibility
Maintain full control over your production inventory at all times. Our systems provide end-to-end transparency across all material movements.
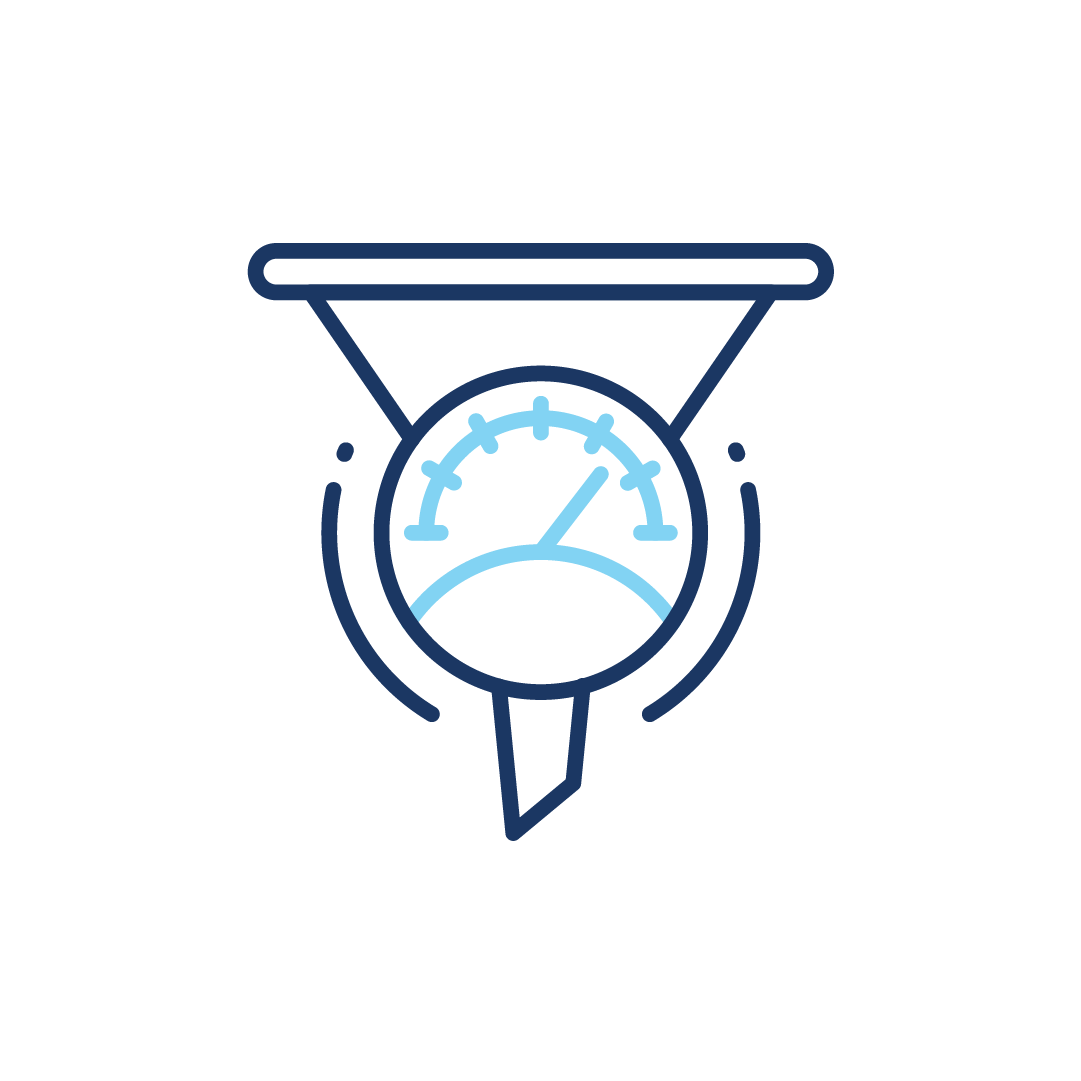
Increased Throughput
Automated intralogistics processes ensure a continuous material flow – fast, reliable, and synchronized with your production cycle.
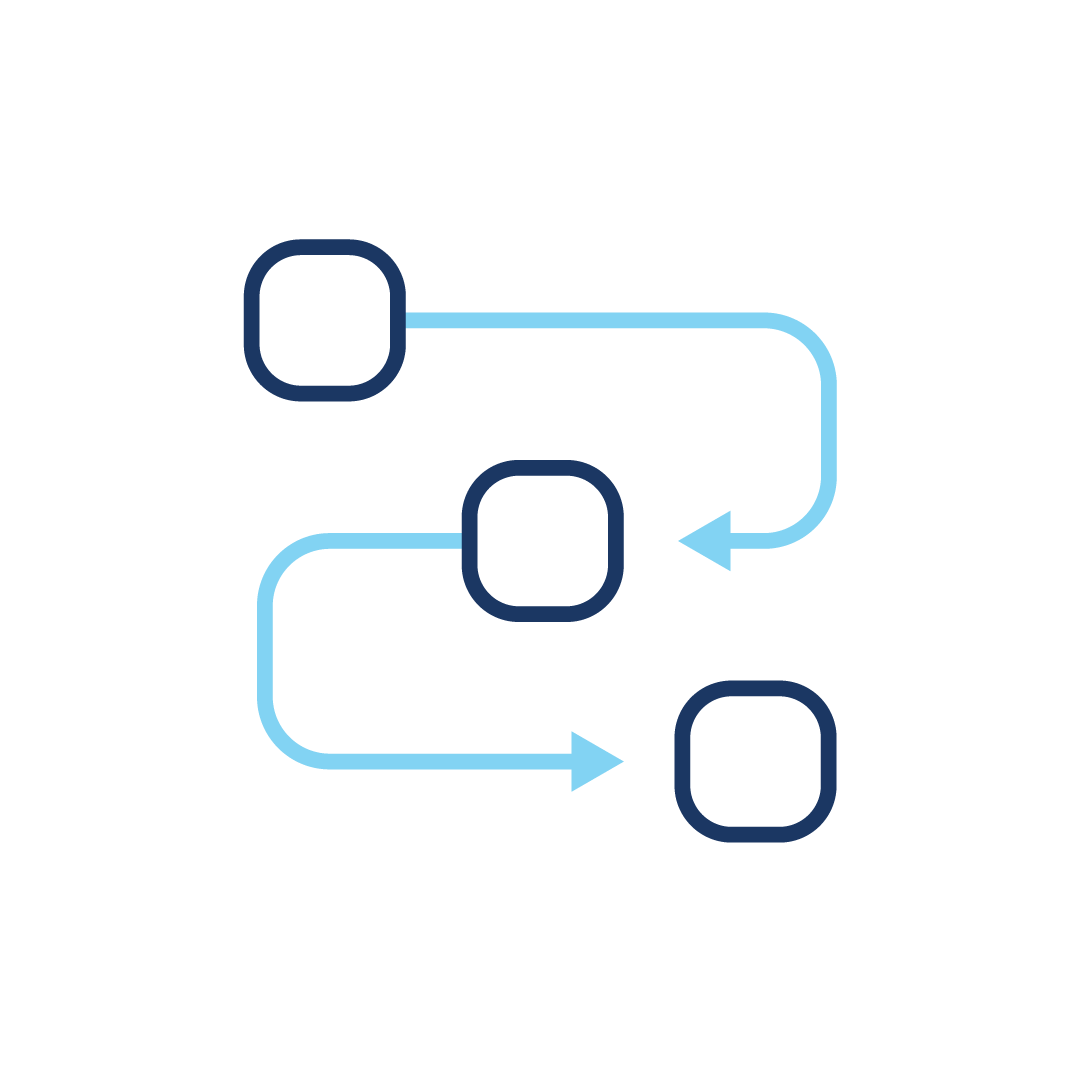
Accurate Picking & Staging
Ensure that every component is available exactly where it's needed. Digitally managed material flows enable precise and error-free provisioning.
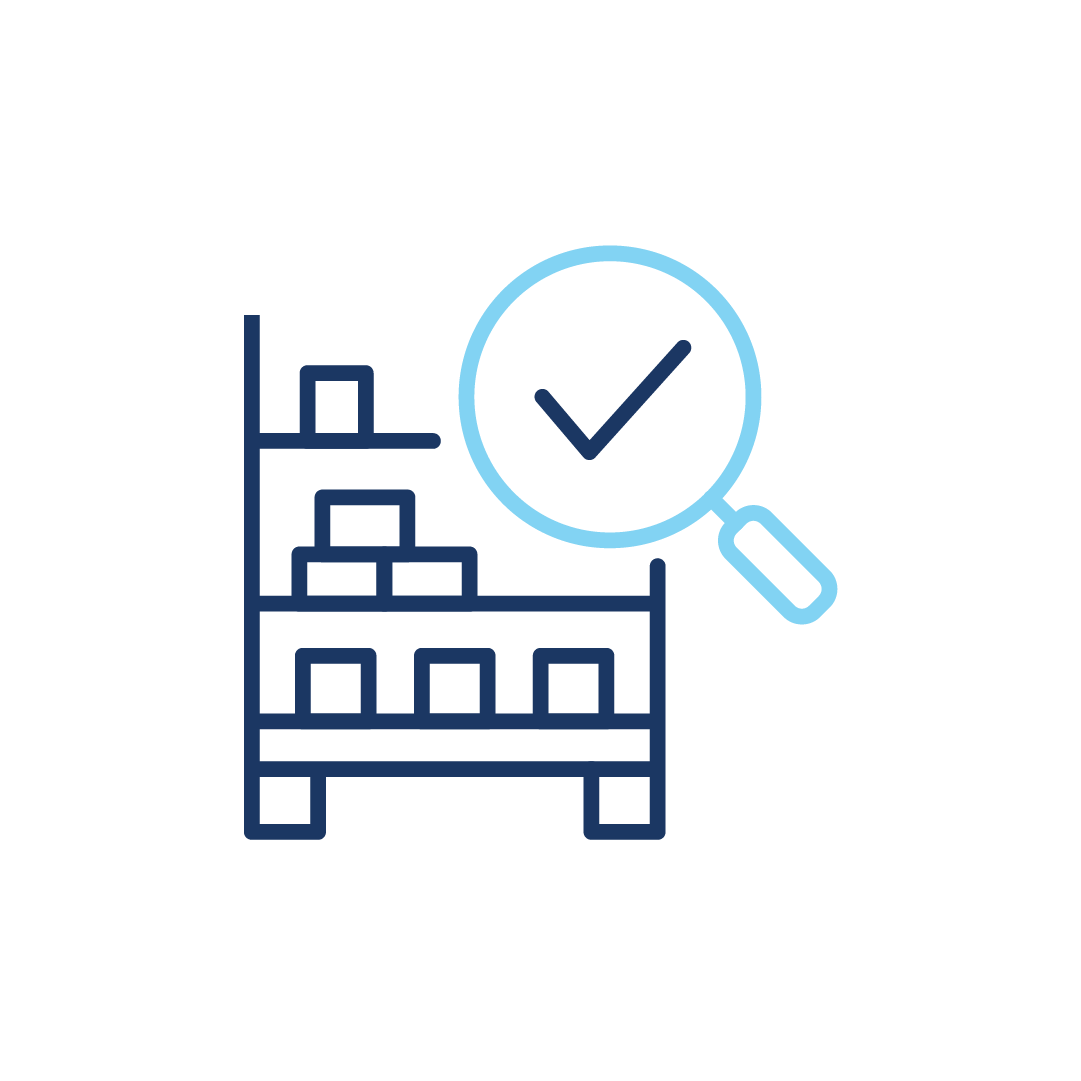
Real-Time Inventory Visibility
Maintain full control over your production inventory at all times. Our systems provide end-to-end transparency across all material movements.
SMART WAREHOUSE / MINI
Compact Warehouse Automation for Production Environments
In many manufacturing facilities, available floor space is limited – especially near the production line.
The Smart Warehouse / Mini is a scalable storage solution designed specifically for space-constrained production areas.
It combines intelligent storage logic with automated material infeed and outfeed, ensuring continuous supply without increasing your spatial footprint.
Whether you're storing small load carriers, workpiece holders, or custom containers – the system handles a wide variety of units securely, efficiently, and on demand. It stabilizes internal material flows, eliminates manual search times, and gives you full control over inventory and availability.
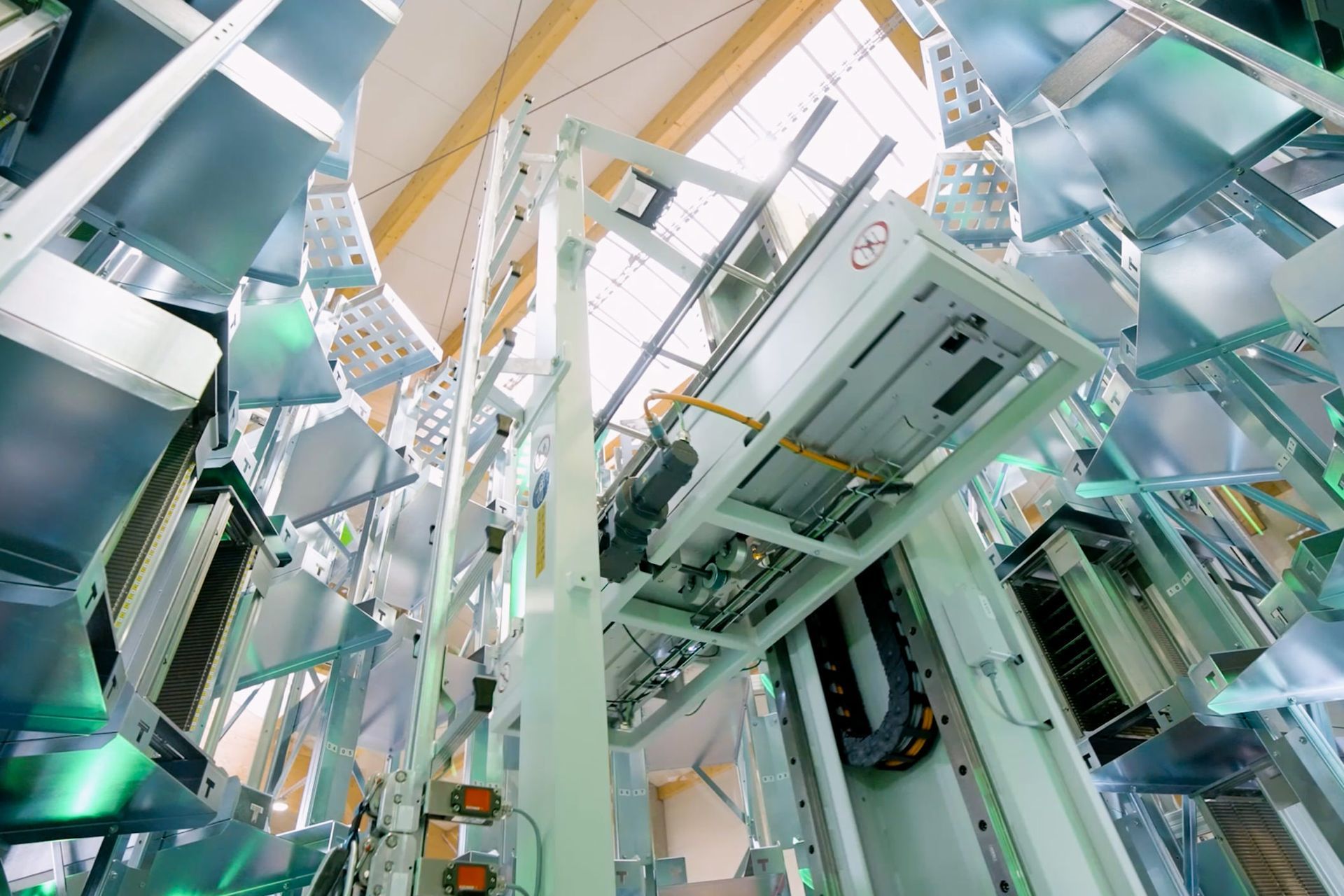
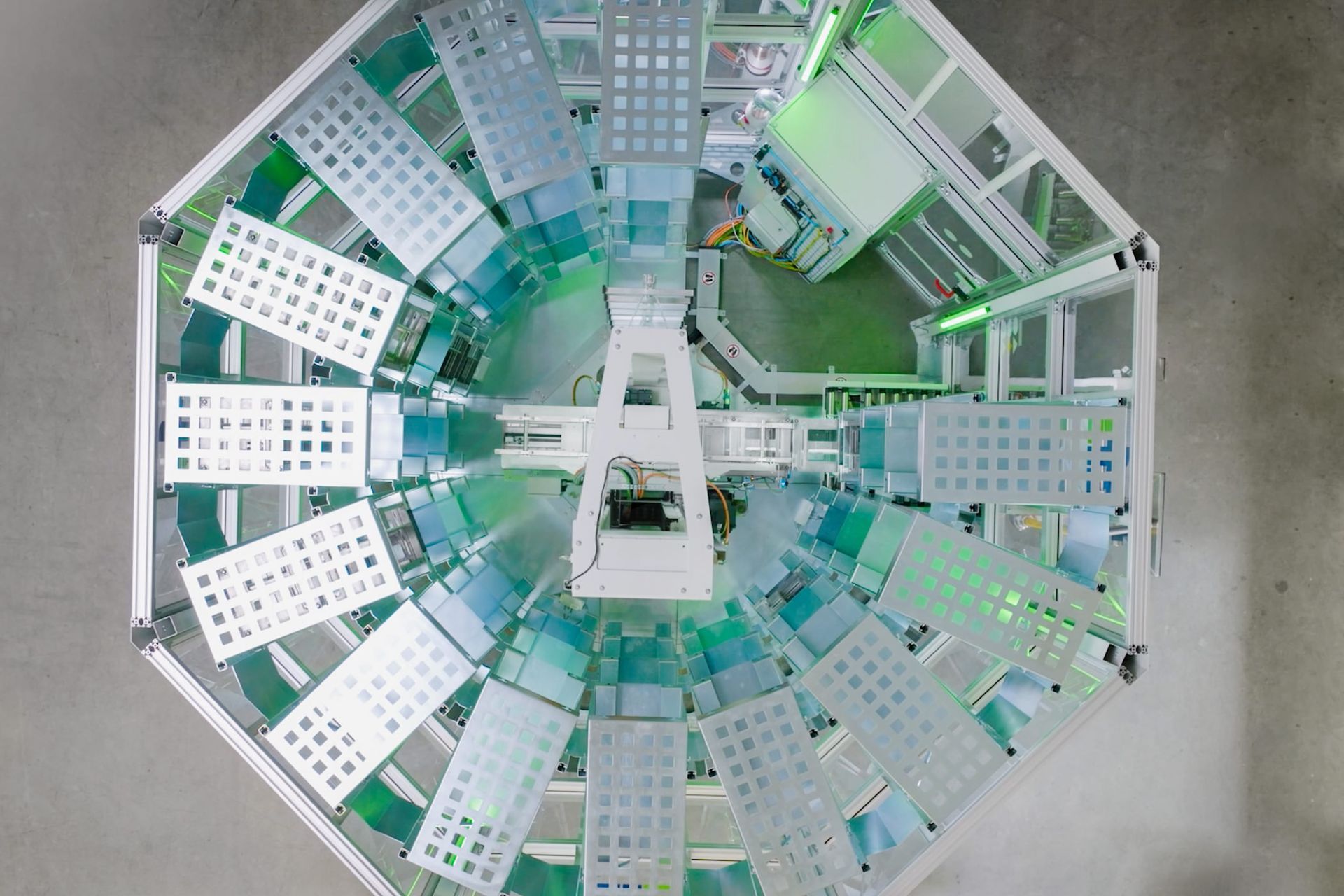
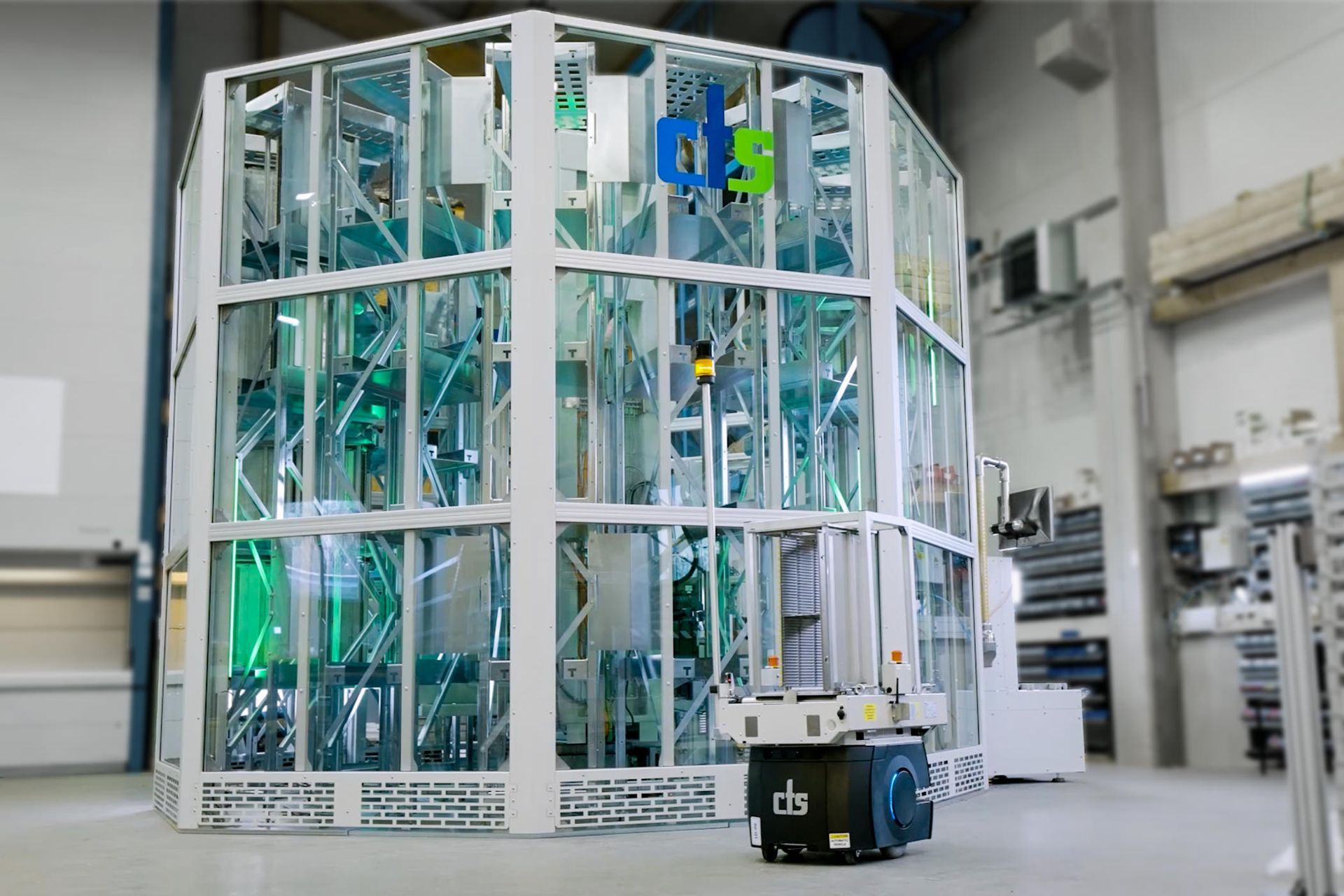
SMART WAREHOUSE / MINI
Compact Warehouse Automation for Production Environments
In many manufacturing facilities, available floor space is limited – especially near the production line.
The Smart Warehouse / Mini is a scalable storage solution designed specifically for space-constrained production areas.
It combines intelligent storage logic with automated material infeed and outfeed, ensuring continuous supply without increasing your spatial footprint.
Whether you're storing small load carriers, workpiece holders, or custom containers – the system handles a wide variety of units securely, efficiently, and on demand. It stabilizes internal material flows, eliminates manual search times, and gives you full control over inventory and availability.
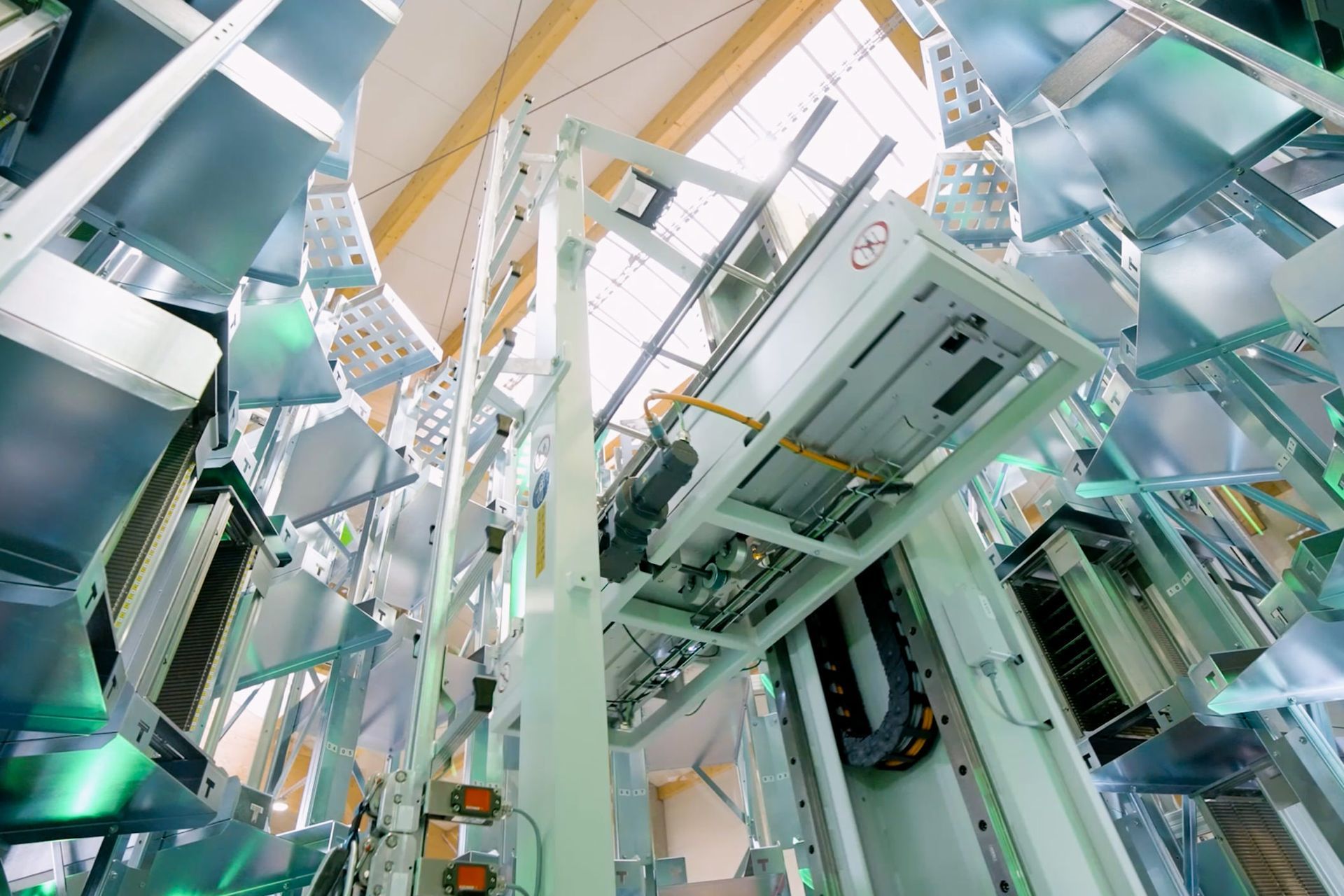
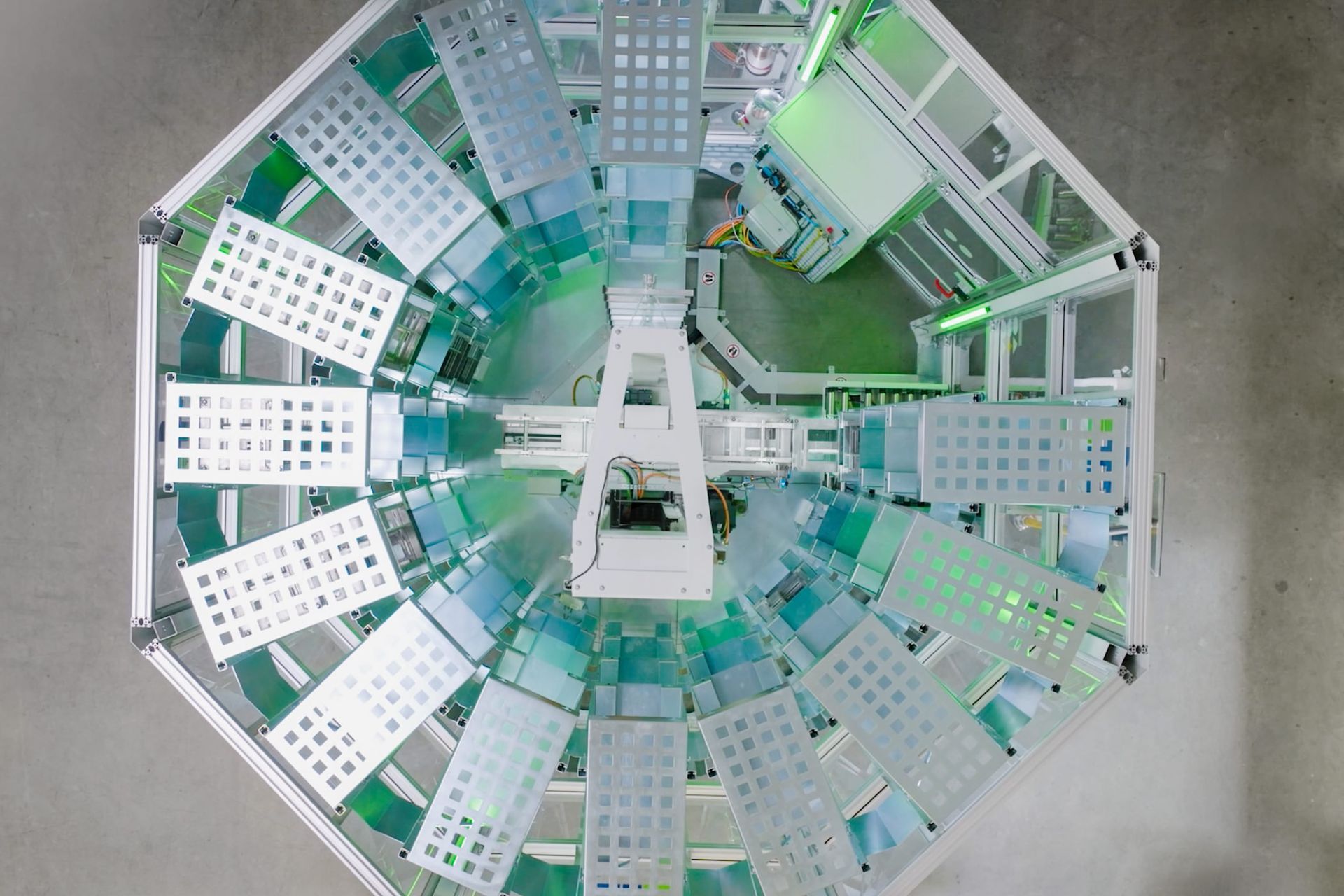
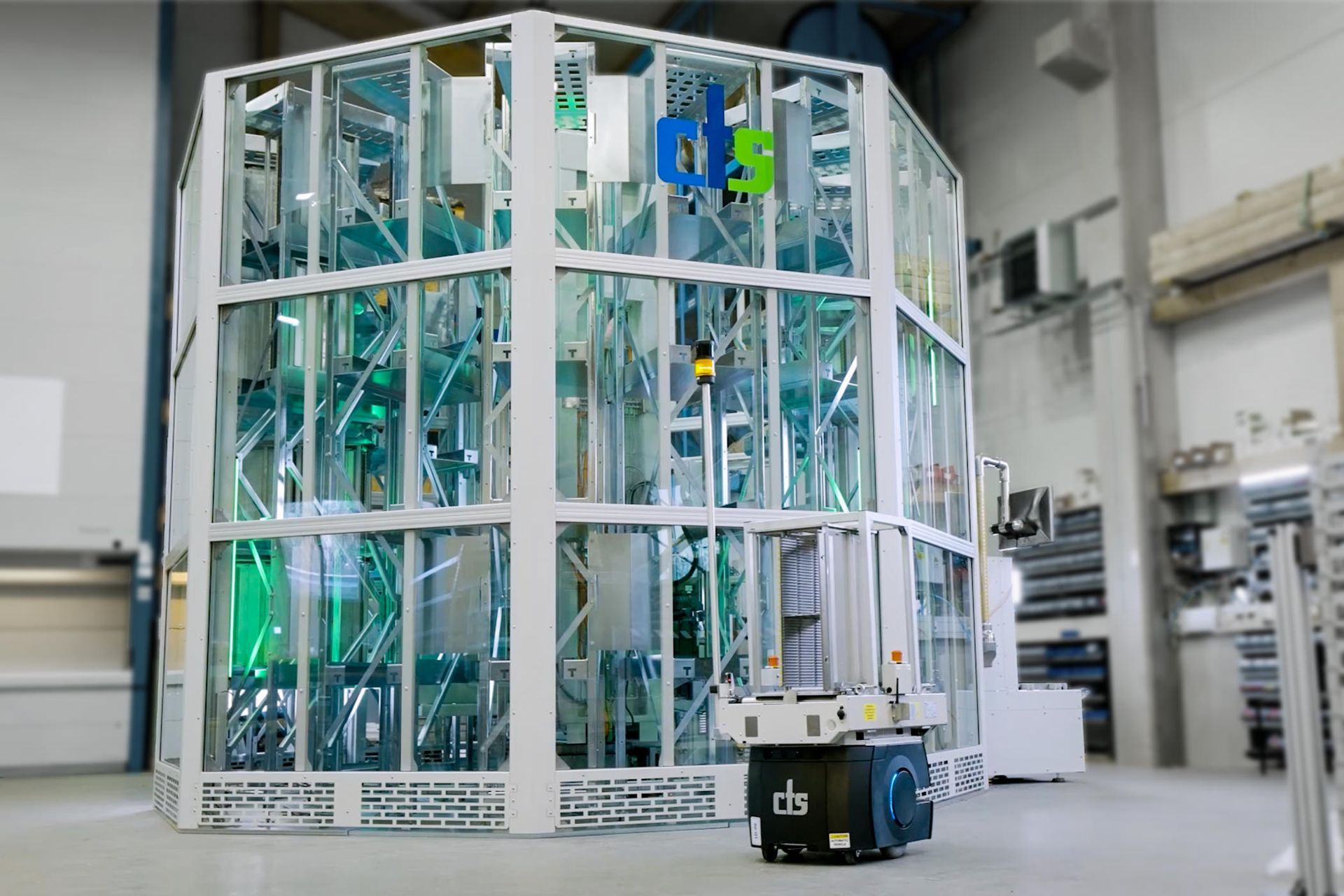
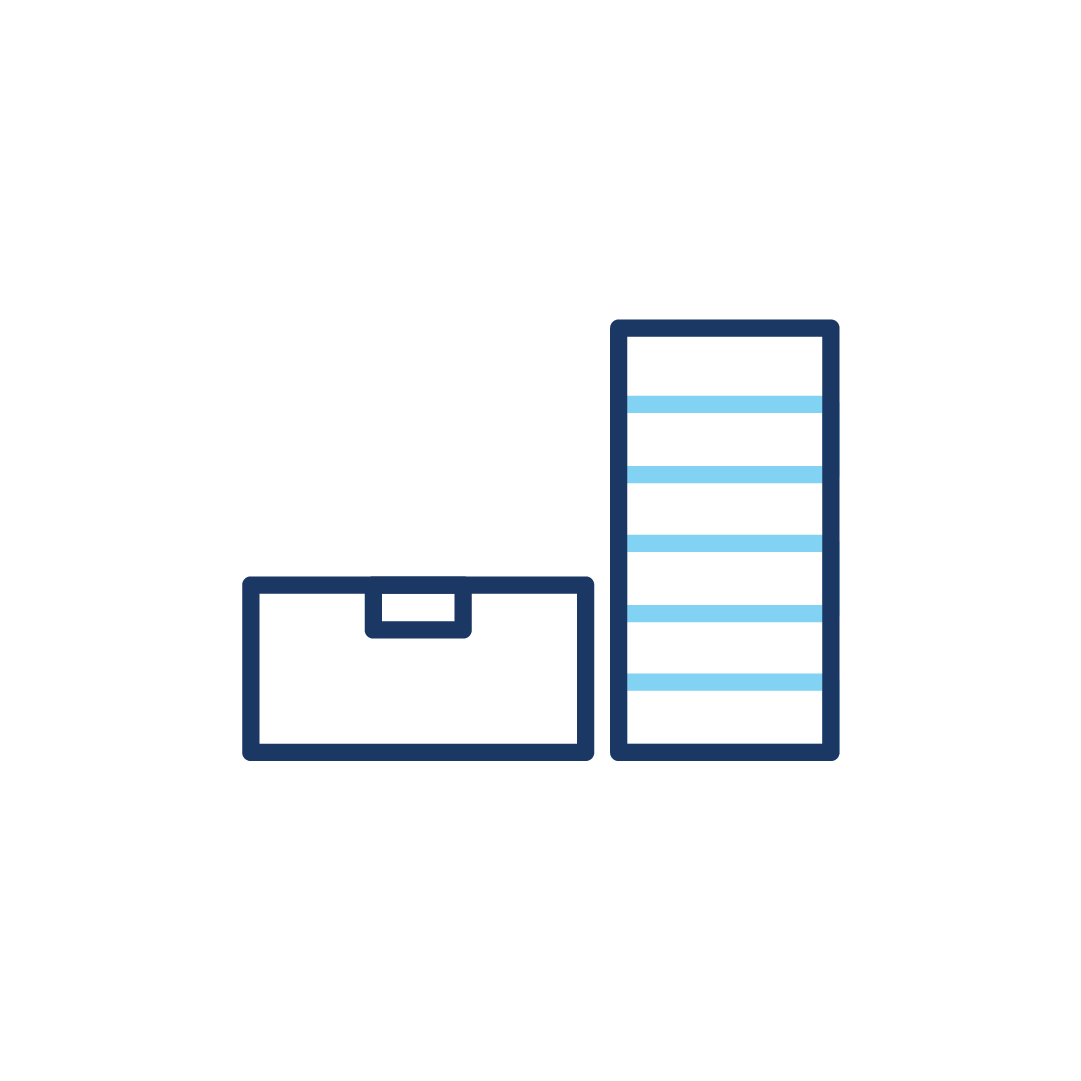
Flexible storage geometry for a wide range of container and carrier formats
Automated interfaces for direct loading and unloading at the production line
Real-time transparency through integrated tracking and tracing
Seamless integration into existing processes, systems, and factory layouts
SMART WAREHOUSE / MINI
Compact Warehouse Automation for Production Environments
In many manufacturing facilities, available floor space is limited – especially near the production line.
The Smart Warehouse / Mini is a scalable storage solution designed specifically for space-constrained production areas.
It combines intelligent storage logic with automated material infeed and outfeed, ensuring continuous supply without increasing your spatial footprint.
Whether you're storing small load carriers, workpiece holders, or custom containers – the system handles a wide variety of units securely, efficiently, and on demand. It stabilizes internal material flows, eliminates manual search times, and gives you full control over inventory and availability.
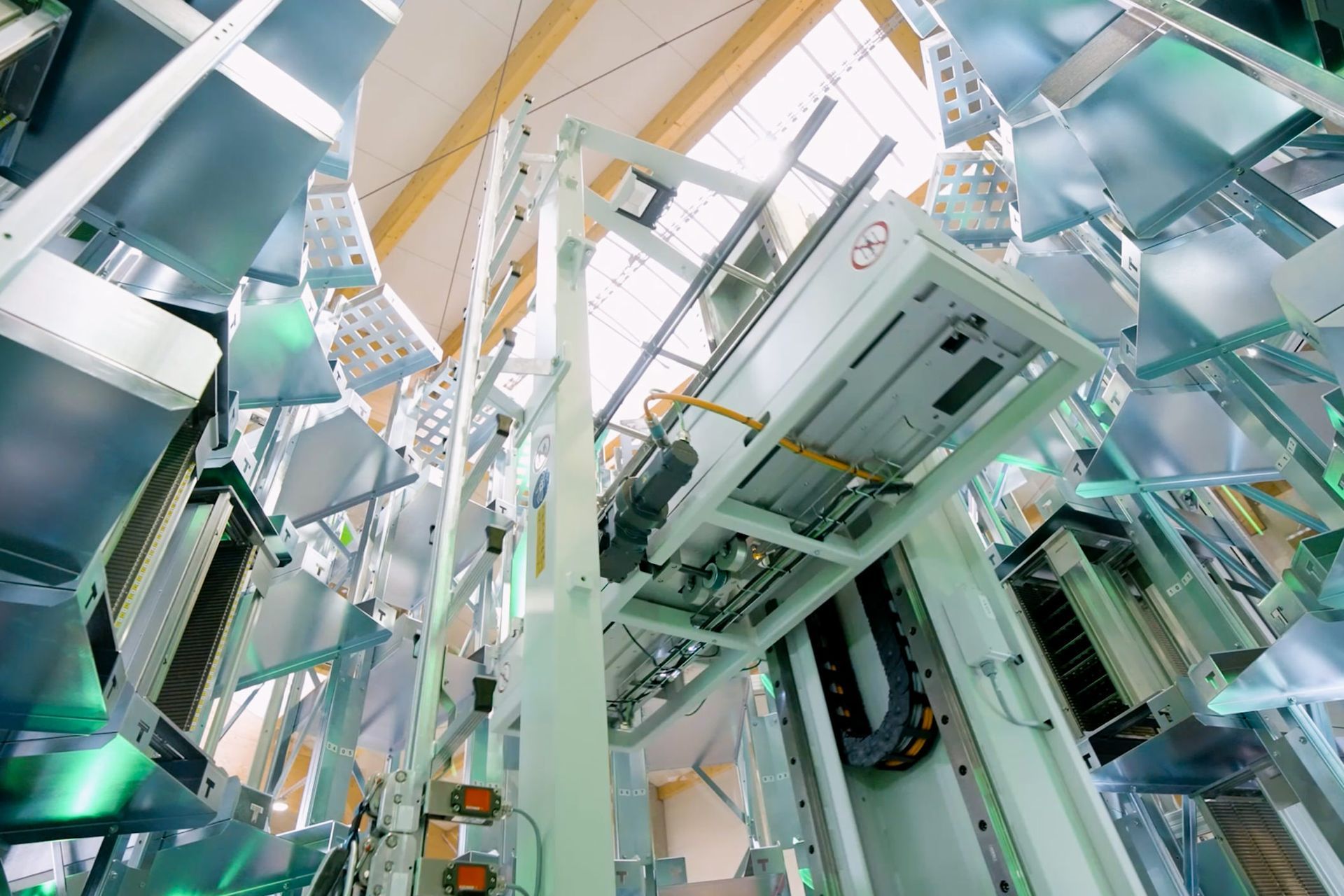
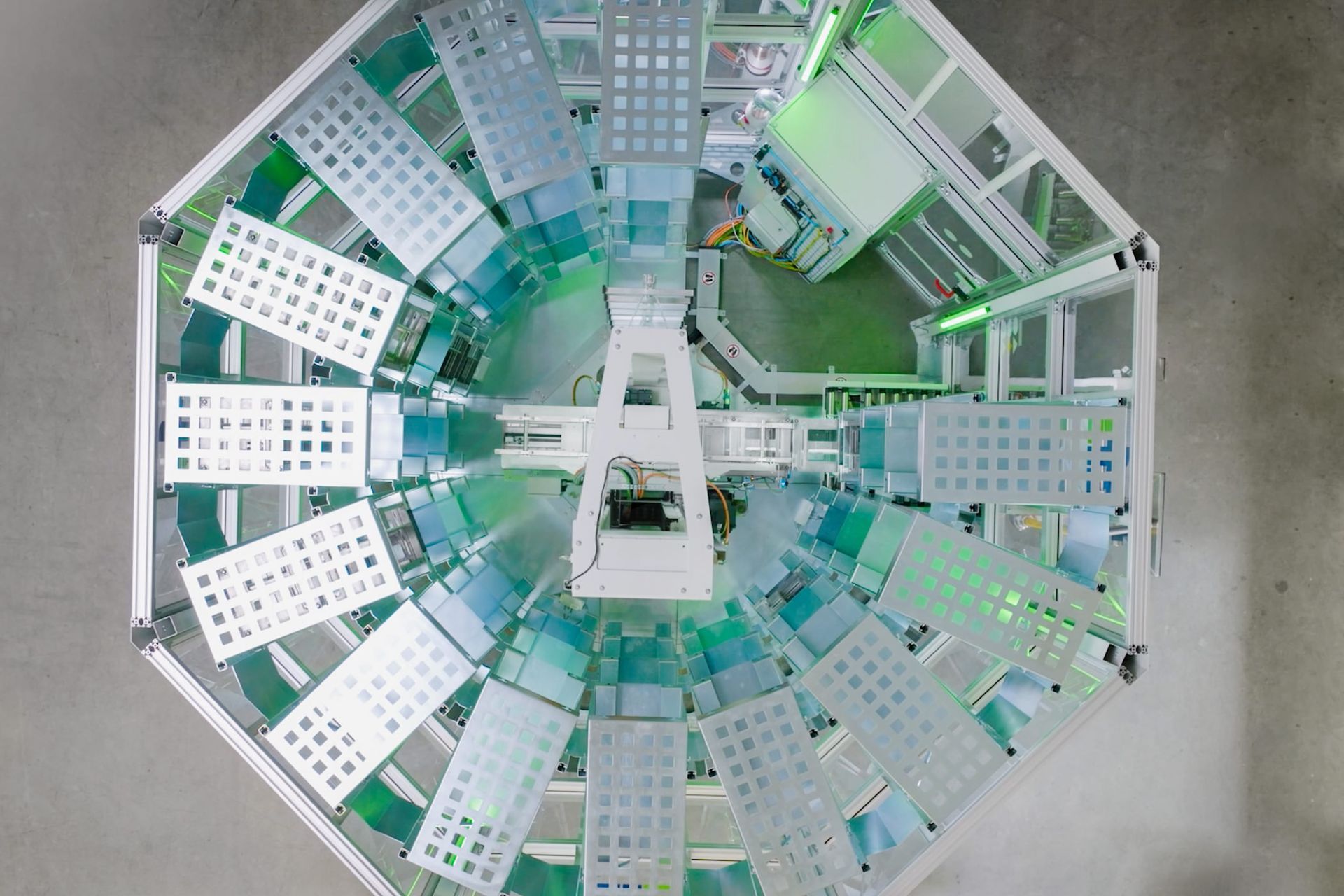
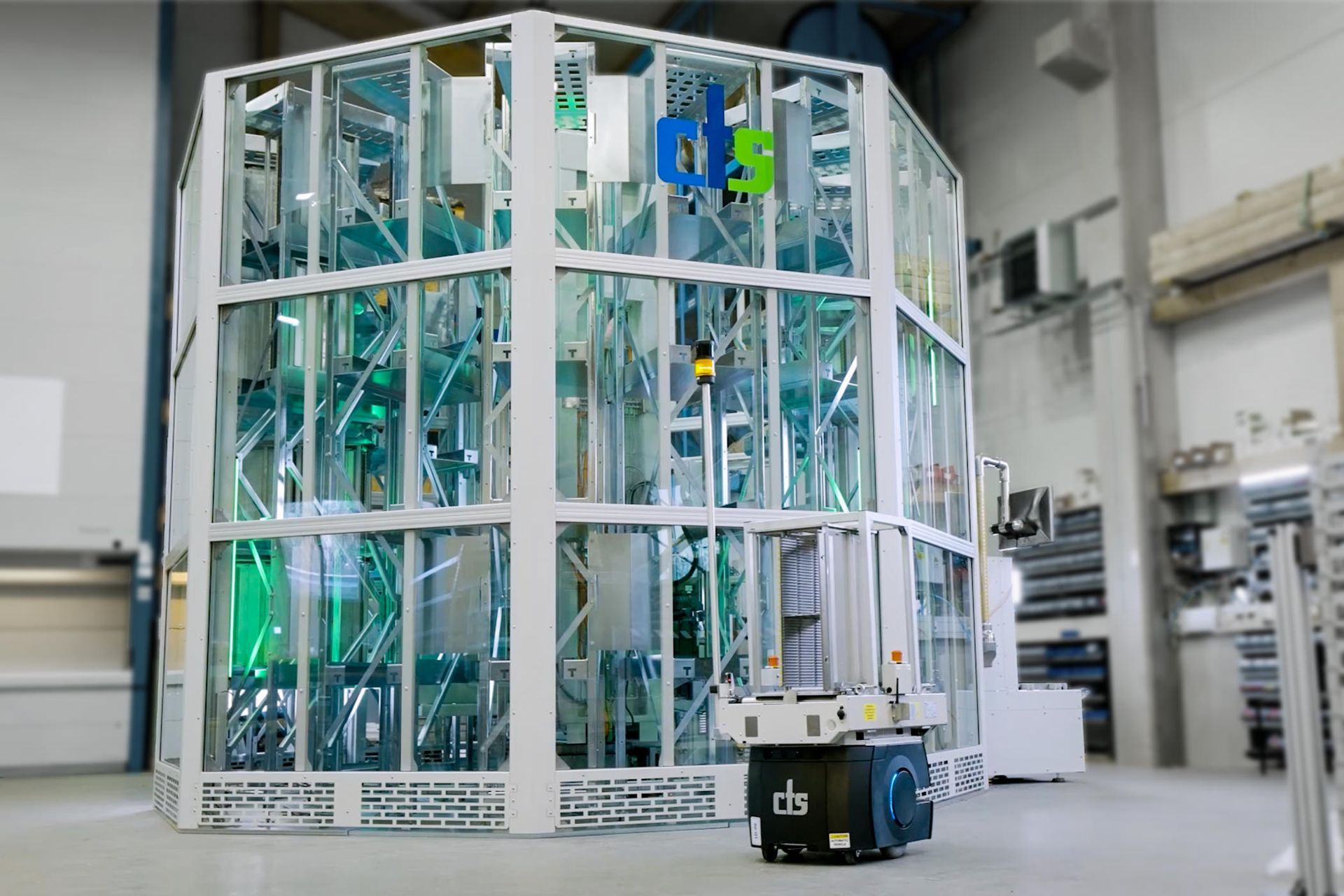
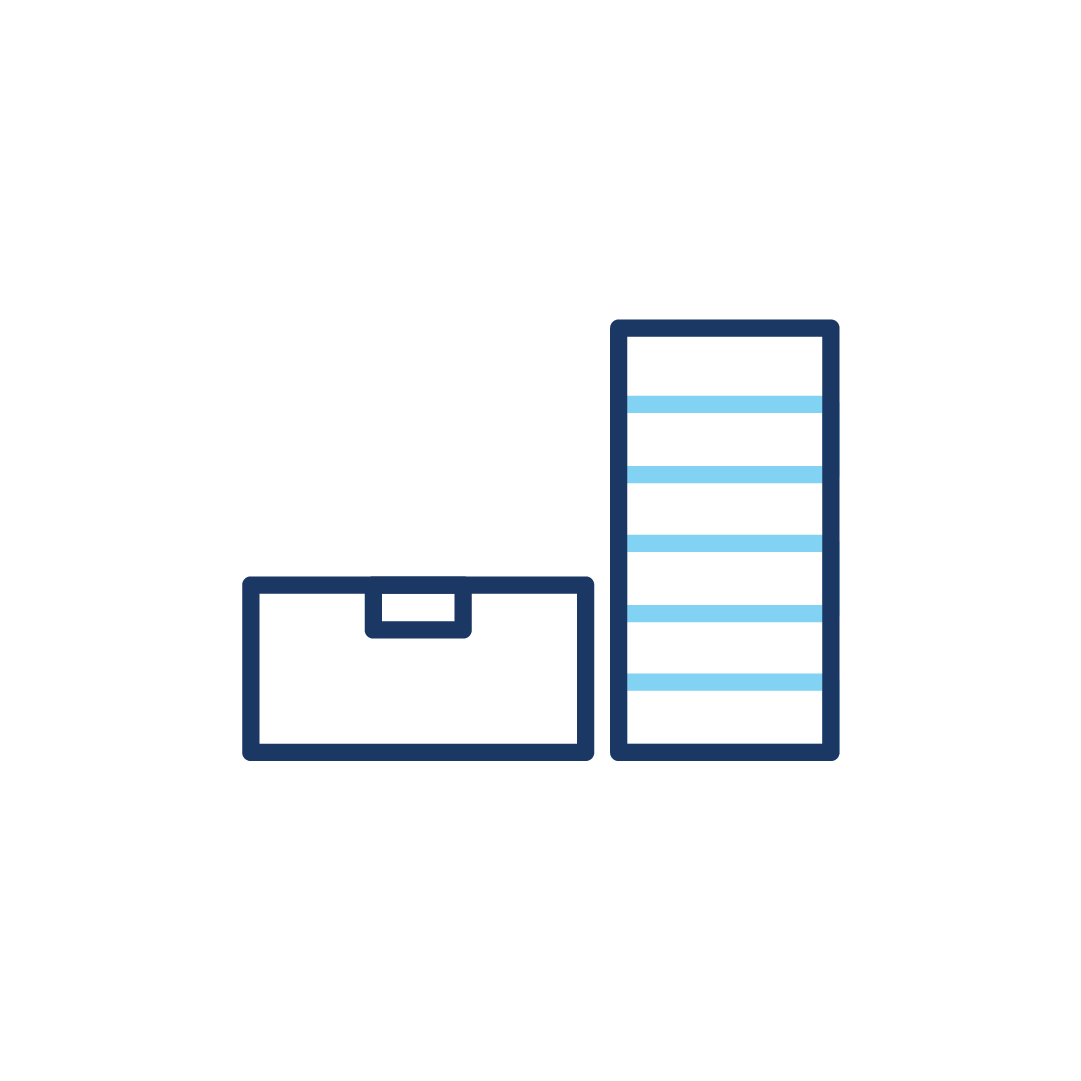
Flexible storage geometry for a wide range of container and carrier formats
Automated interfaces for direct loading and unloading at the production line
Real-time transparency through integrated tracking and tracing
Seamless integration into existing processes, systems, and factory layouts
SMART WAREHOUSE / BIG
Automated Storage System for High Material Volumes
As production volumes increase and supply chains become more complex, warehouse systems must scale accordingly.
The Smart Warehouse / Big is designed for manufacturing environments with high material throughput. It enables structured storage of large volumes and ensures continuous supply to production areas.
The system is based on a scalable racking infrastructure with fully automated loading and retrieval. If required, the material flow can be extended with autonomous transport systems. This reduces buffer zones, stabilizes processes, and shortens internal transport times.
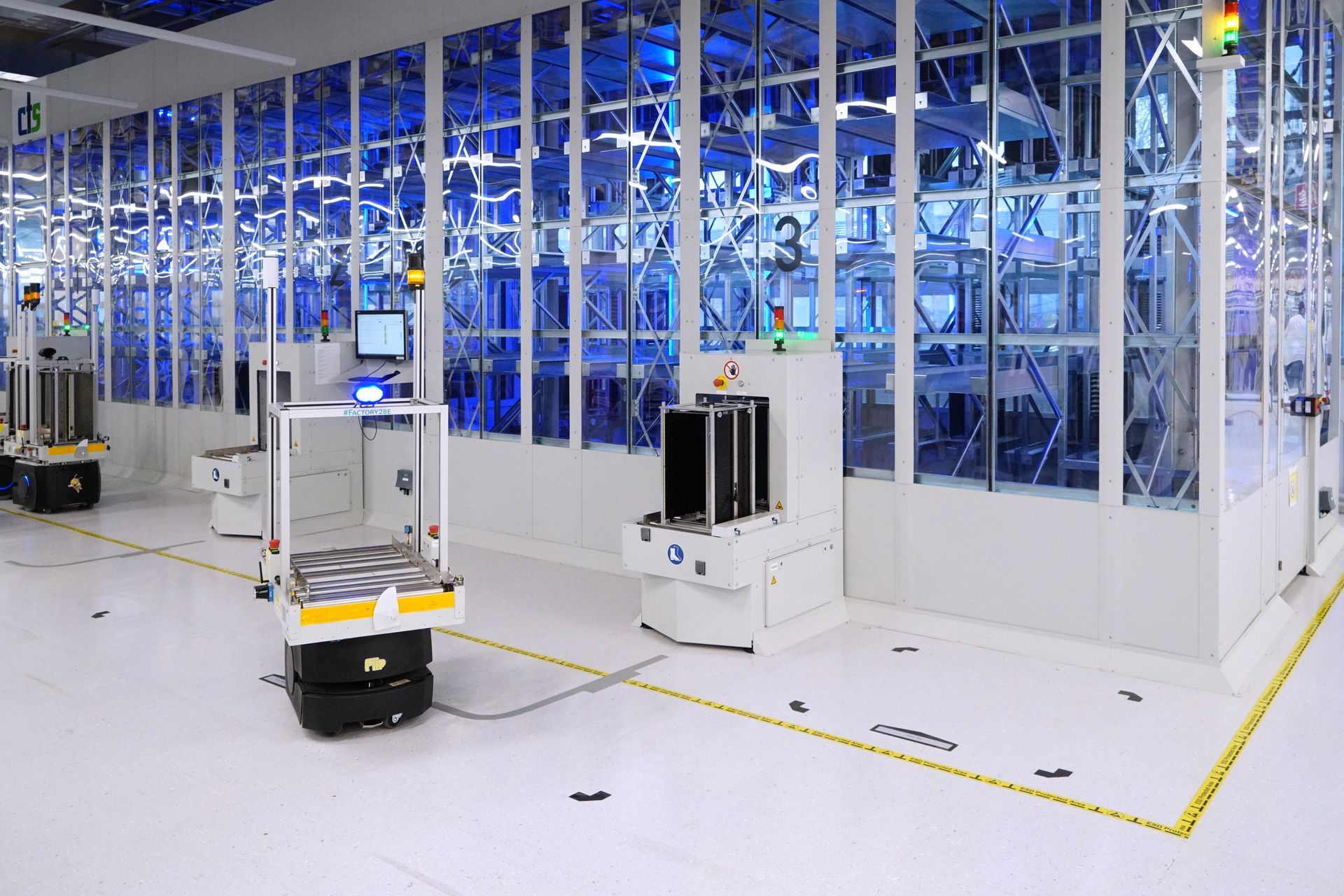
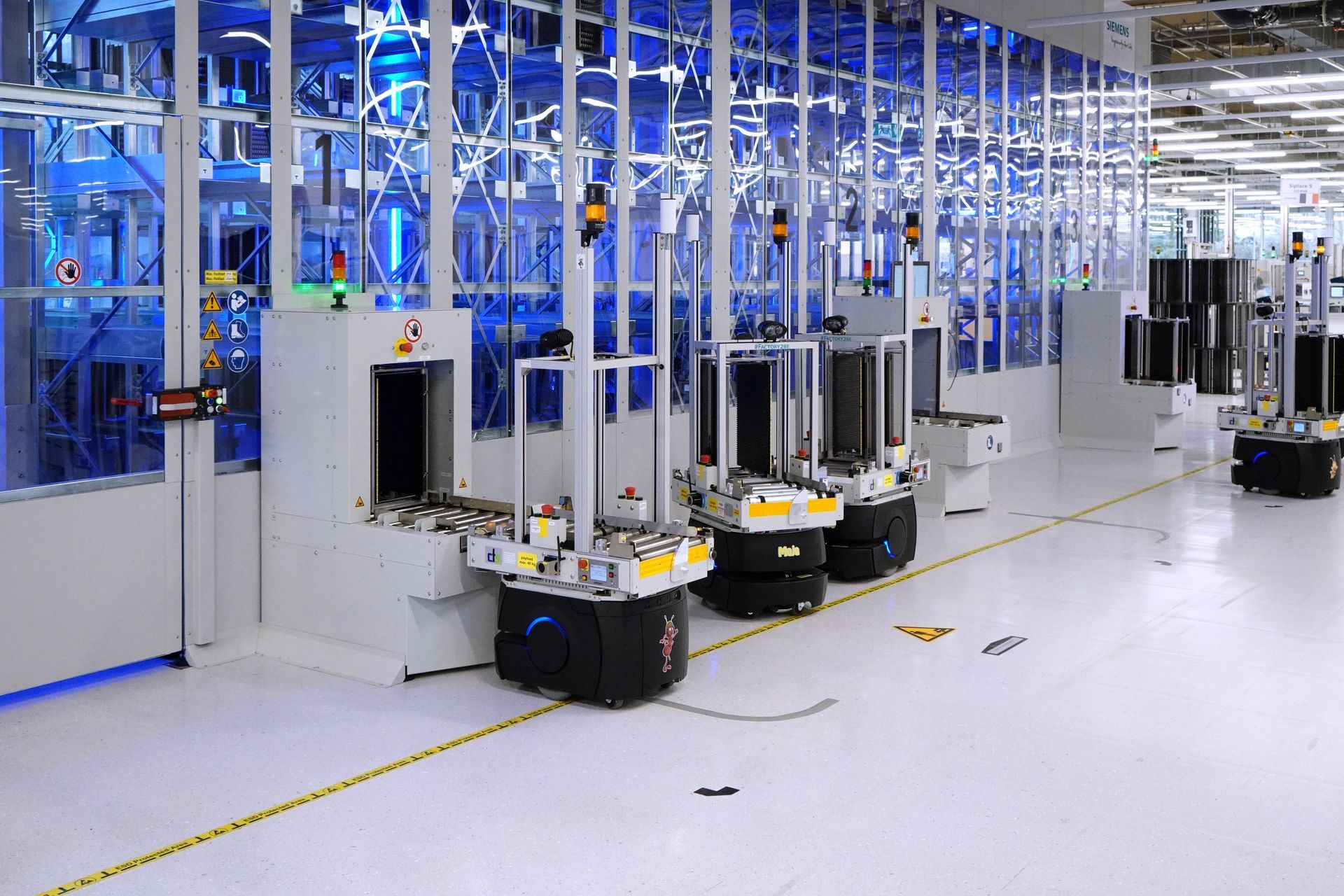
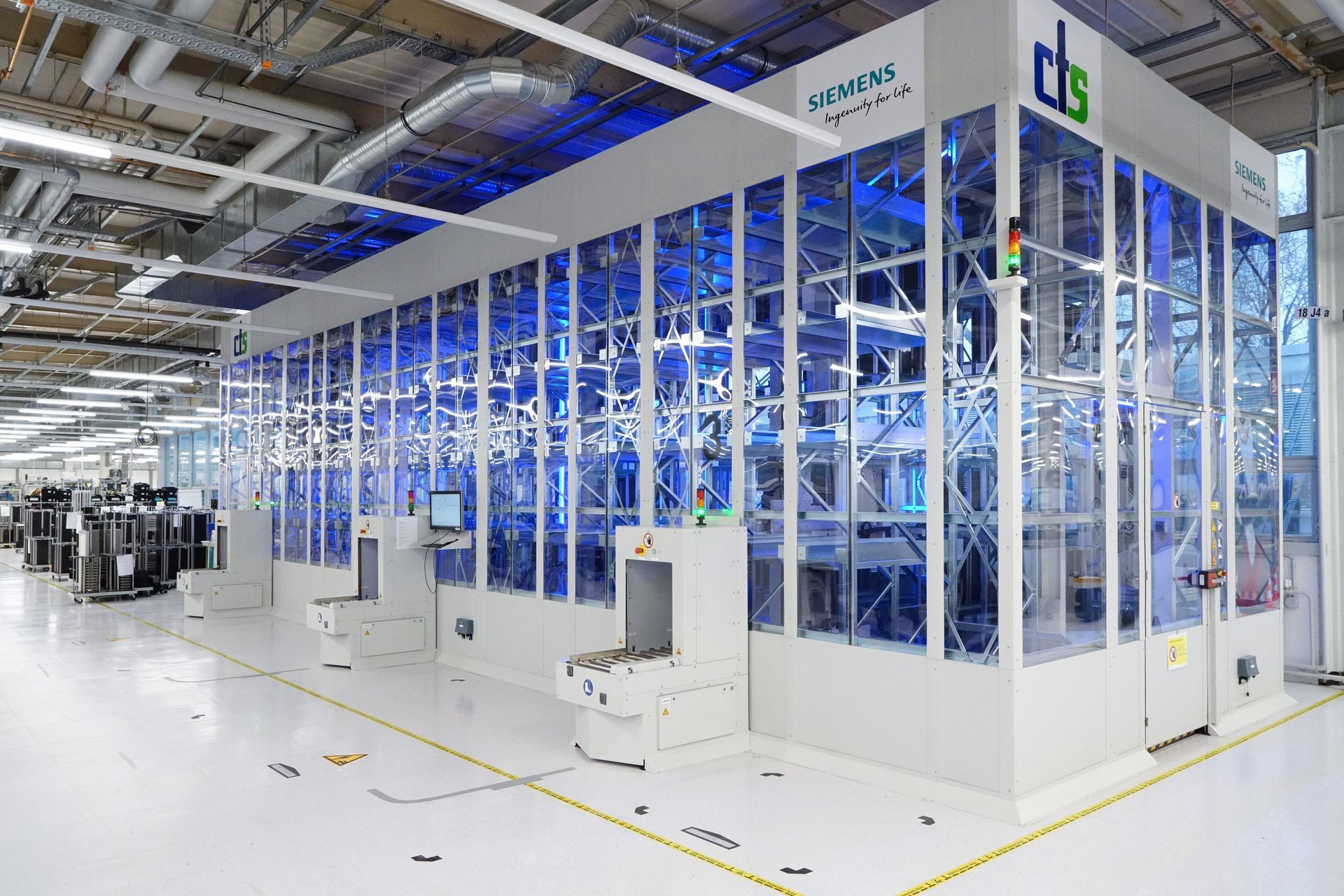
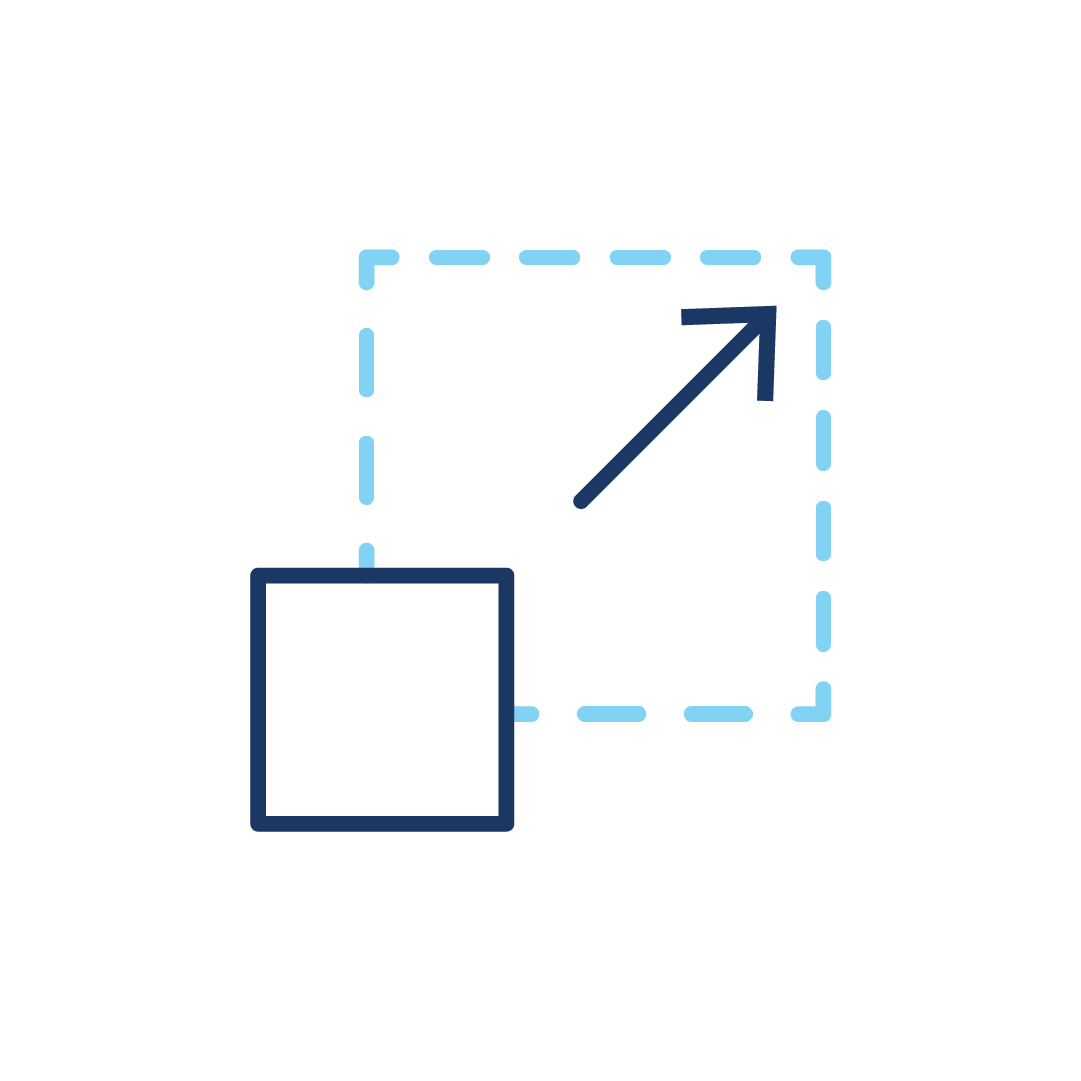
Scalable storage capacity from 400 to over 2,000 locations
Min: 8,5m x 4,5m x 4,5m
Max: 20m x 4,5 m x 8m
Automated material transport with efficient AMR integration
Compact design enabled by high-density racking and advanced gripper technology
SMART WAREHOUSE / SMT REELS
Optimized Reel Storage for SMT Production
"Designed for manufacturing" – this principle drives the efficiency of modern SMT lines. But what about the storage systems that directly impact that efficiency?
The Smart Warehouse / SMT Reels is specifically developed for the requirements of electronics manufacturing. It enables structured storage and automated provisioning of SMT component reels – with the goal of reducing setup times, stabilizing workflows, and ensuring reliable material availability.
With integrated tracking and direct connection to existing SMT lines, the system seamlessly integrates into the Smart Electronics Factory.
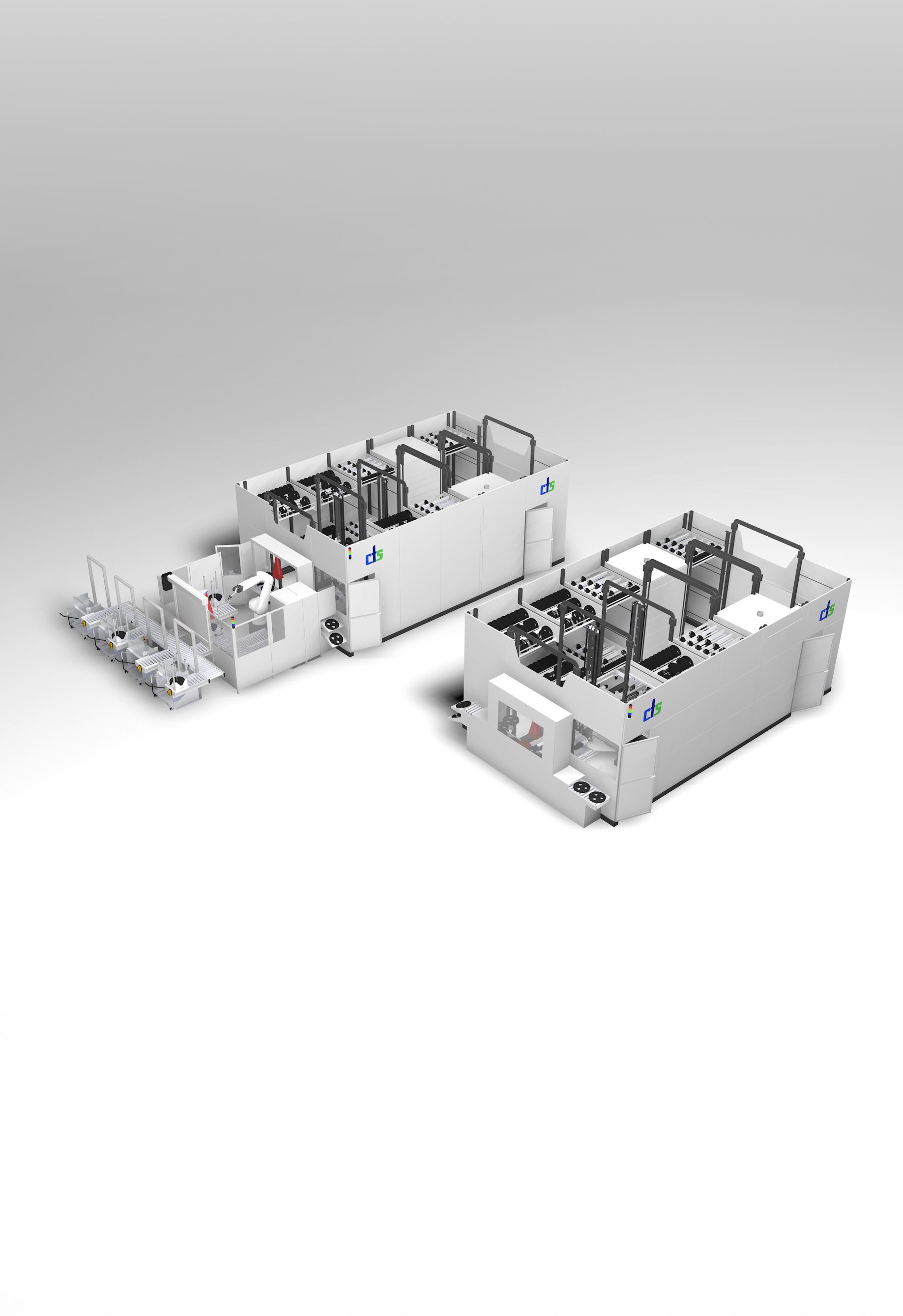
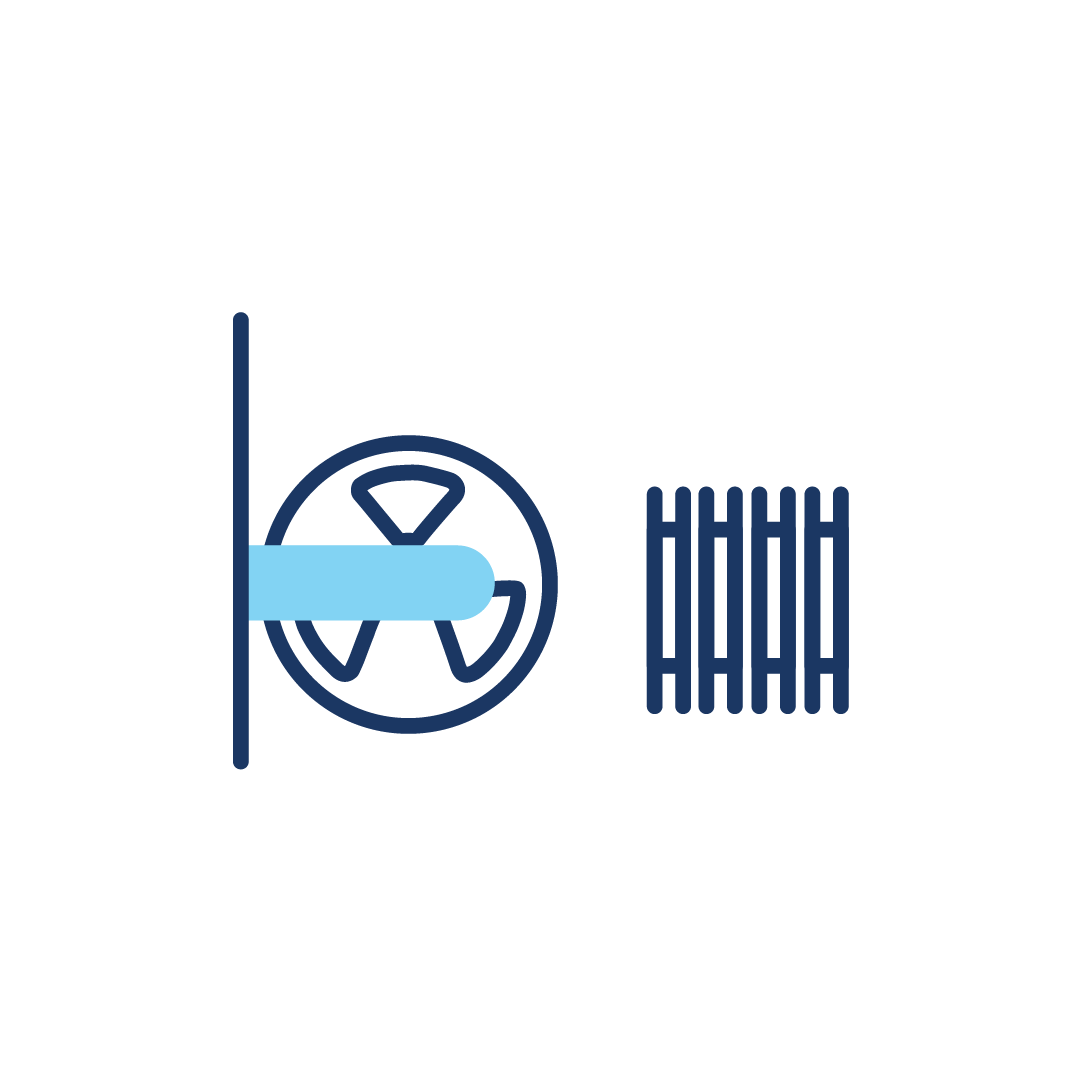
Maximum reel density with minimal footprint
Controlled storage zones for MSD-sensitive components
Central hub for material and logistics coordination
Seamless tracking and tracing of material flows
TRANSFER & BUFFER STATIONS
Temporary Buffering for Flexible Production Processes
Buffer stations are a key element in production logistics when it comes to compensating for cycle time deviations, supply bottlenecks, or fluctuating demand.
CTS offers modular transfer and buffer solutions that act as temporary storage between warehouse, production line, and transport systems – helping to stabilize internal material flows.
With automated loading and unloading interfaces, these stations can be directly connected to AMR systems or manual transport units – without the need for additional handover processes.
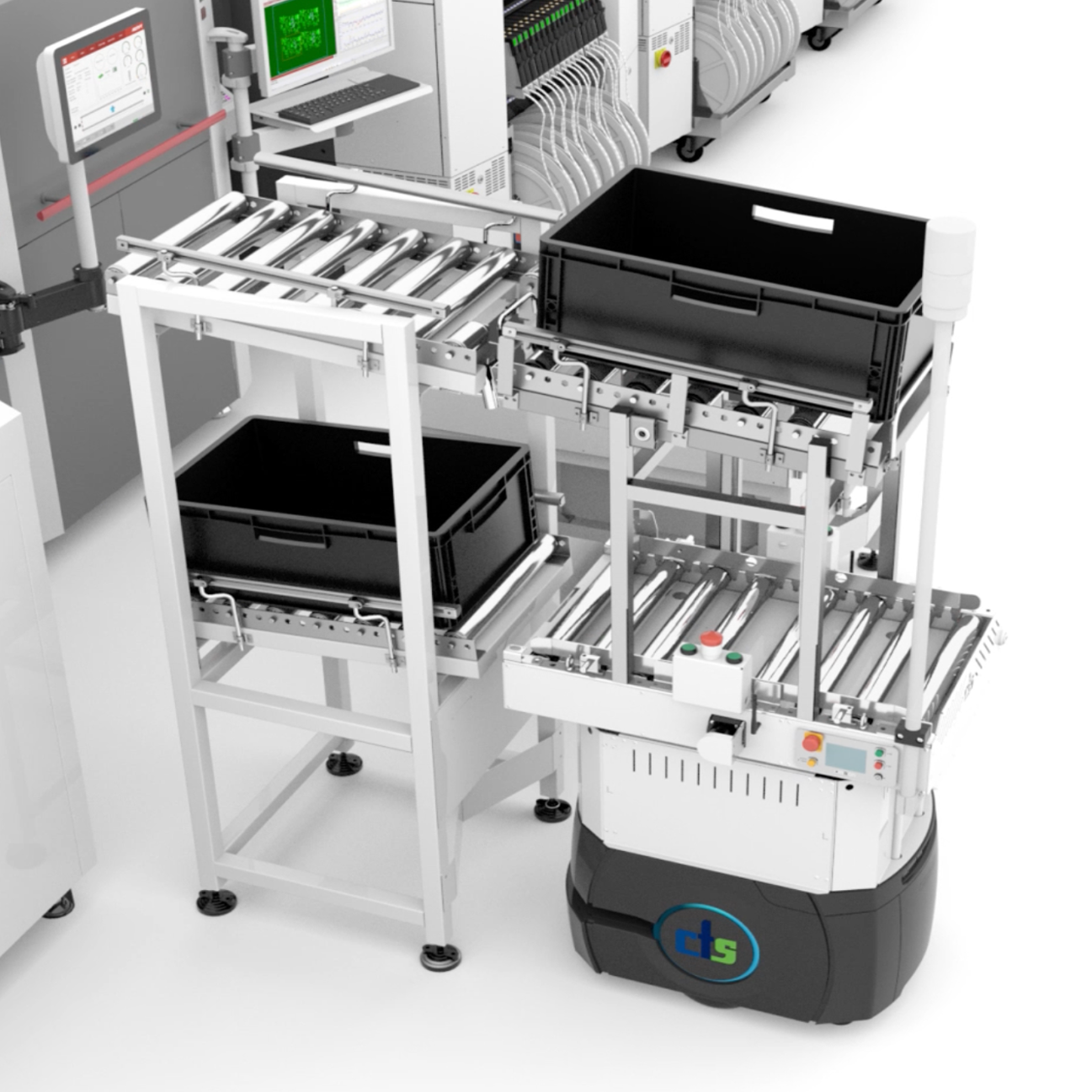
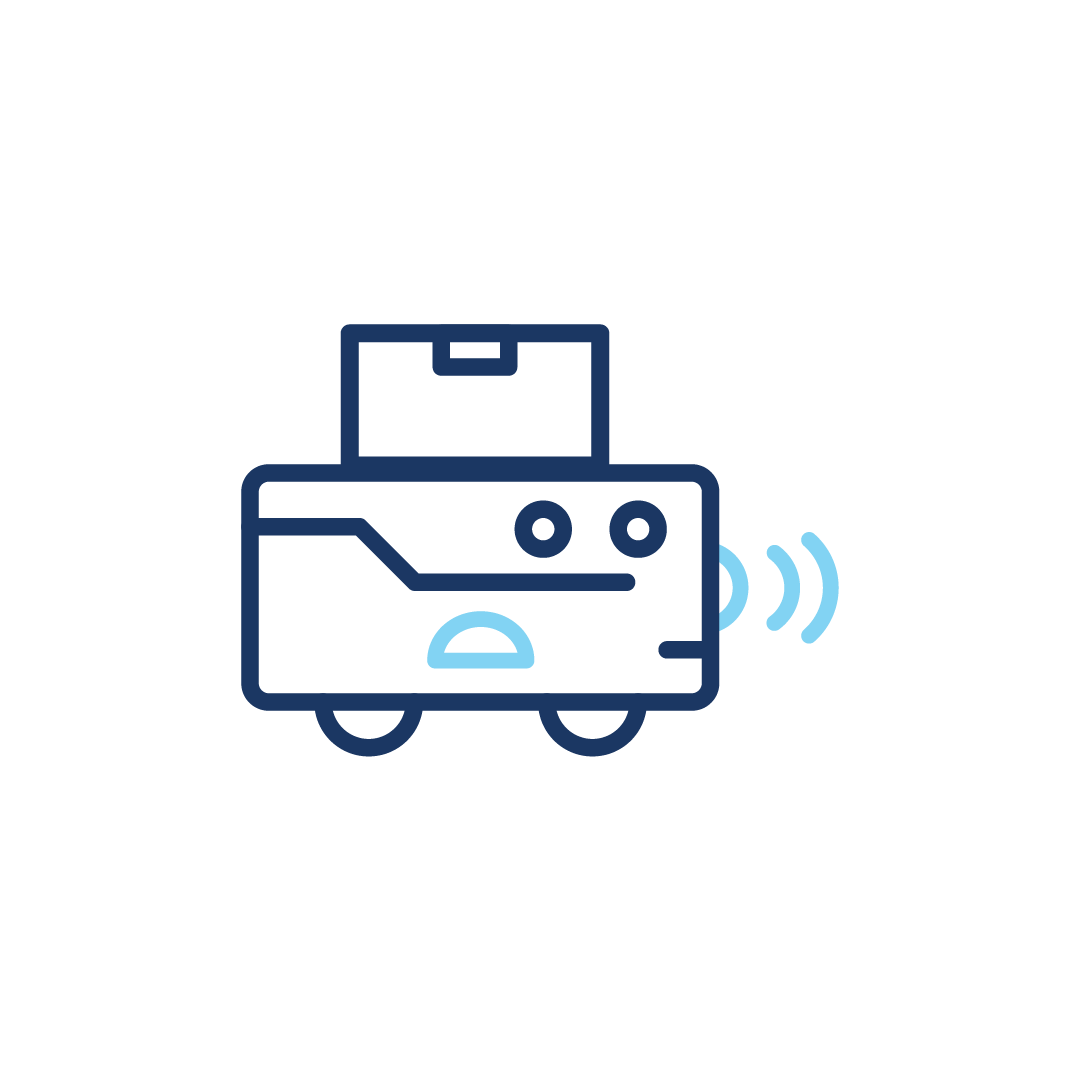
Direct AMR and conveyor integration via automated interfaces
Flexible configuration as line buffer, circulation buffer, or transfer point
Decoupling of production areas in case of asynchronous takt times
Dynamic buffering for parts, containers, or carriers
AUTONOUS MOBILE ROBOTS
Transport Solutions for Flexible, Decoupled Production Environments
Autonomous Mobile Robots (AMRs) handle repetitive transport tasks within production – reliably, flexibly, and without manual intervention.
They connect warehouses, buffers, and handover stations directly to the consumption points along the line, ensuring a continuous and synchronized material supply.
AMRs navigate freely in dynamic environments, adapt their routes in real time, and remain operational even as layouts change. By integrating AMRs, internal transport processes become standardized – relieving personnel from non-value-adding tasks.
CTS implements AMR solutions in collaboration with partners such as Omron, Agilox and MiR – vendor-neutral and tailored to your infrastructure. Existing systems can be integrated via modular interfaces.
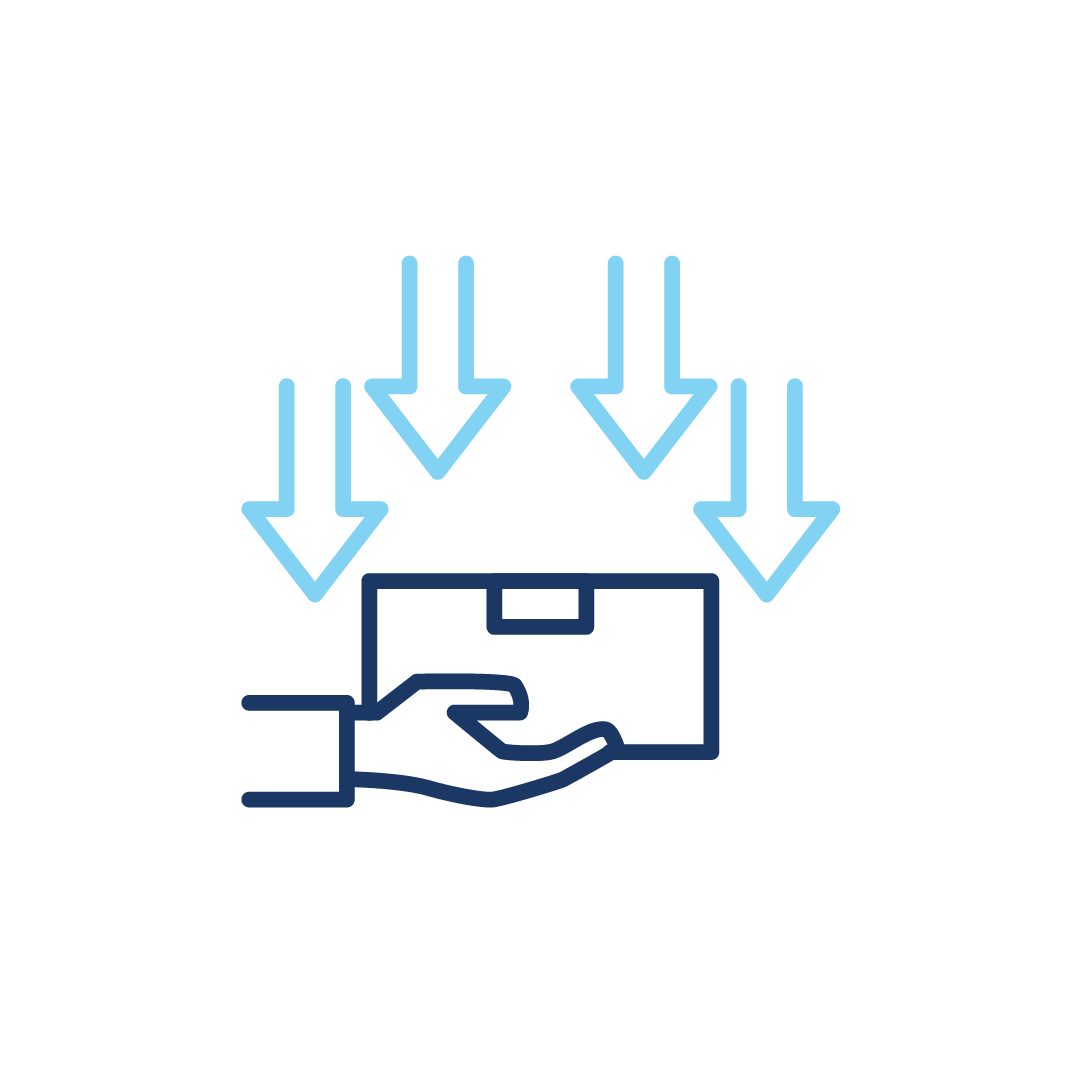
Reduction of manual transports and empty runs
Personnel relief through automated material staging
Scalable deployment for changing production requirements
Just-in-time line supply with components, carriers, or containers
sloXis – Middleware for Connected Material Supply
Seamless Integration of CTS Systems into Your Existing ERP or MES Setup
sloXis is not a new control layer – it’s an integration middleware that connects existing ERP, MES, WMS, and CTS systems to enable automated material flows across your factory.
The platform processes data such as order information, inventory levels, or machine statuses and translates it into actionable commands for CTS systems like storage units, buffer stations, or AMRs – from inbound logistics to precise line-side delivery. This enables demand-driven, real-time material handling without interfering with your core IT infrastructure.
Integration is vendor-agnostic and supported through standard interfaces or custom-developed connectors – making sloXis suitable for new and legacy production environments alike.
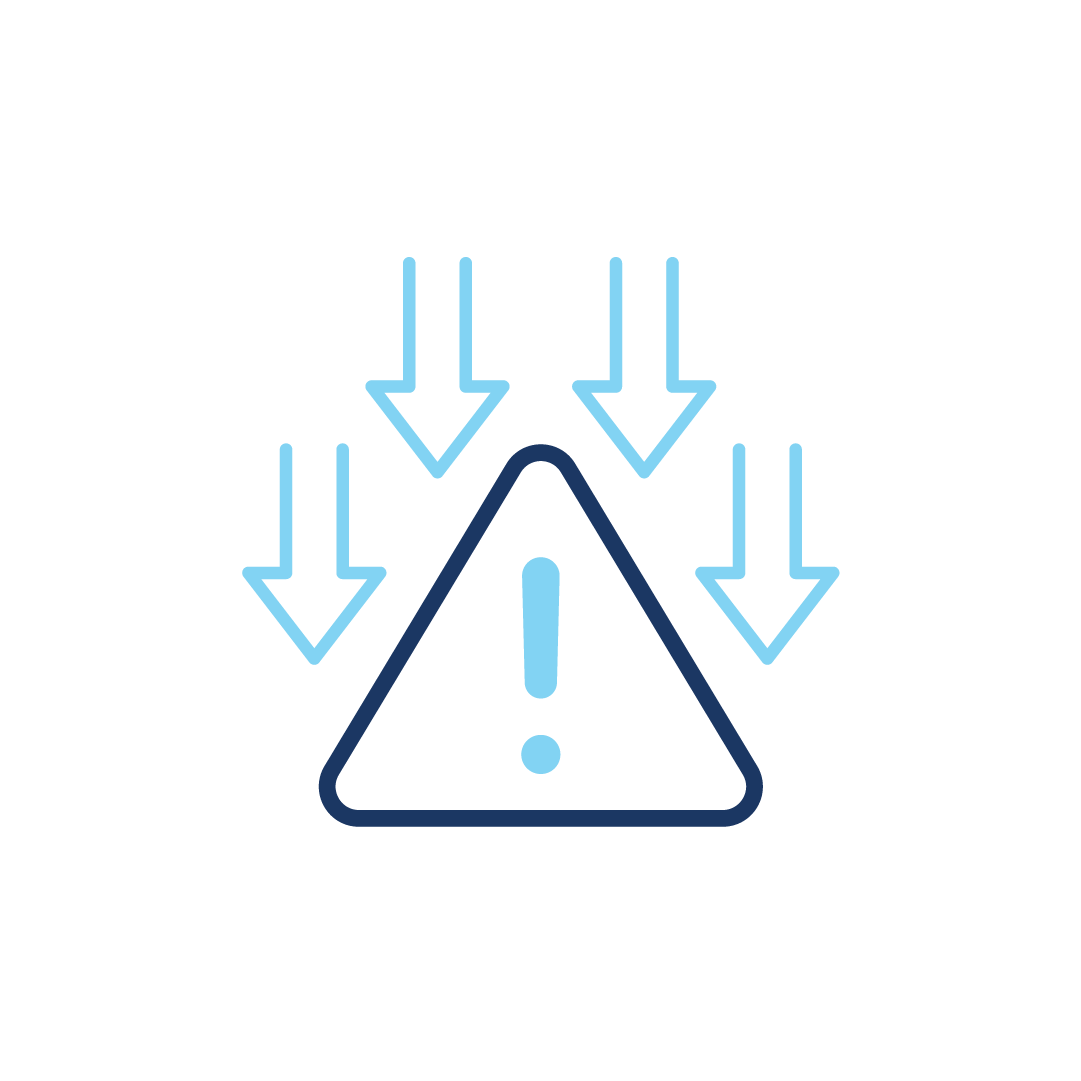
No interference with existing control systems
Middleware interface between ERP, MES, WMS & CTS automation
Automated material flow execution across storage and transport systems
Flexible integration via standard protocols or tailored adapters
SMART WAREHOUSE / BIG
Automated Storage System for High Material Volumes
As production volumes increase and supply chains become more complex, warehouse systems must scale accordingly.
The Smart Warehouse / Big is designed for manufacturing environments with high material throughput. It enables structured storage of large volumes and ensures continuous supply to production areas.
The system is based on a scalable racking infrastructure with fully automated loading and retrieval. If required, the material flow can be extended with autonomous transport systems. This reduces buffer zones, stabilizes processes, and shortens internal transport times.
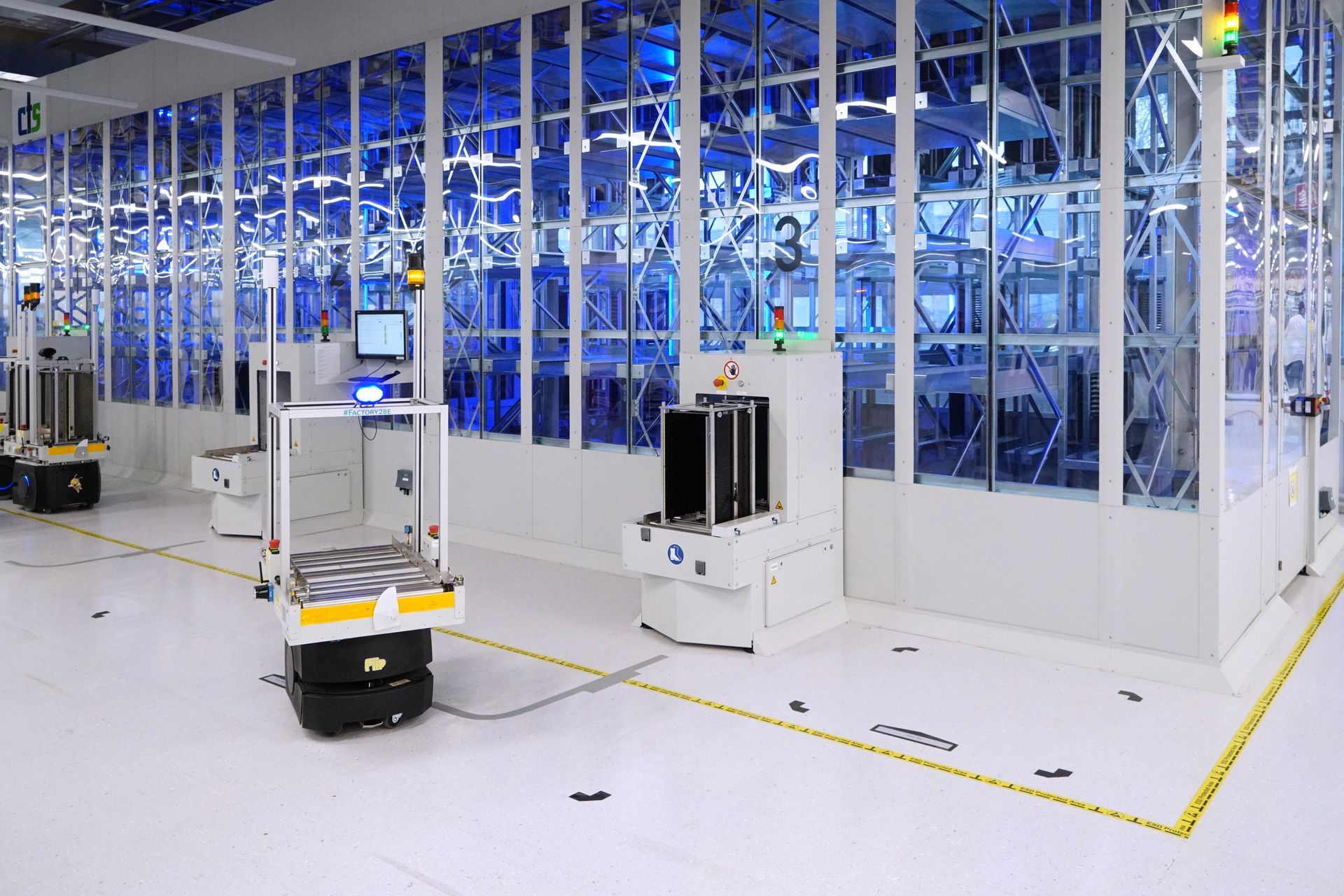
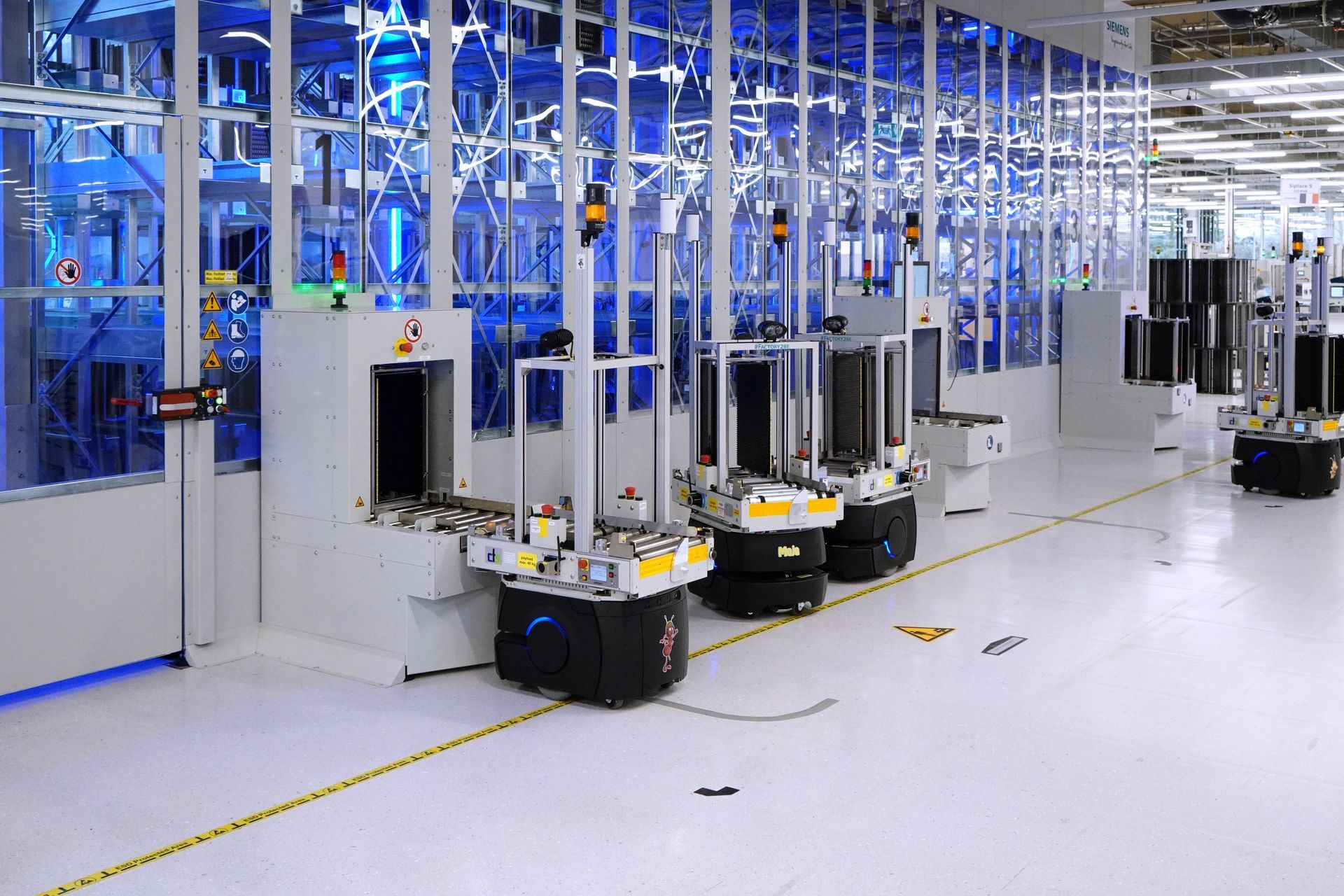
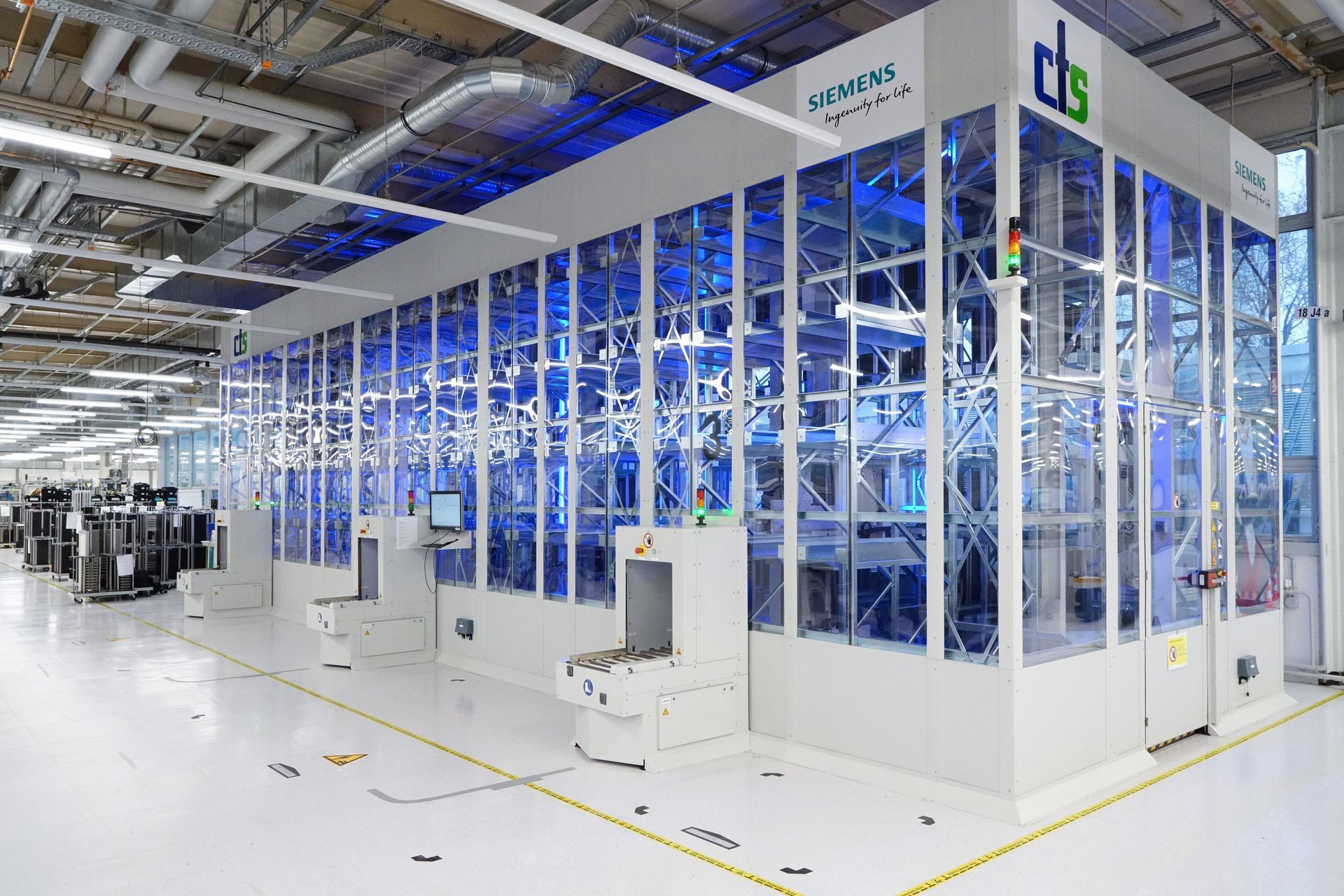
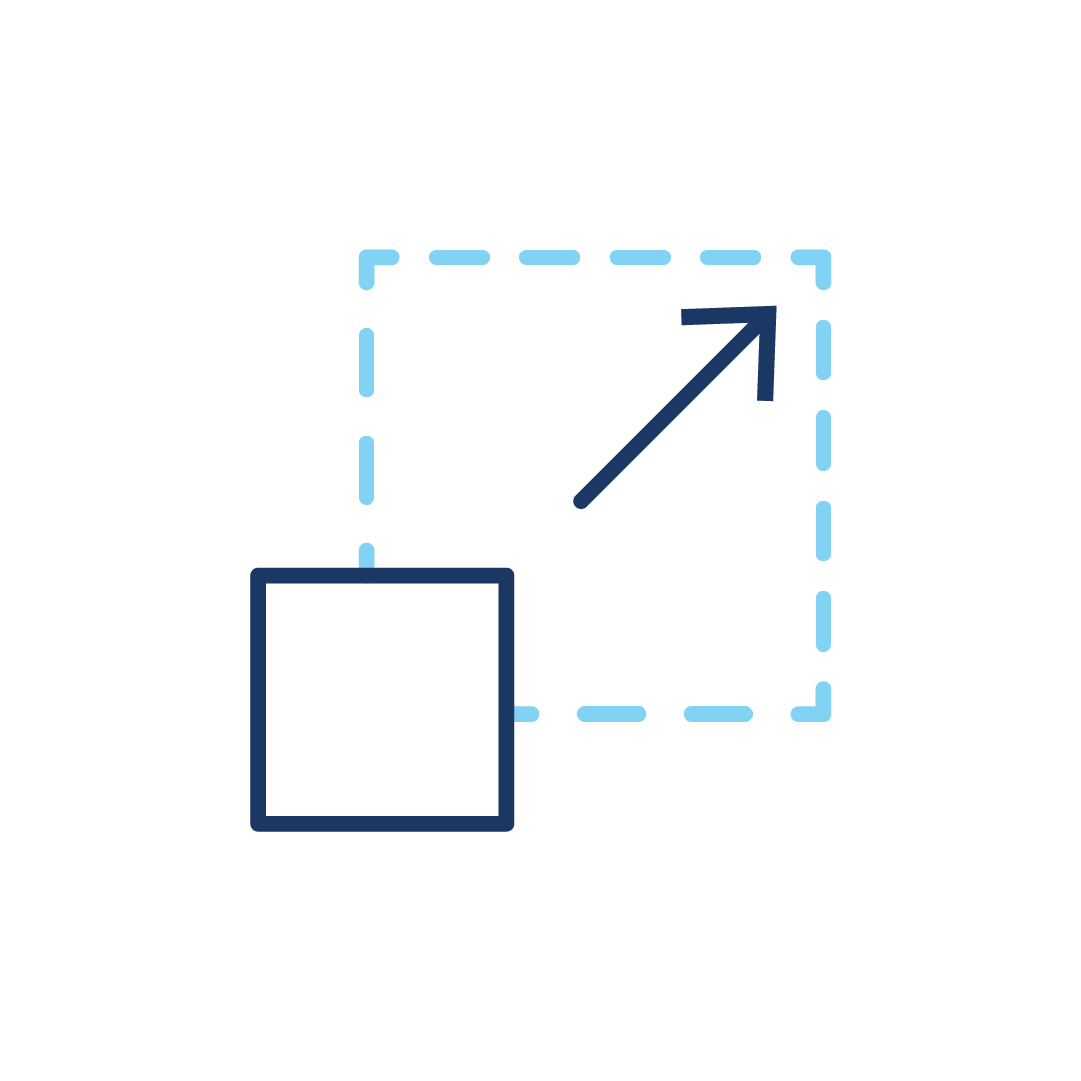
Scalable storage capacity from 400 to over 2,000 locations
Min: 8,5m x 4,5m x 4,5m
Max: 20m x 4,5 m x 8m
Automated material transport with efficient AMR integration
Compact design enabled by high-density racking and advanced gripper technology
SMART WAREHOUSE / SMT REELS
Optimized Reel Storage for SMT Production
"Designed for manufacturing" – this principle drives the efficiency of modern SMT lines. But what about the storage systems that directly impact that efficiency?
The Smart Warehouse / SMT Reels is specifically developed for the requirements of electronics manufacturing. It enables structured storage and automated provisioning of SMT component reels – with the goal of reducing setup times, stabilizing workflows, and ensuring reliable material availability.
With integrated tracking and direct connection to existing SMT lines, the system seamlessly integrates into the Smart Electronics Factory.
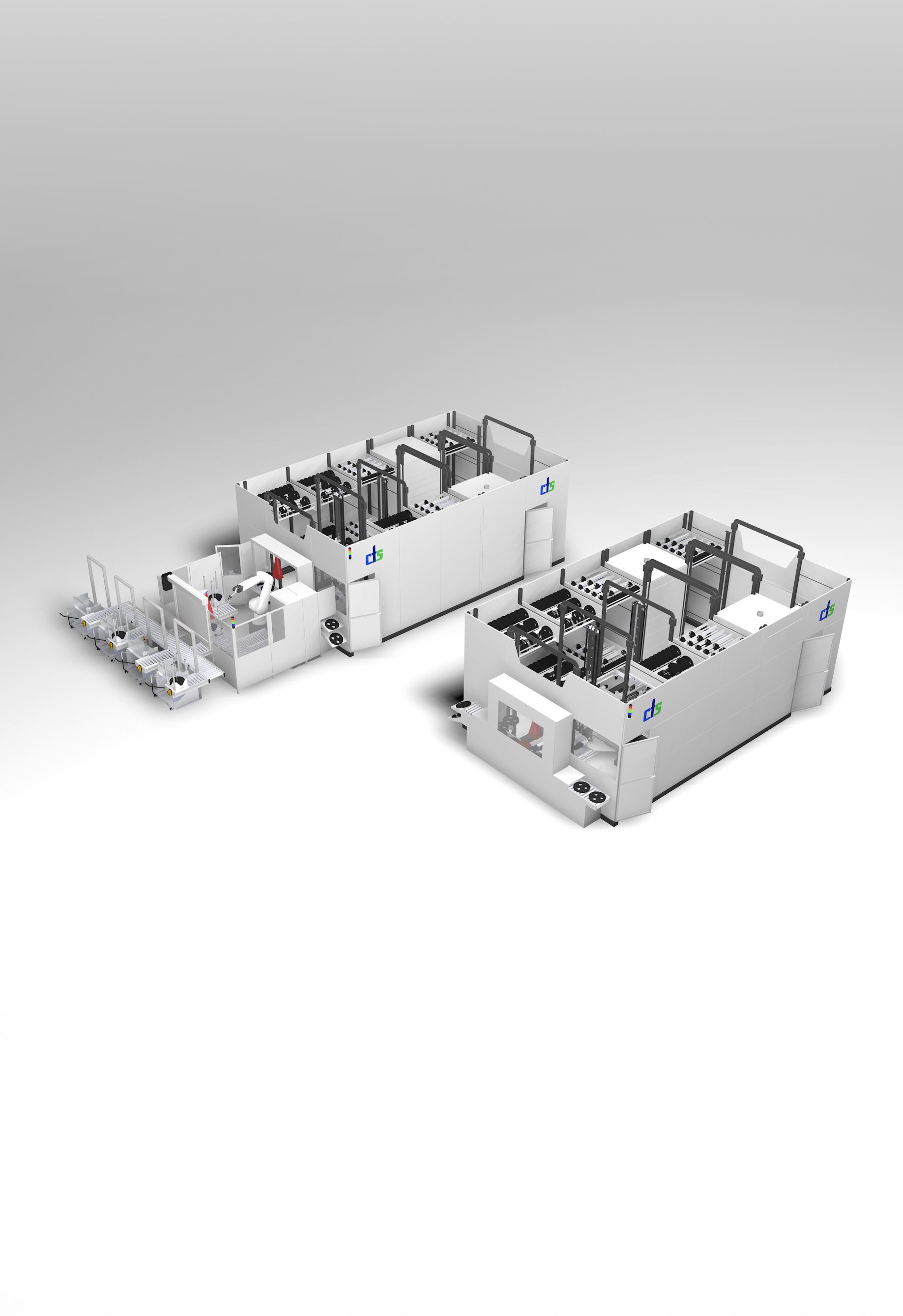
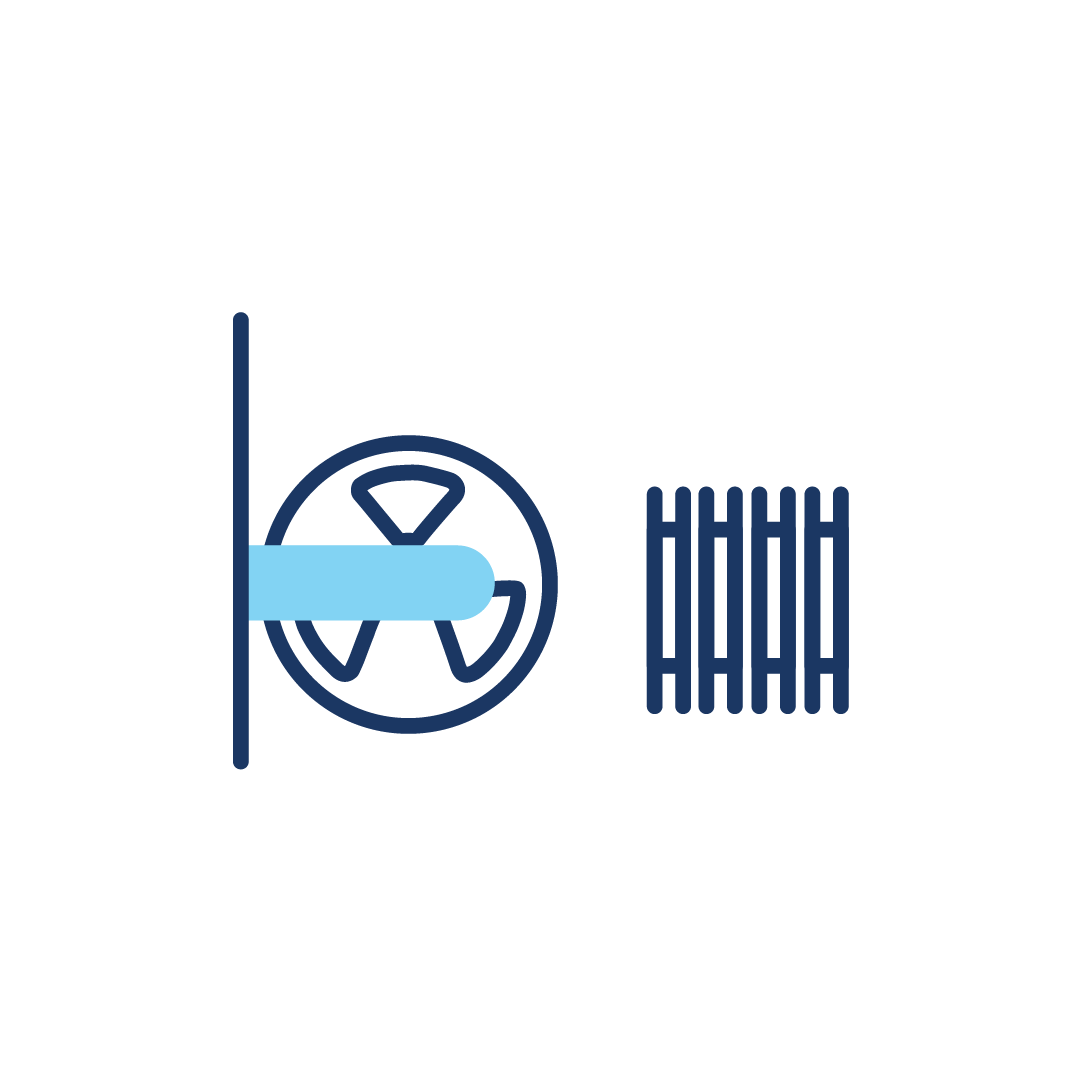
Maximum reel density with minimal footprint
Controlled storage zones for MSD-sensitive components
Central hub for material and logistics coordination
Seamless tracking and tracing of material flows
TRANSFER & BUFFER STATIONS
Temporary Buffering for Flexible Production Processes
Buffer stations are a key element in production logistics when it comes to compensating for cycle time deviations, supply bottlenecks, or fluctuating demand.
CTS offers modular transfer and buffer solutions that act as temporary storage between warehouse, production line, and transport systems – helping to stabilize internal material flows.
With automated loading and unloading interfaces, these stations can be directly connected to AMR systems or manual transport units – without the need for additional handover processes.
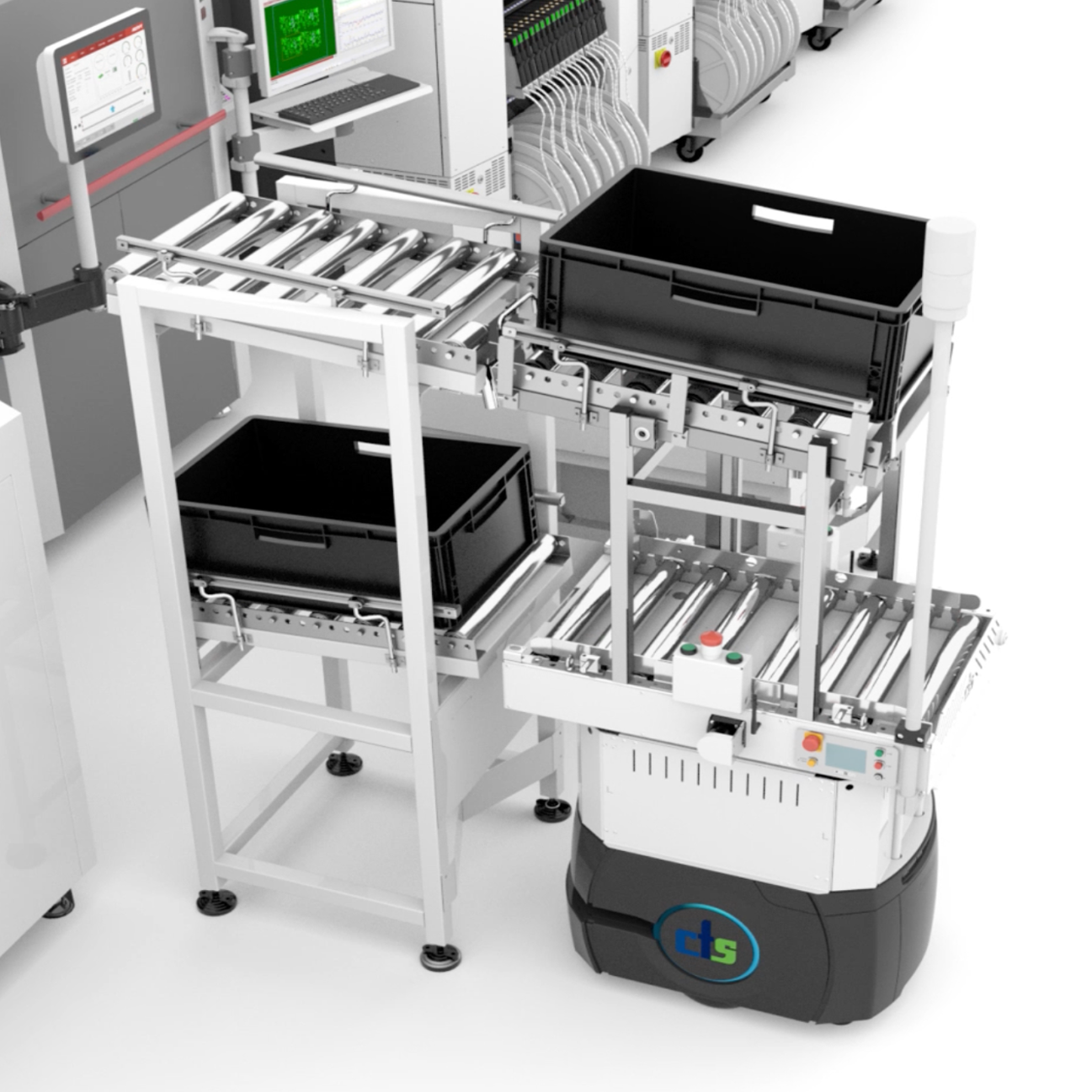
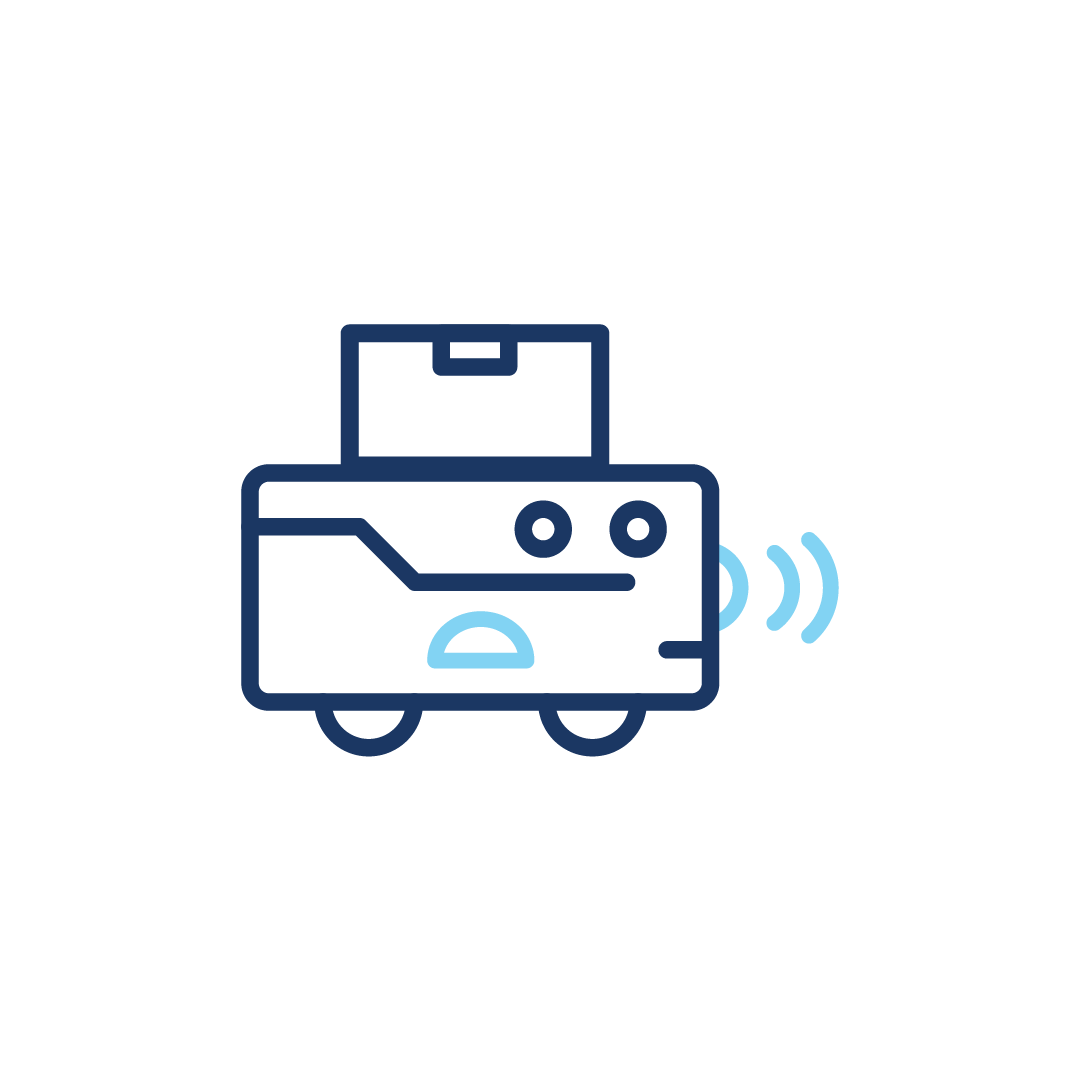
Direct AMR and conveyor integration via automated interfaces
Flexible configuration as line buffer, circulation buffer, or transfer point
Decoupling of production areas in case of asynchronous takt times
Dynamic buffering for parts, containers, or carriers
AUTONOUS MOBILE ROBOTS
Transport Solutions for Flexible, Decoupled Production Environments
Autonomous Mobile Robots (AMRs) handle repetitive transport tasks within production – reliably, flexibly, and without manual intervention.
They connect warehouses, buffers, and handover stations directly to the consumption points along the line, ensuring a continuous and synchronized material supply.
AMRs navigate freely in dynamic environments, adapt their routes in real time, and remain operational even as layouts change. By integrating AMRs, internal transport processes become standardized – relieving personnel from non-value-adding tasks.
CTS implements AMR solutions in collaboration with partners such as Omron, Agilox and MiR – vendor-neutral and tailored to your infrastructure. Existing systems can be integrated via modular interfaces.
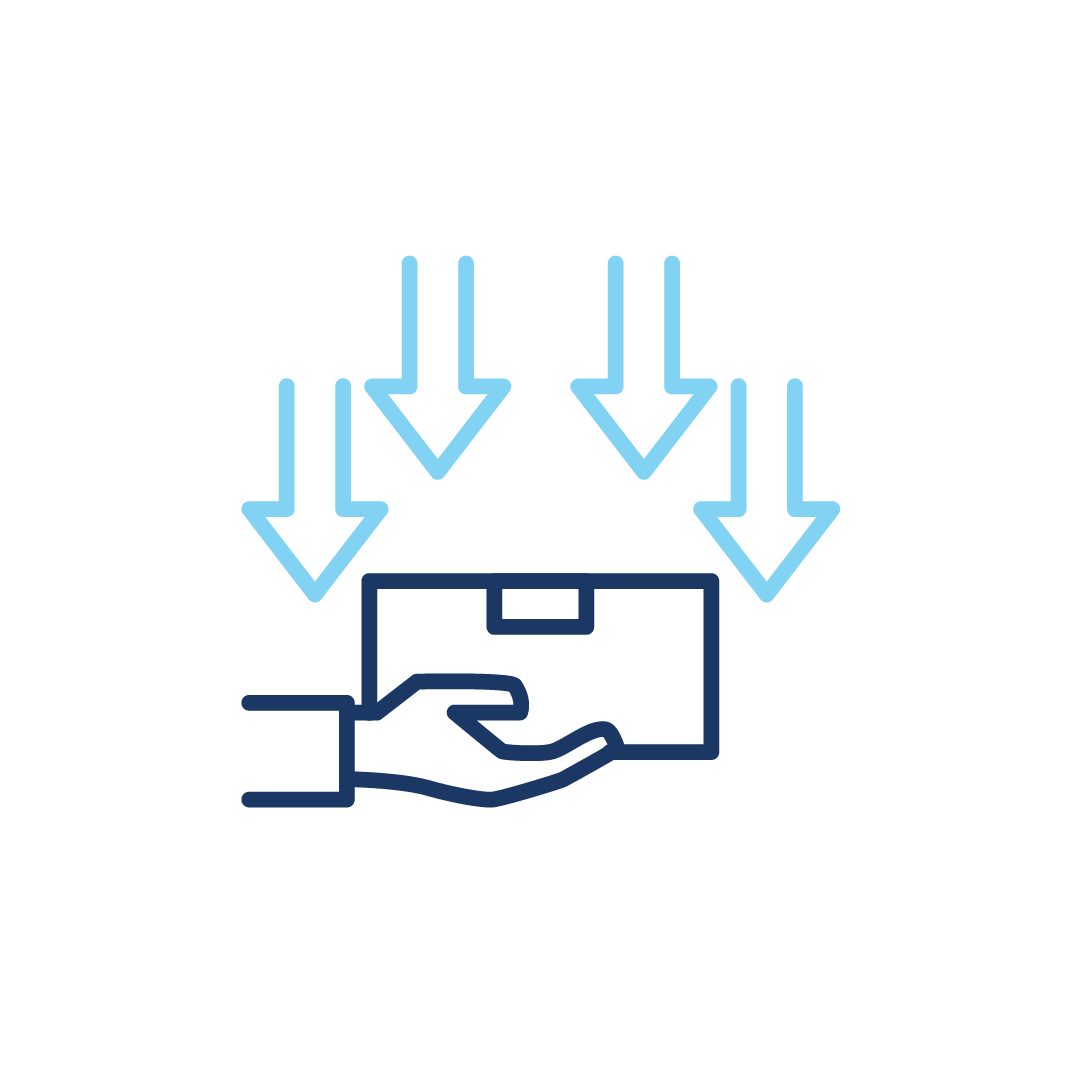
Reduction of manual transports and empty runs
Personnel relief through automated material staging
Scalable deployment for changing production requirements
Just-in-time line supply with components, carriers, or containers
Seamless Integration of CTS Systems into Your Existing ERP or MES Setup
sloXis – Middleware for Connected Material Supply
sloXis is not a new control layer – it’s an integration middleware that connects existing ERP, MES, WMS, and CTS systems to enable automated material flows across your factory.
The platform processes data such as order information, inventory levels, or machine statuses and translates it into actionable commands for CTS systems like storage units, buffer stations, or AMRs – from inbound logistics to precise line-side delivery. This enables demand-driven, real-time material handling without interfering with your core IT infrastructure.
Integration is vendor-agnostic and supported through standard interfaces or custom-developed connectors – making sloXis suitable for new and legacy production environments alike.
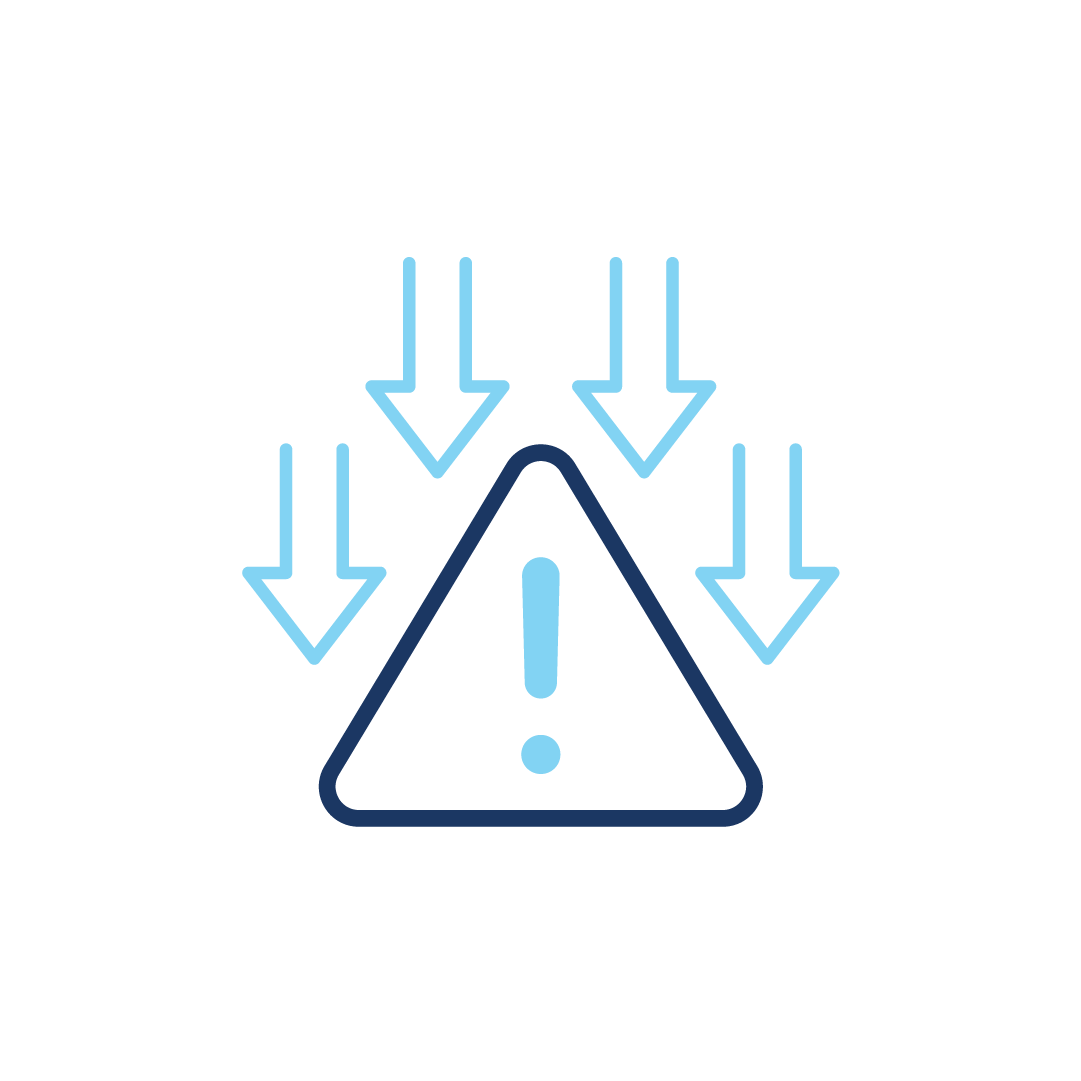
No interference with existing control systems
Middleware interface between ERP, MES, WMS & CTS automation
Automated material flow execution across storage and transport systems
Flexible integration via standard protocols or tailored adapters
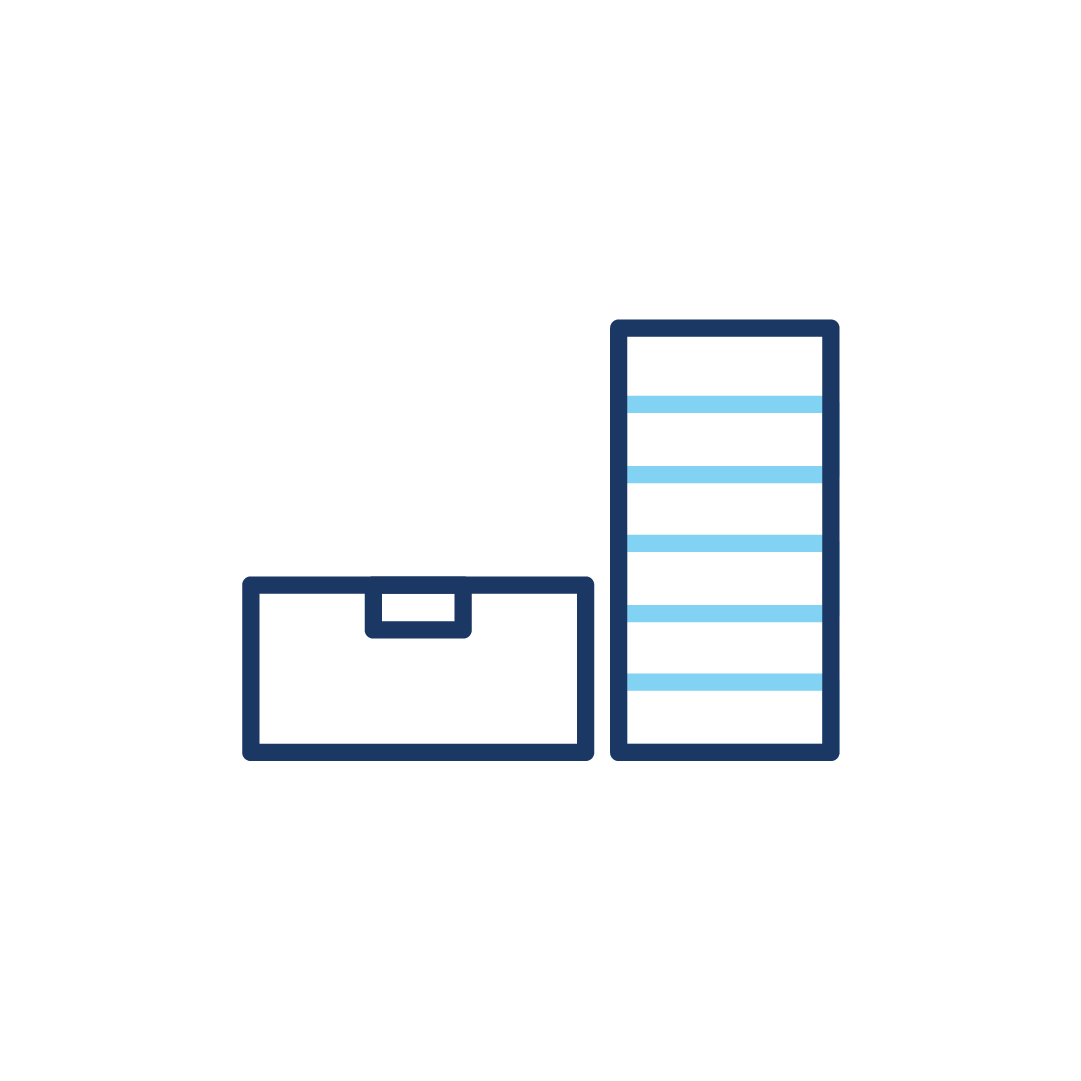
Flexible storage geometry for a wide range of container and carrier formats
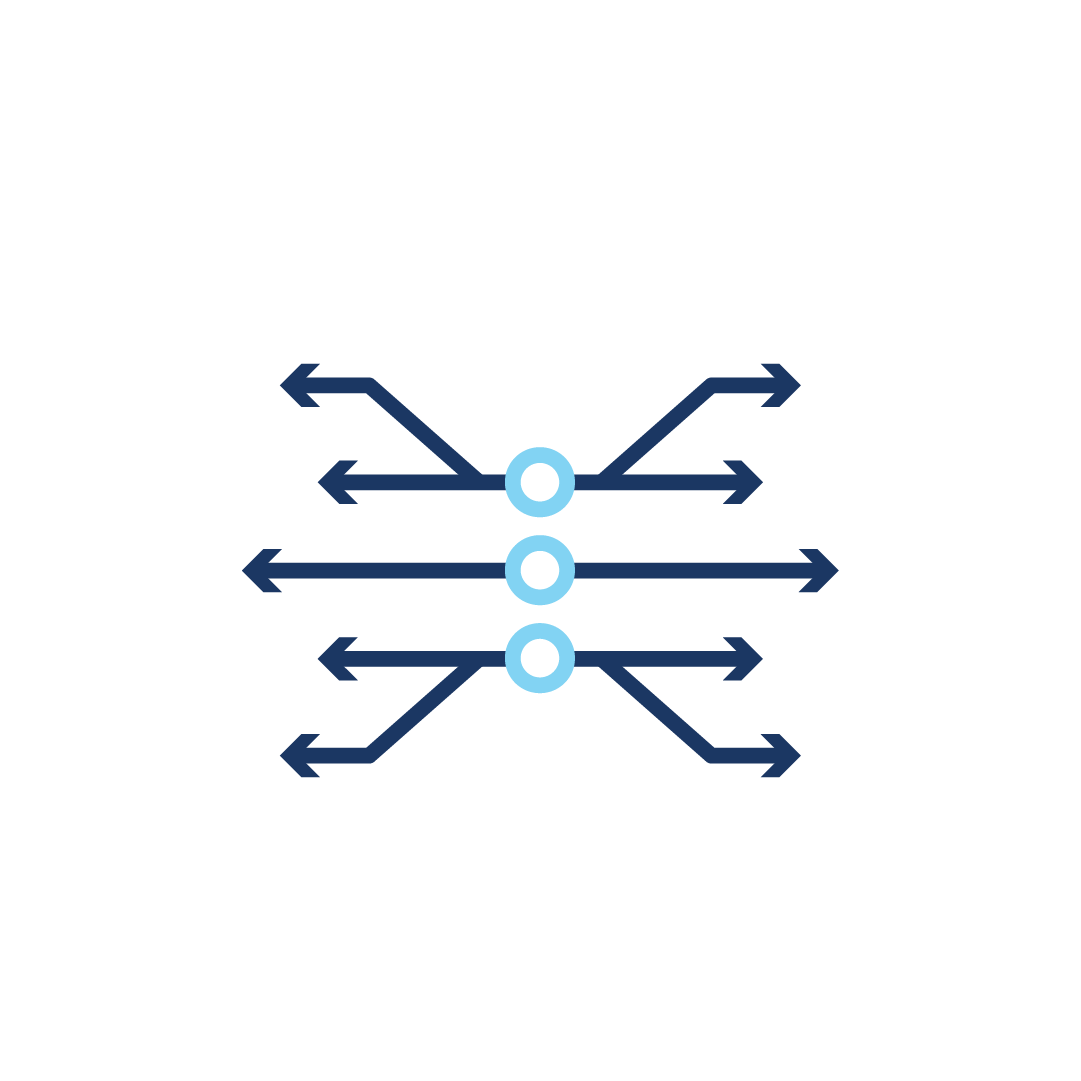
Automated interfaces for direct loading and unloading at the production line
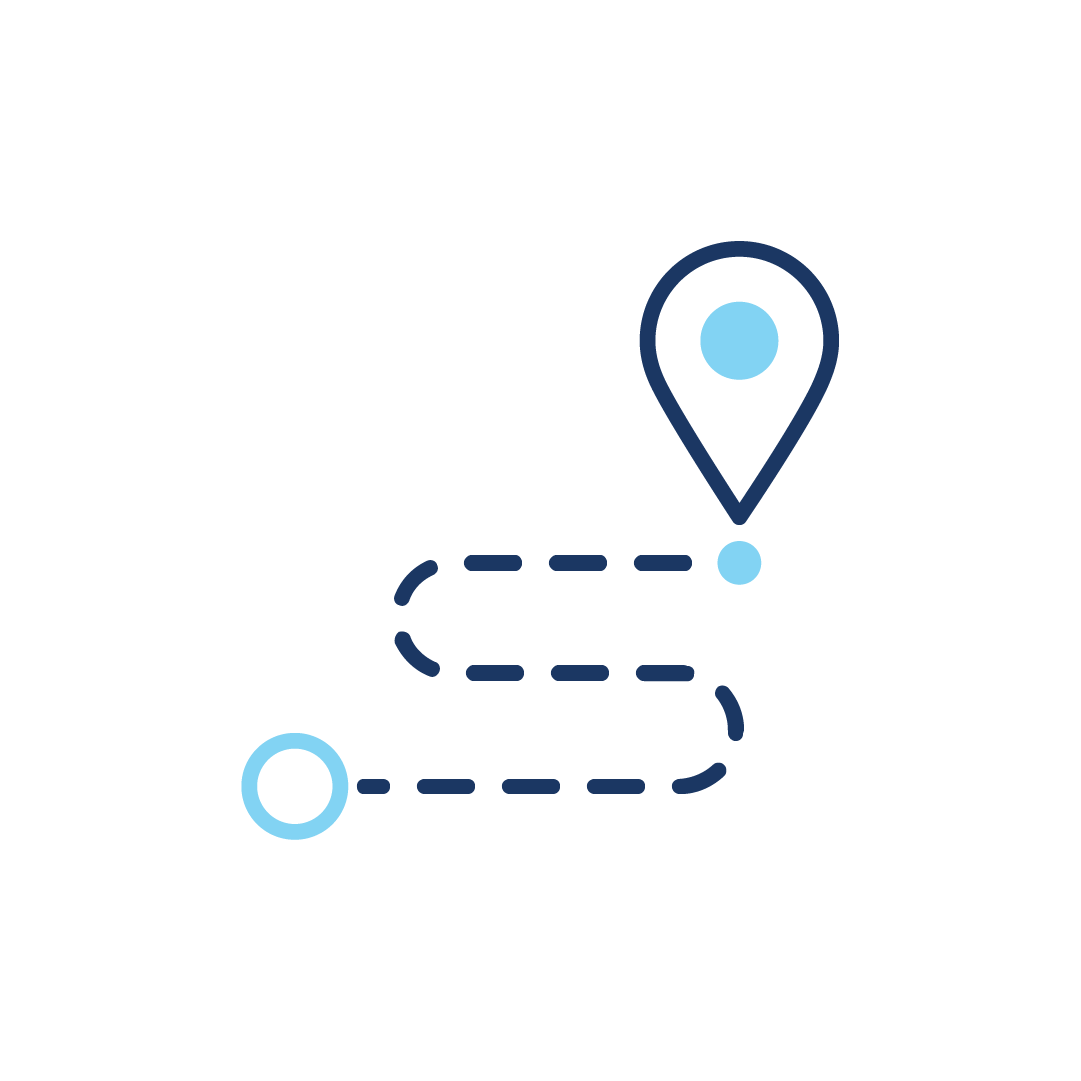
Real-time transparency through integrated tracking and tracing
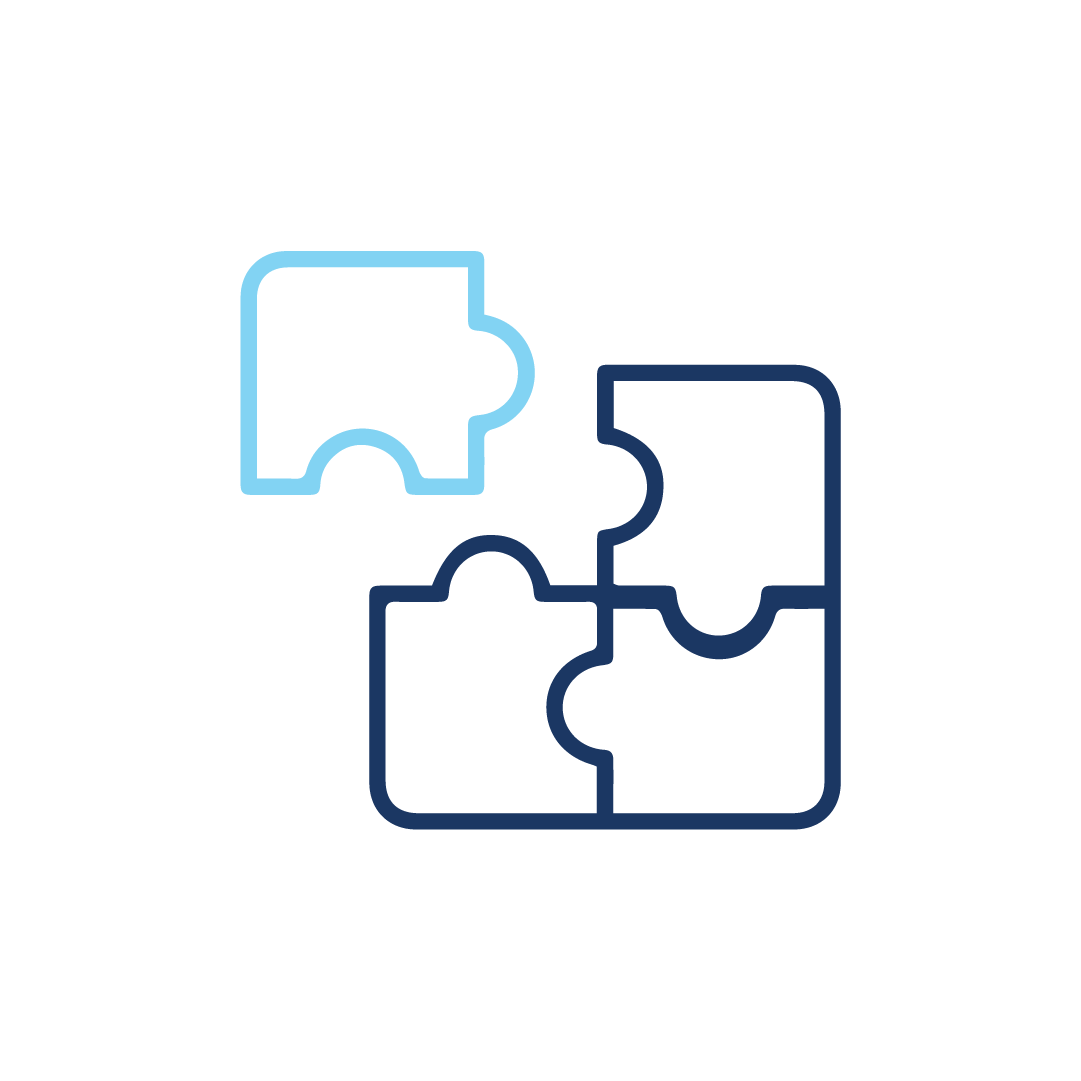
Seamless integration into existing processes, systems, and factory layouts
SMART WAREHOUSE / BIG
Automated Storage System for High Material Volumes
As production volumes increase and supply chains become more complex, warehouse systems must scale accordingly.
The Smart Warehouse / Big is designed for manufacturing environments with high material throughput. It enables structured storage of large volumes and ensures continuous supply to production areas.
The system is based on a scalable racking infrastructure with fully automated loading and retrieval. If required, the material flow can be extended with autonomous transport systems. This reduces buffer zones, stabilizes processes, and shortens internal transport times.
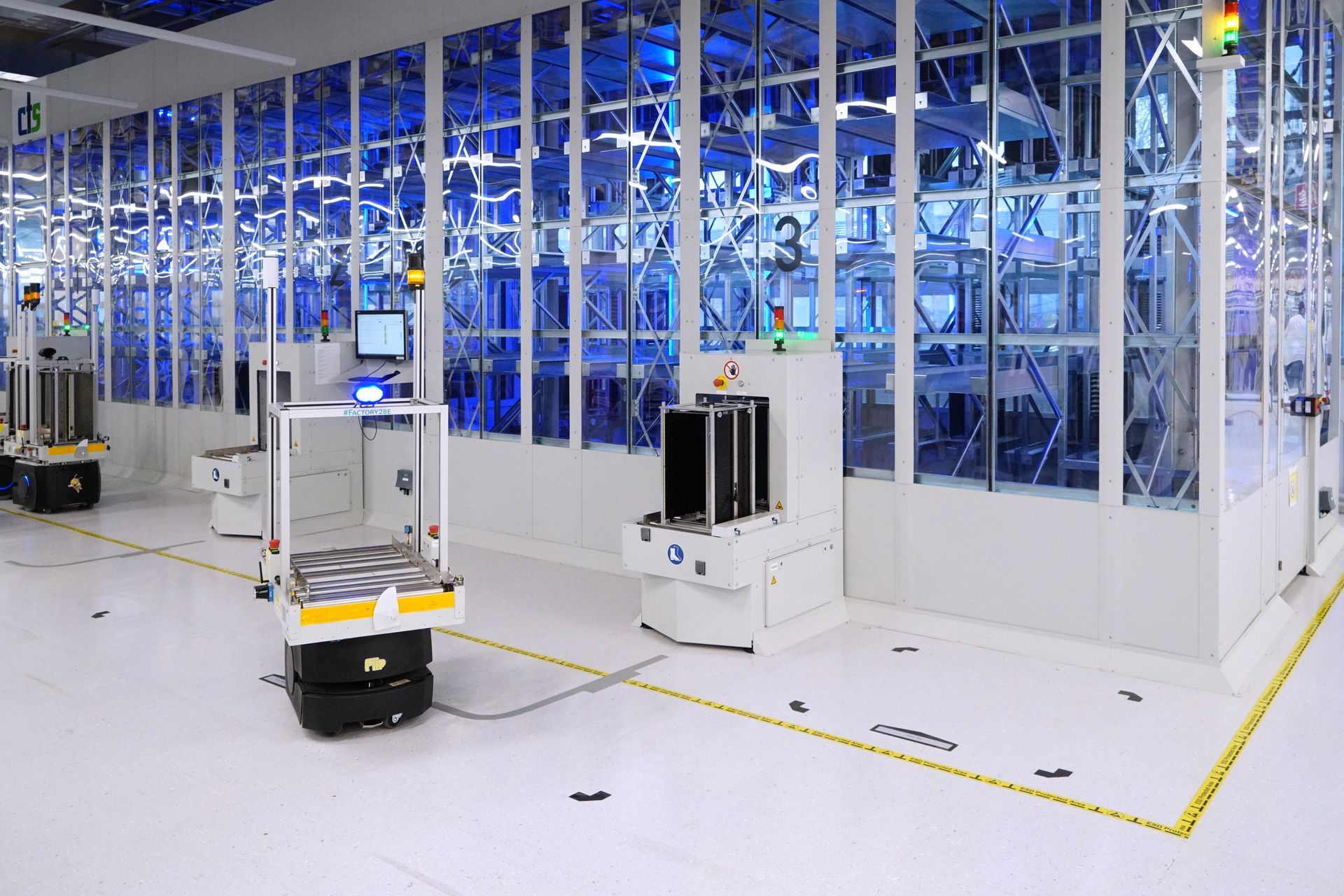
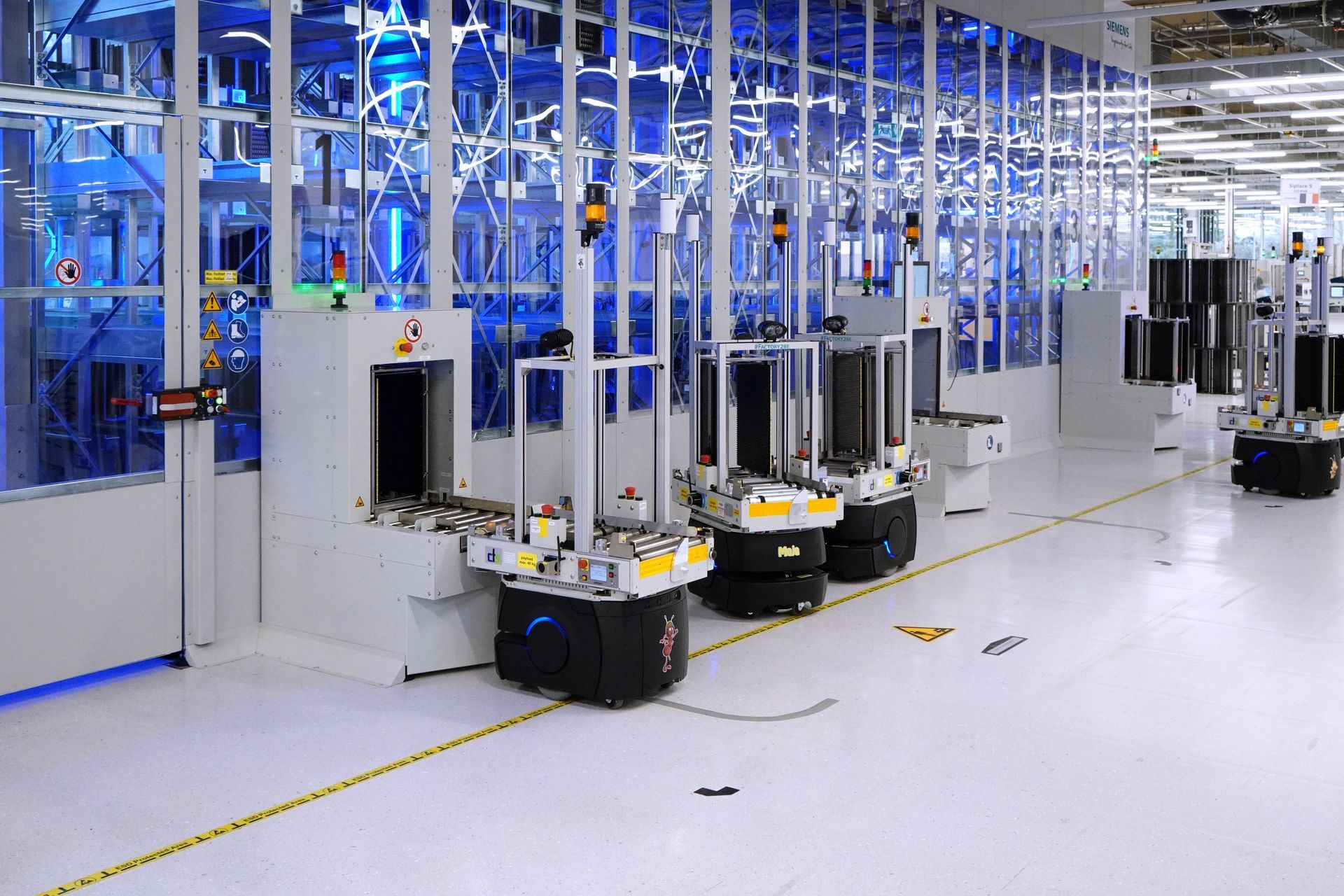
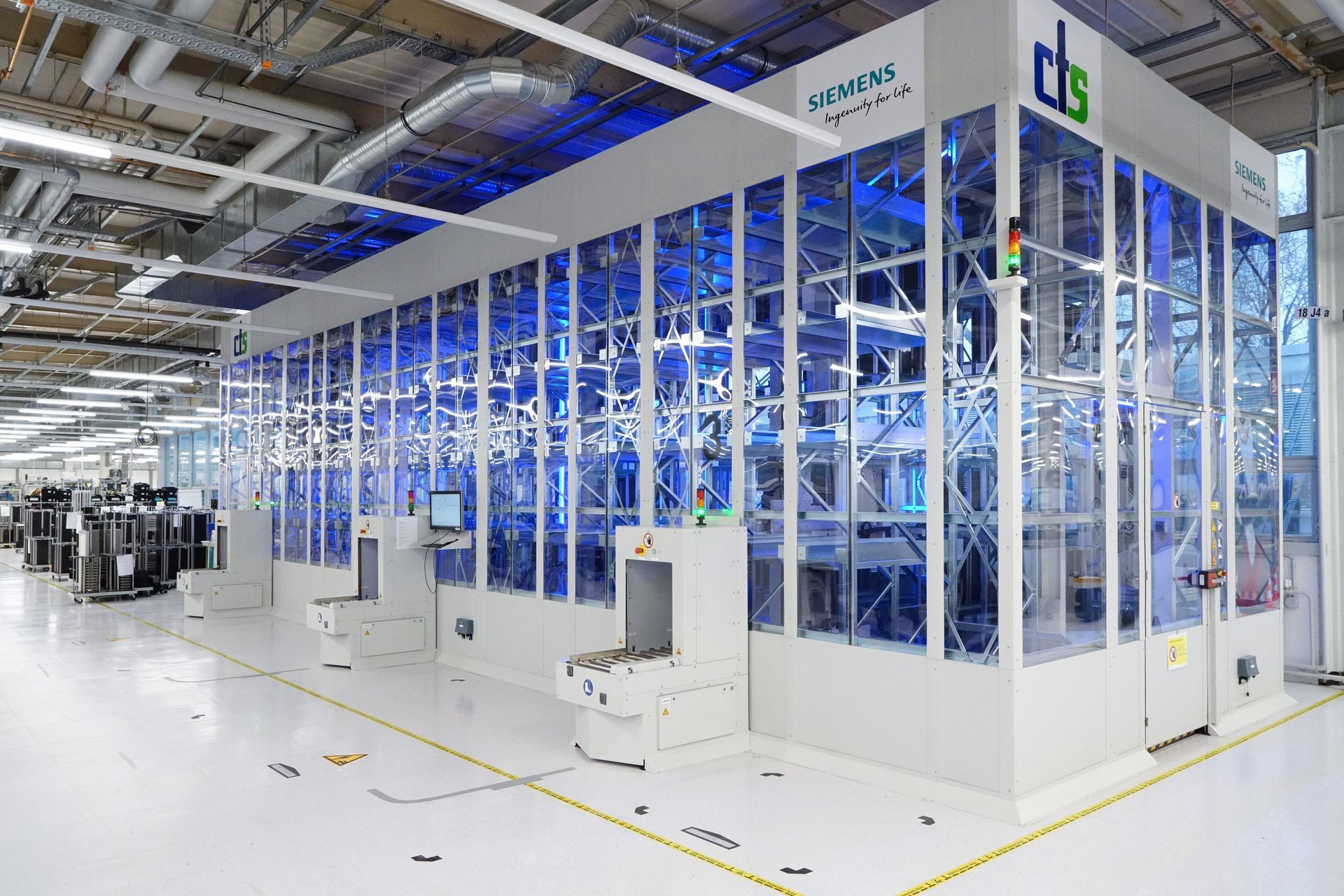
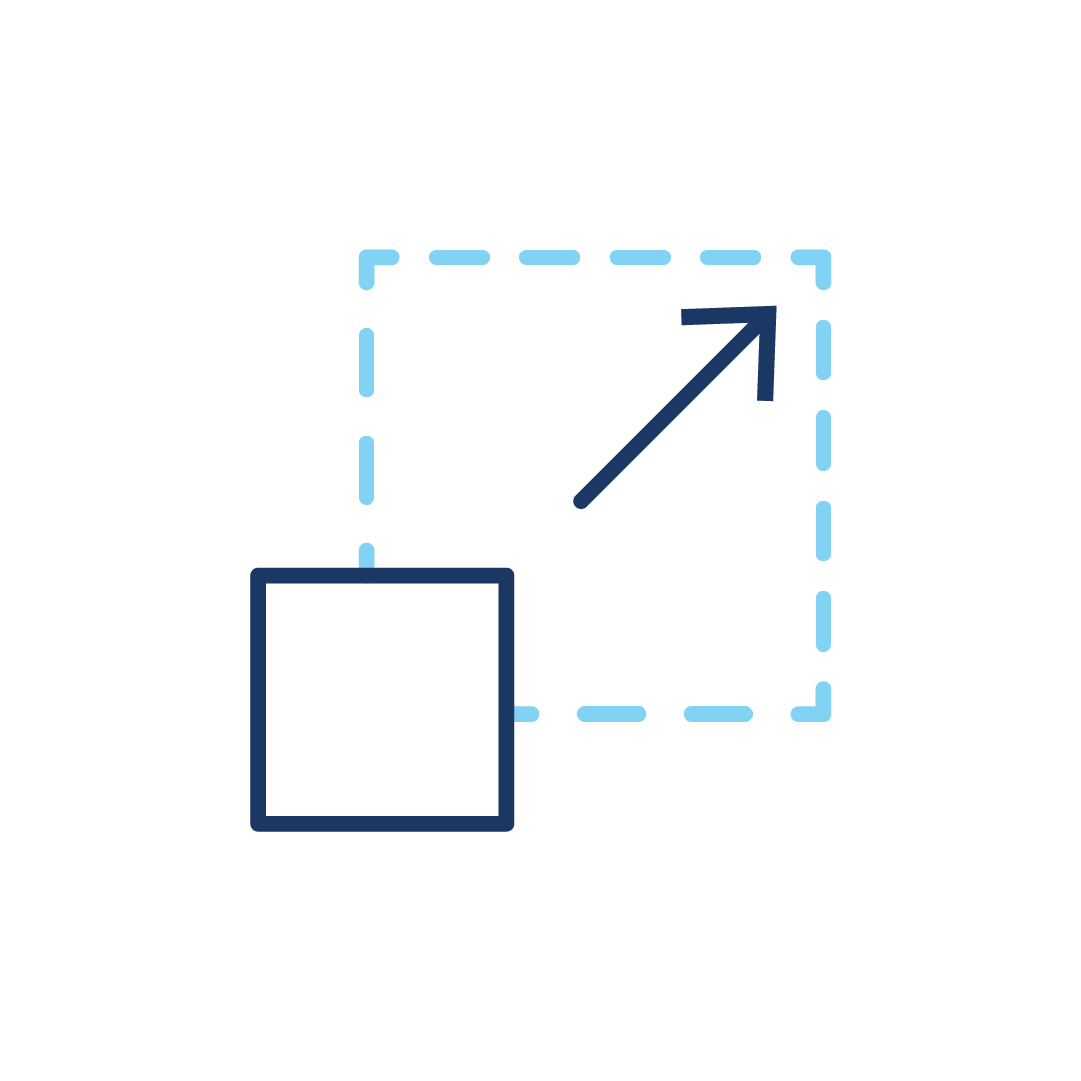
Scalable storage capacity from 400 to over 2,000 locations
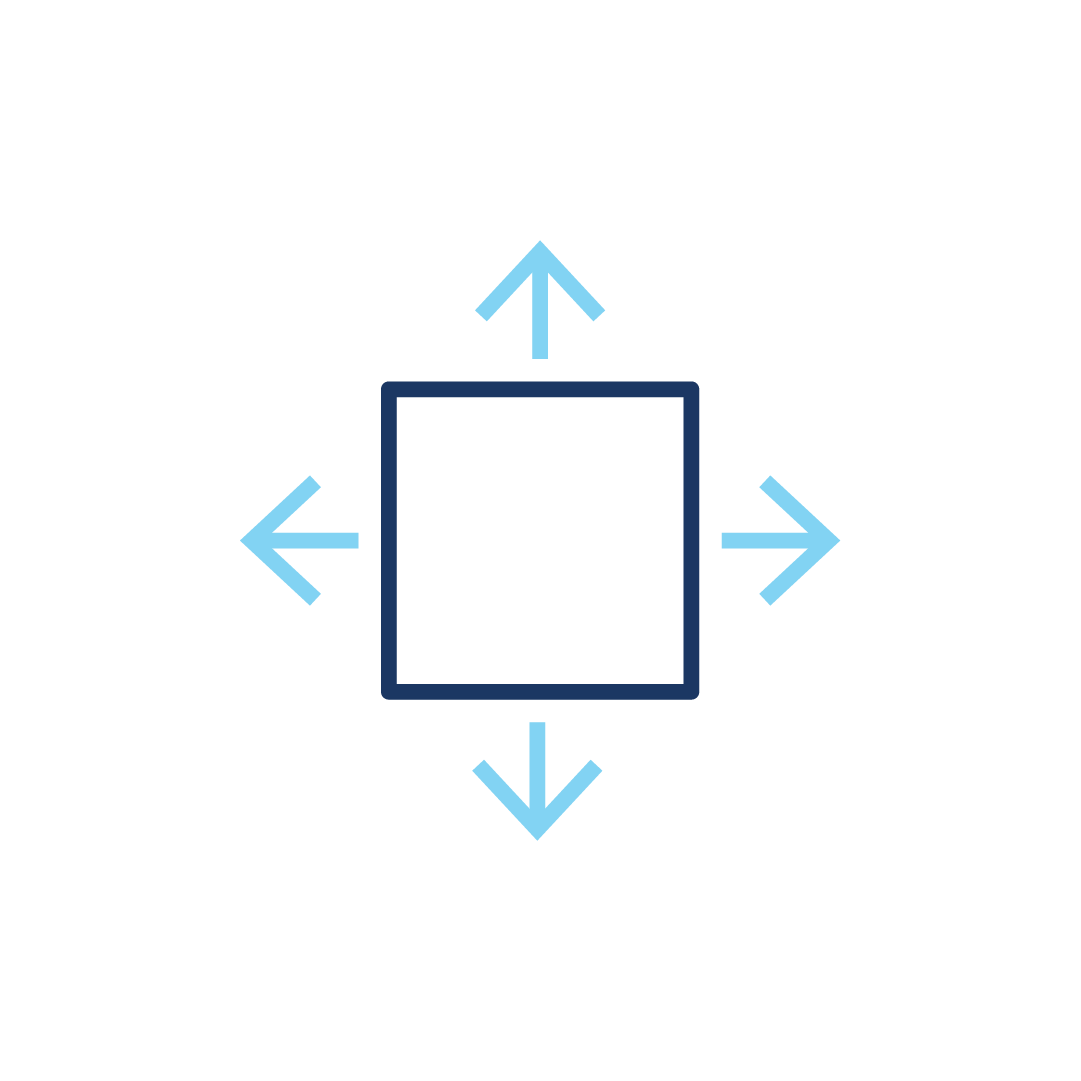
Min: 8,5m x 4,5m x 4,5m
Max: 20m x 4,5 m x 8m
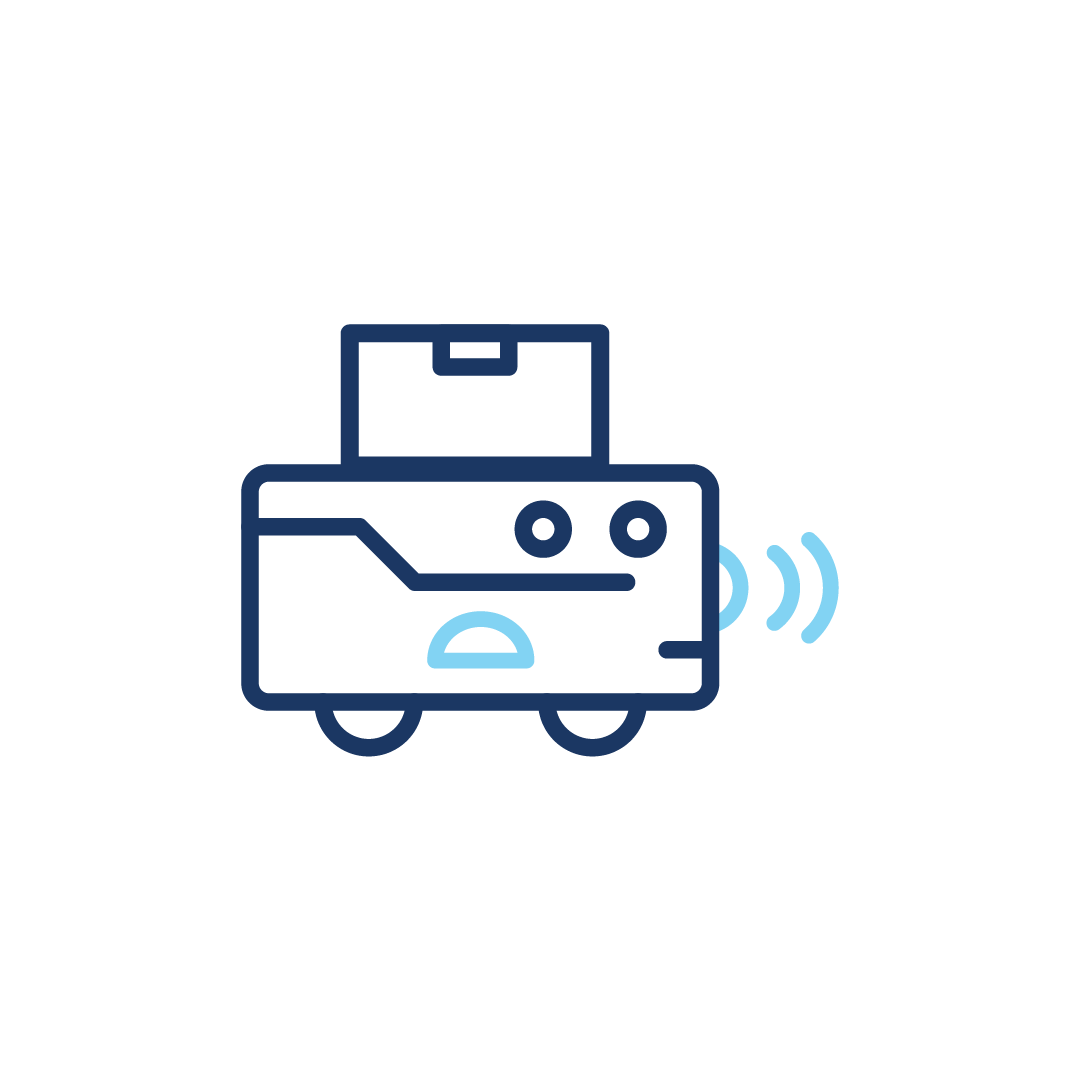
Automated material transport with efficient AMR integration
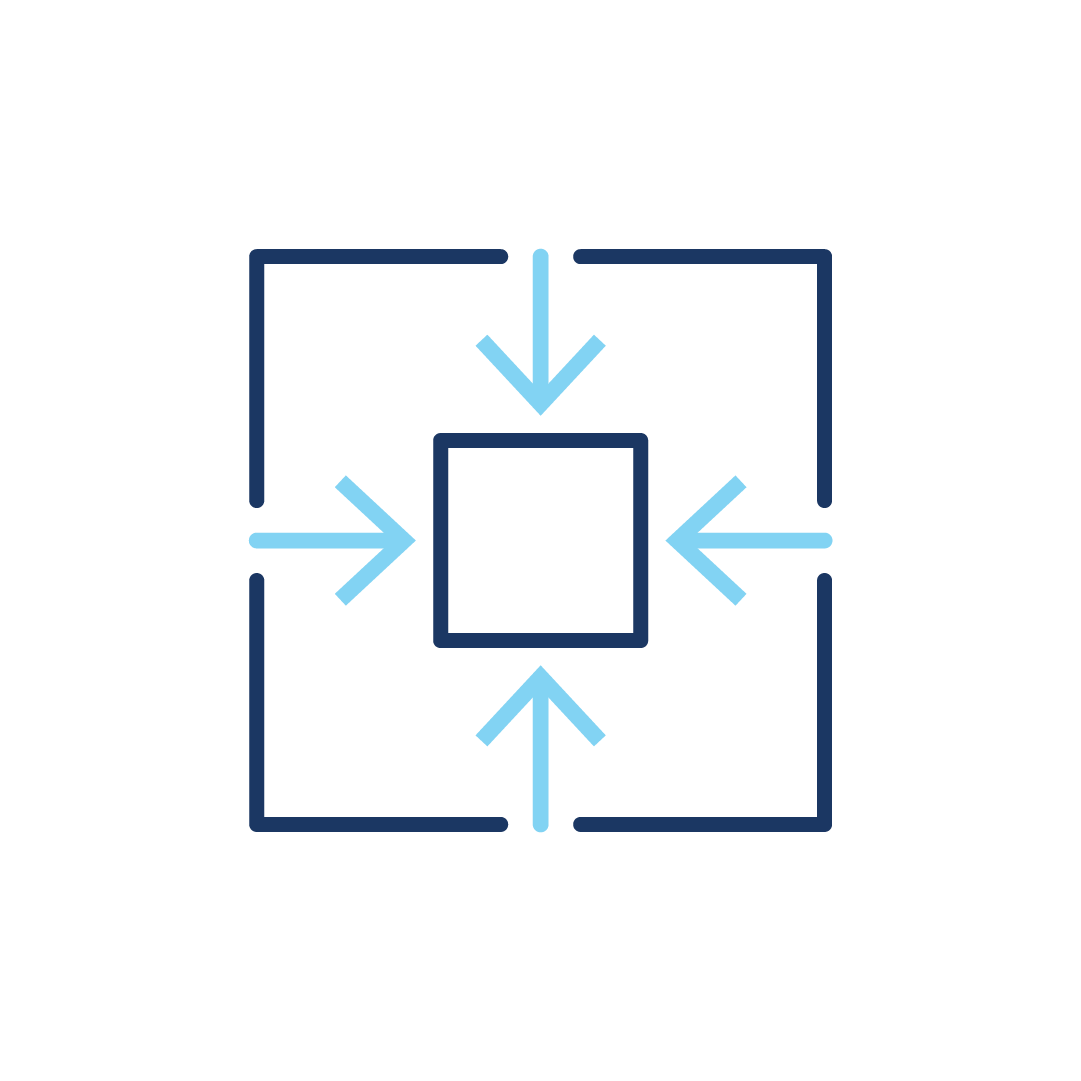
Compact design enabled by high-density racking and advanced gripper technology
SMART WAREHOUSE / SMT REELS
Optimized Reel Storage for SMT Production
"Designed for manufacturing" – this principle drives the efficiency of modern SMT lines. But what about the storage systems that directly impact that efficiency?
The Smart Warehouse / SMT Reels is specifically developed for the requirements of electronics manufacturing. It enables structured storage and automated provisioning of SMT component reels – with the goal of reducing setup times, stabilizing workflows, and ensuring reliable material availability.
With integrated tracking and direct connection to existing SMT lines, the system seamlessly integrates into the Smart Electronics Factory.
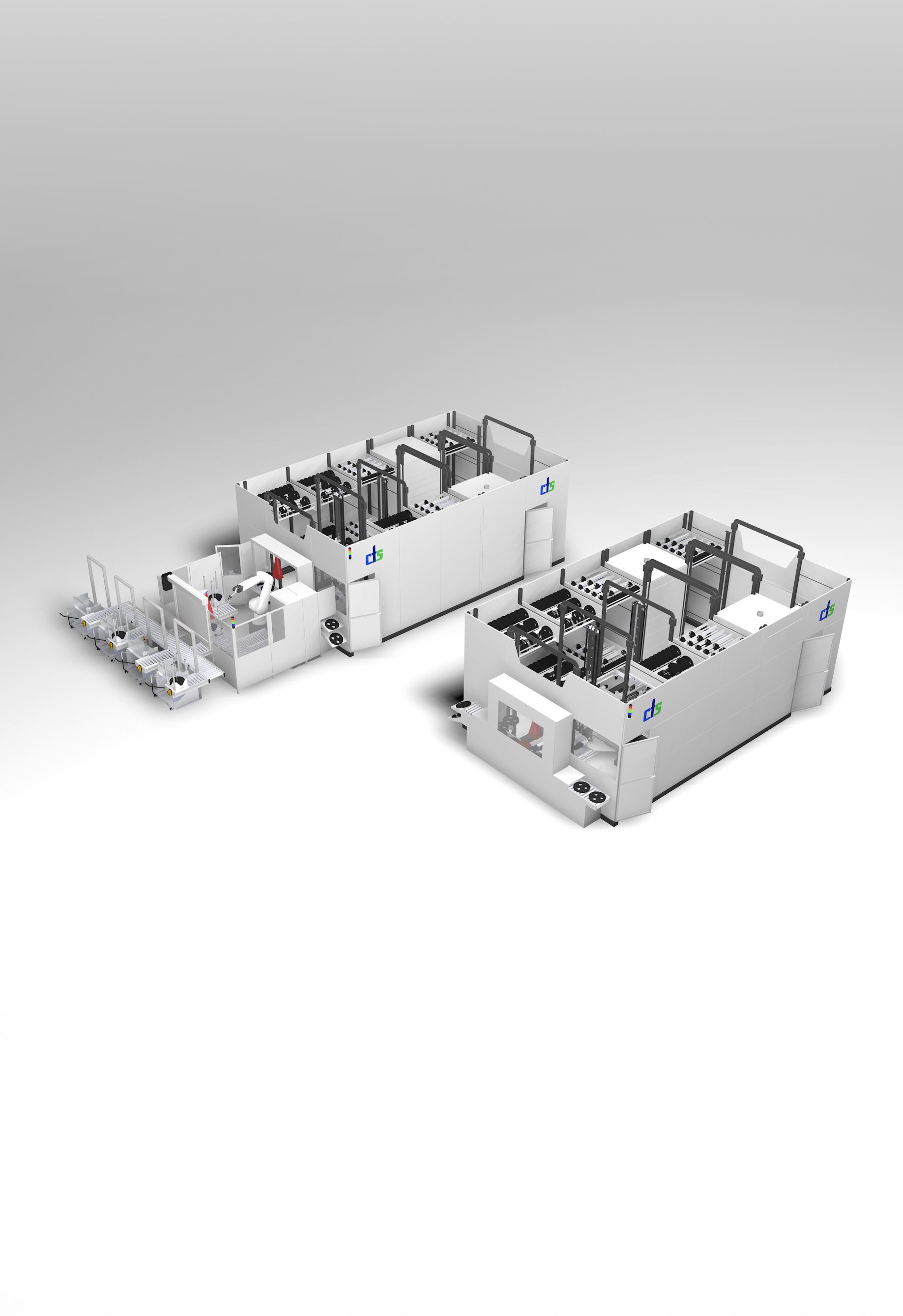
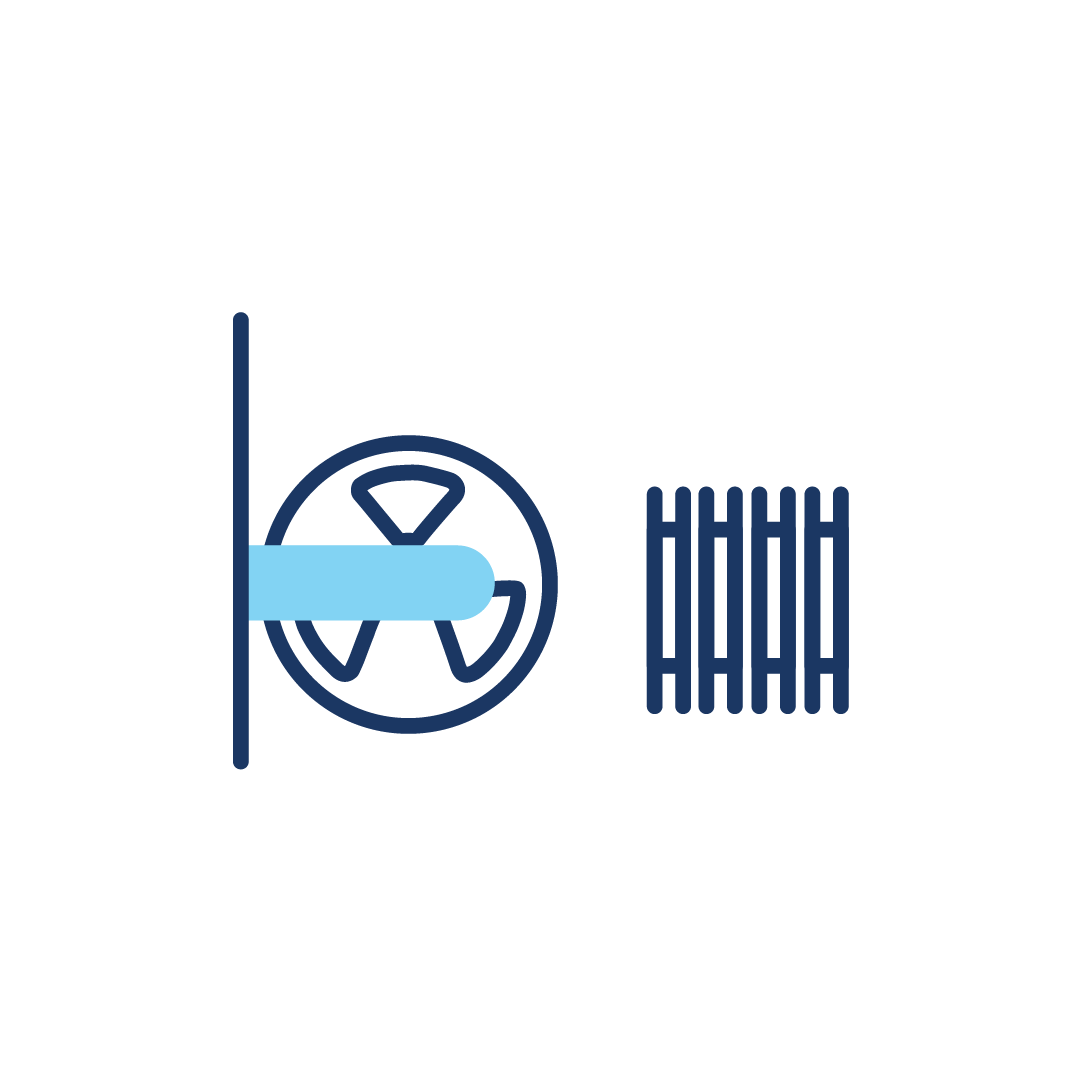
Maximum reel density with minimal footprint
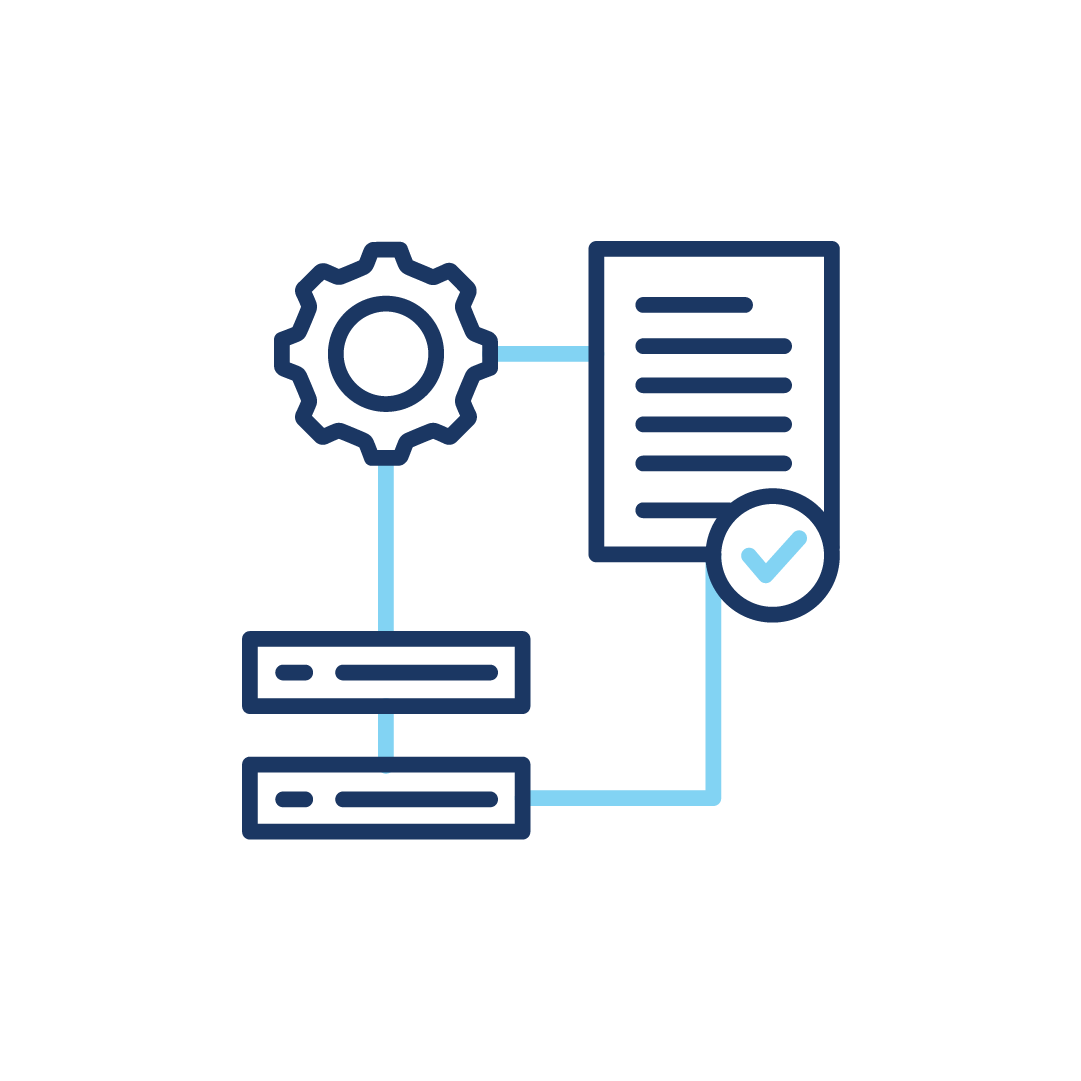
Controlled storage zones for MSD-sensitive components
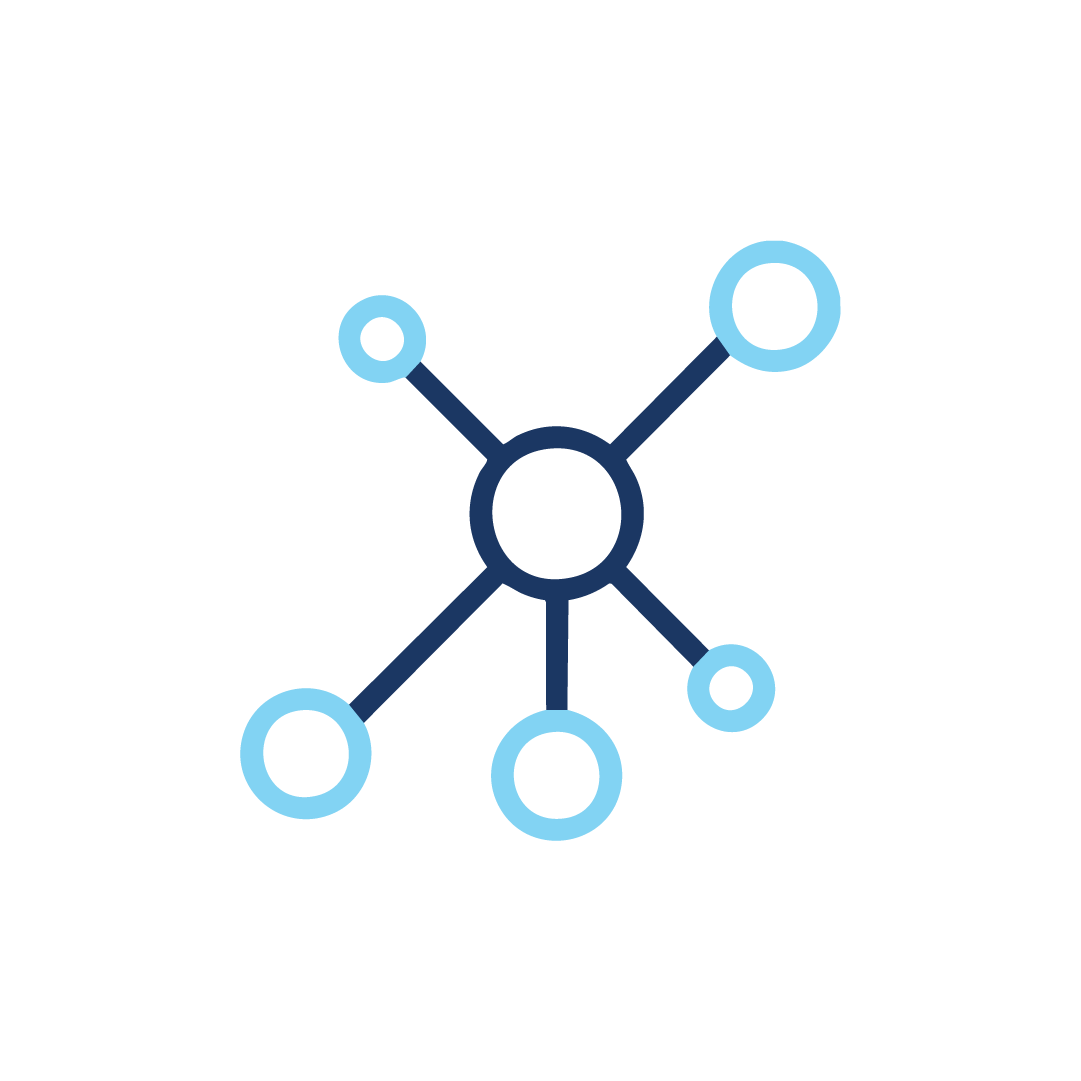
Central hub for material and logistics coordination
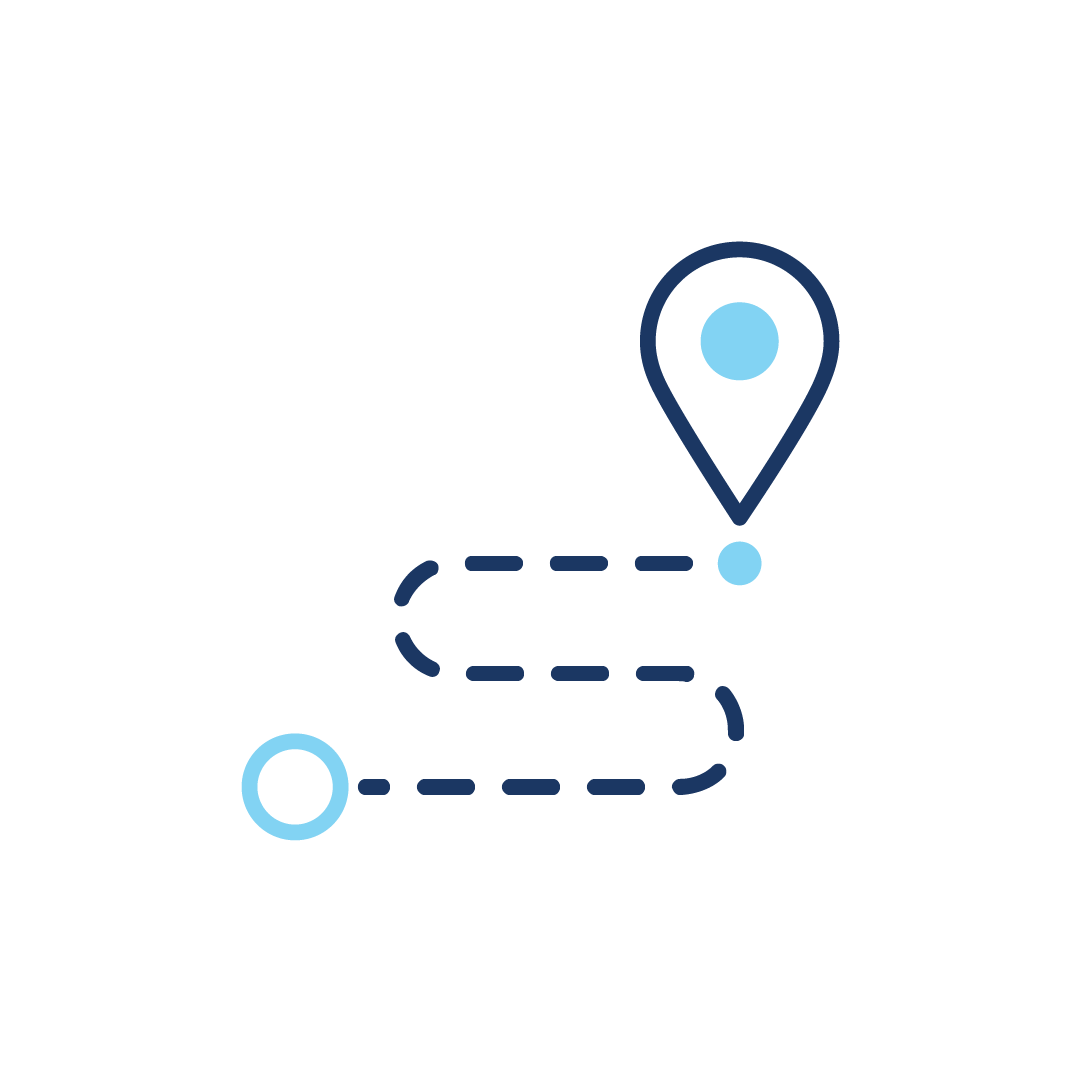
Seamless tracking and tracing of material flows
TRANSFER & BUFFER STATIONS
Temporary Buffering for Flexible Production Processes
Buffer stations are a key element in production logistics when it comes to compensating for cycle time deviations, supply bottlenecks, or fluctuating demand.
CTS offers modular transfer and buffer solutions that act as temporary storage between warehouse, production line, and transport systems – helping to stabilize internal material flows.
With automated loading and unloading interfaces, these stations can be directly connected to AMR systems or manual transport units – without the need for additional handover processes.
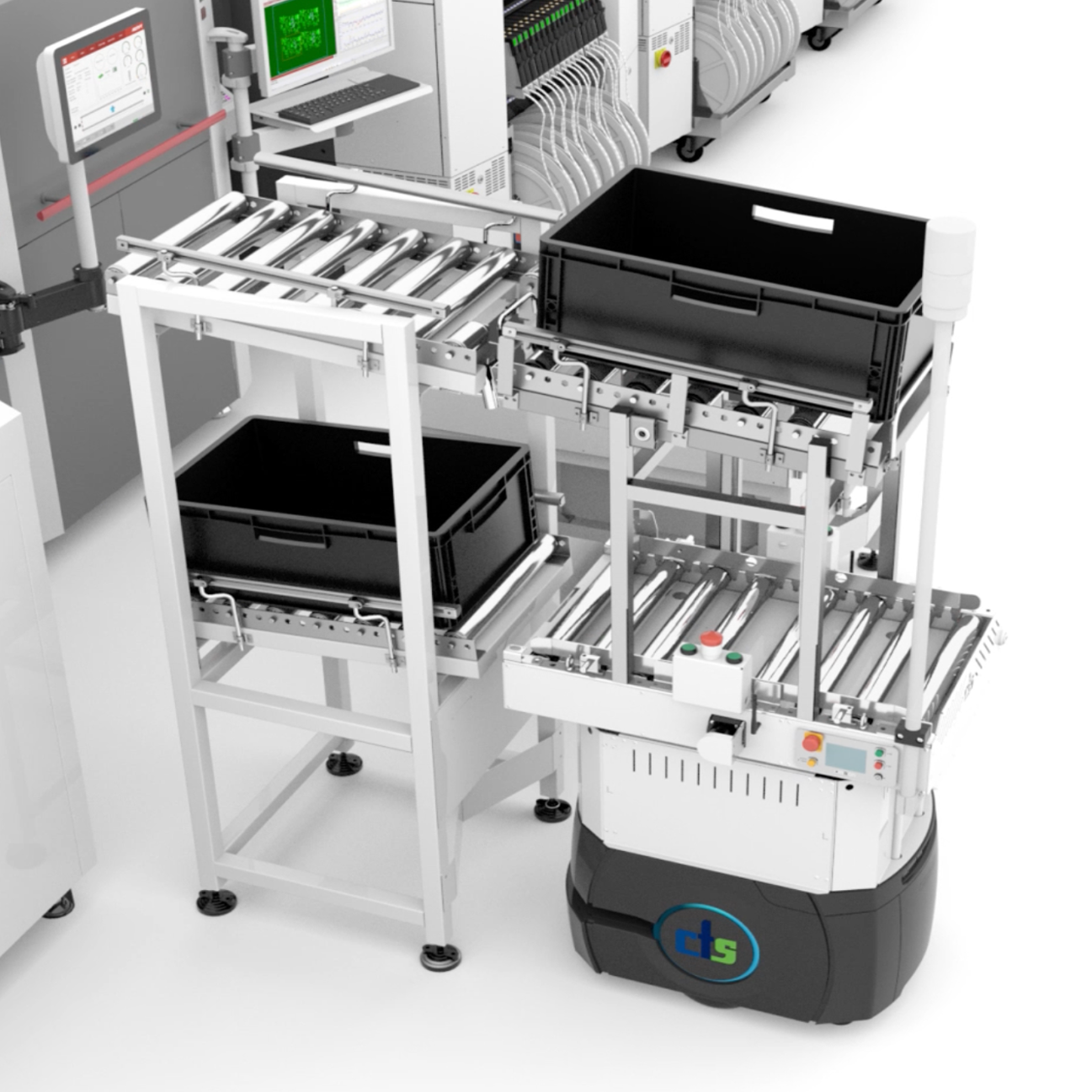
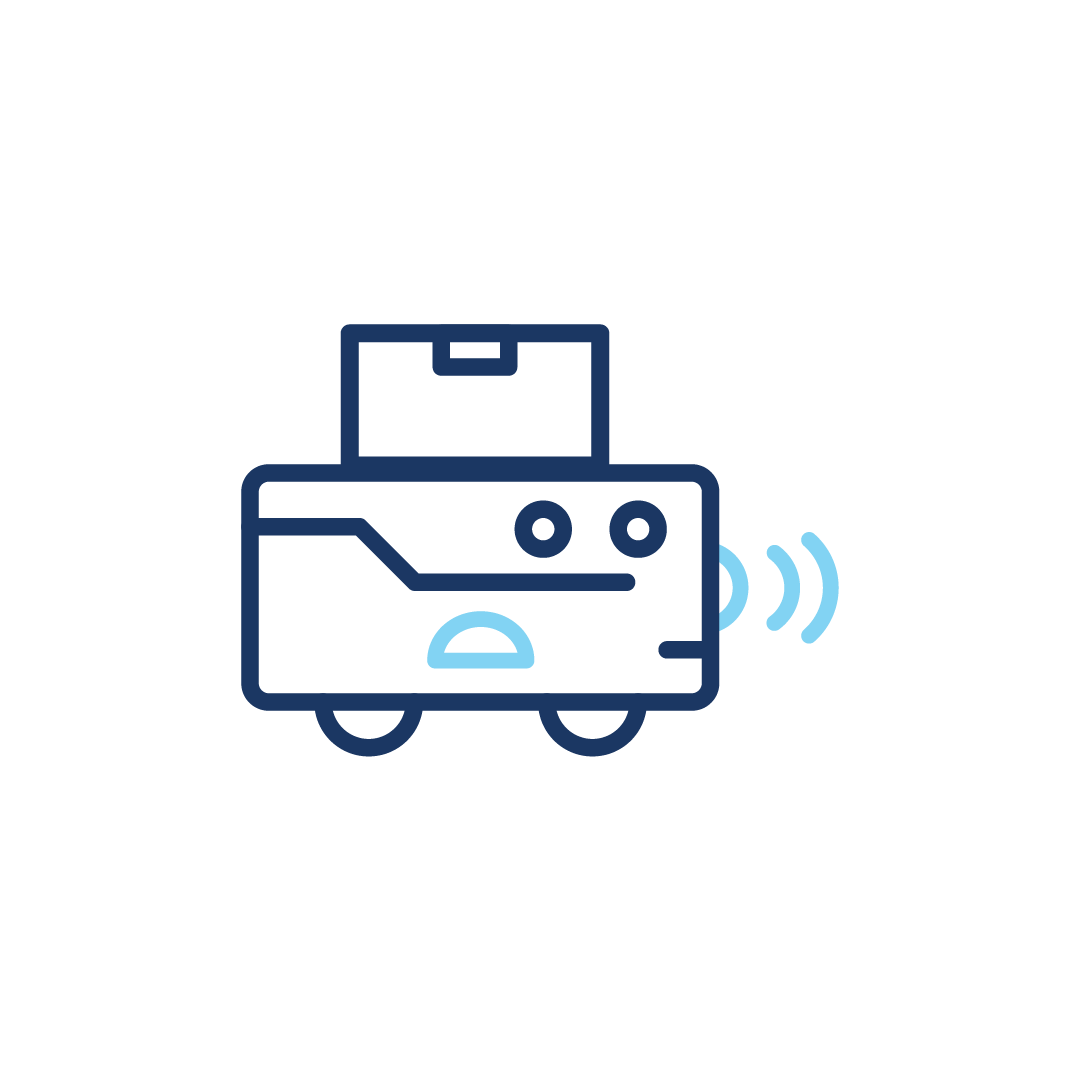
Direct AMR and conveyor integration via automated interfaces
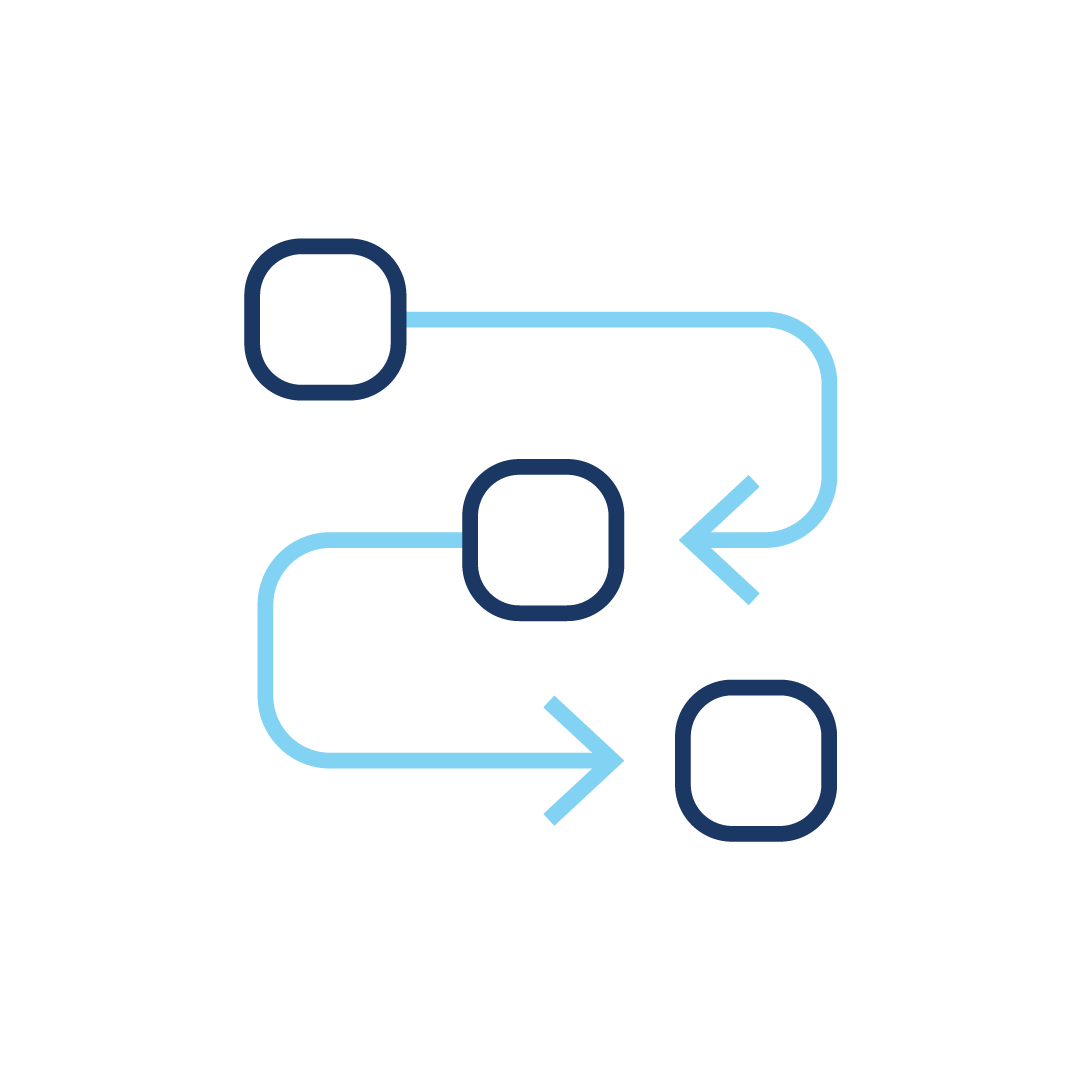
Flexible configuration as line buffer, circulation buffer, or transfer point
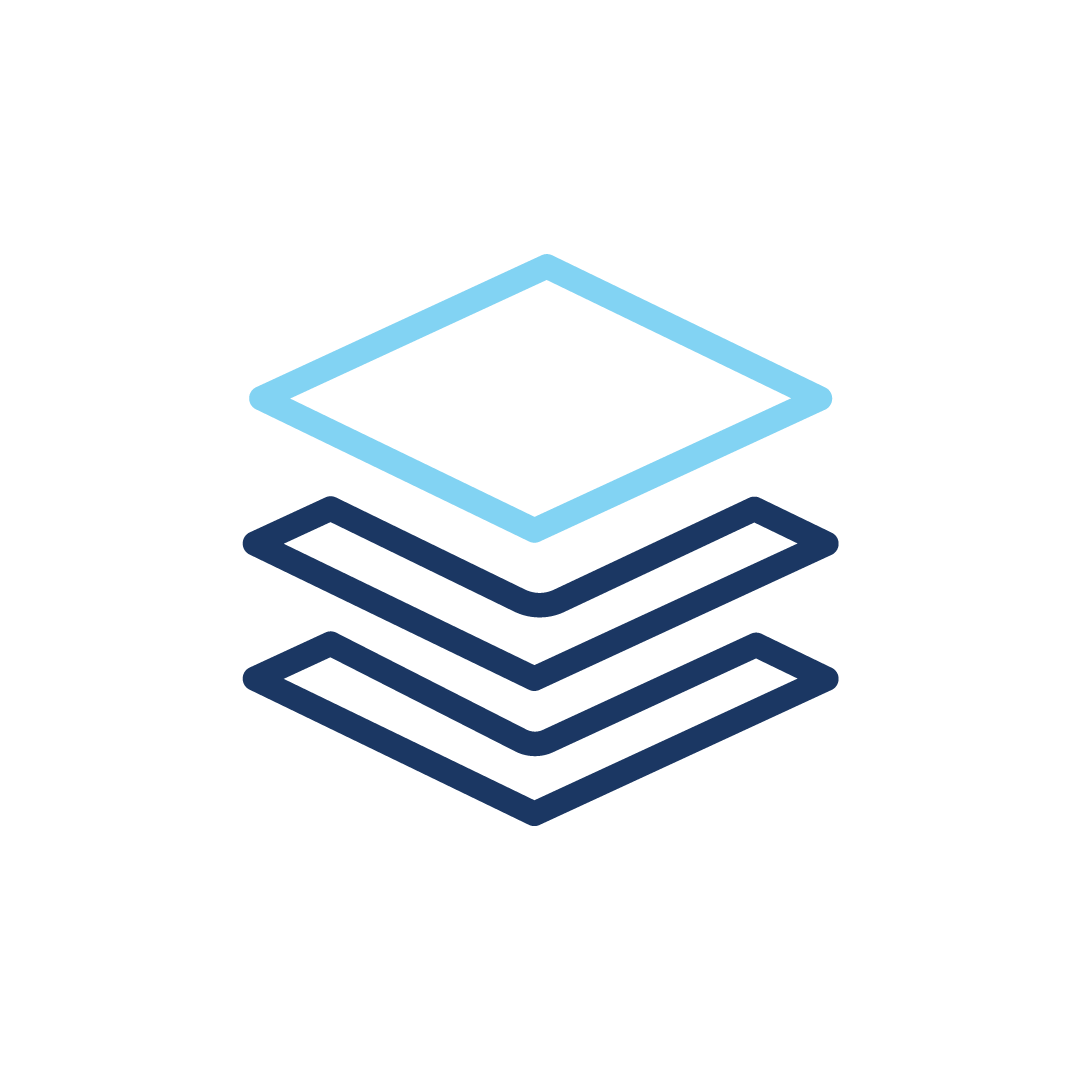
Decoupling of production areas in case of asynchronous takt times
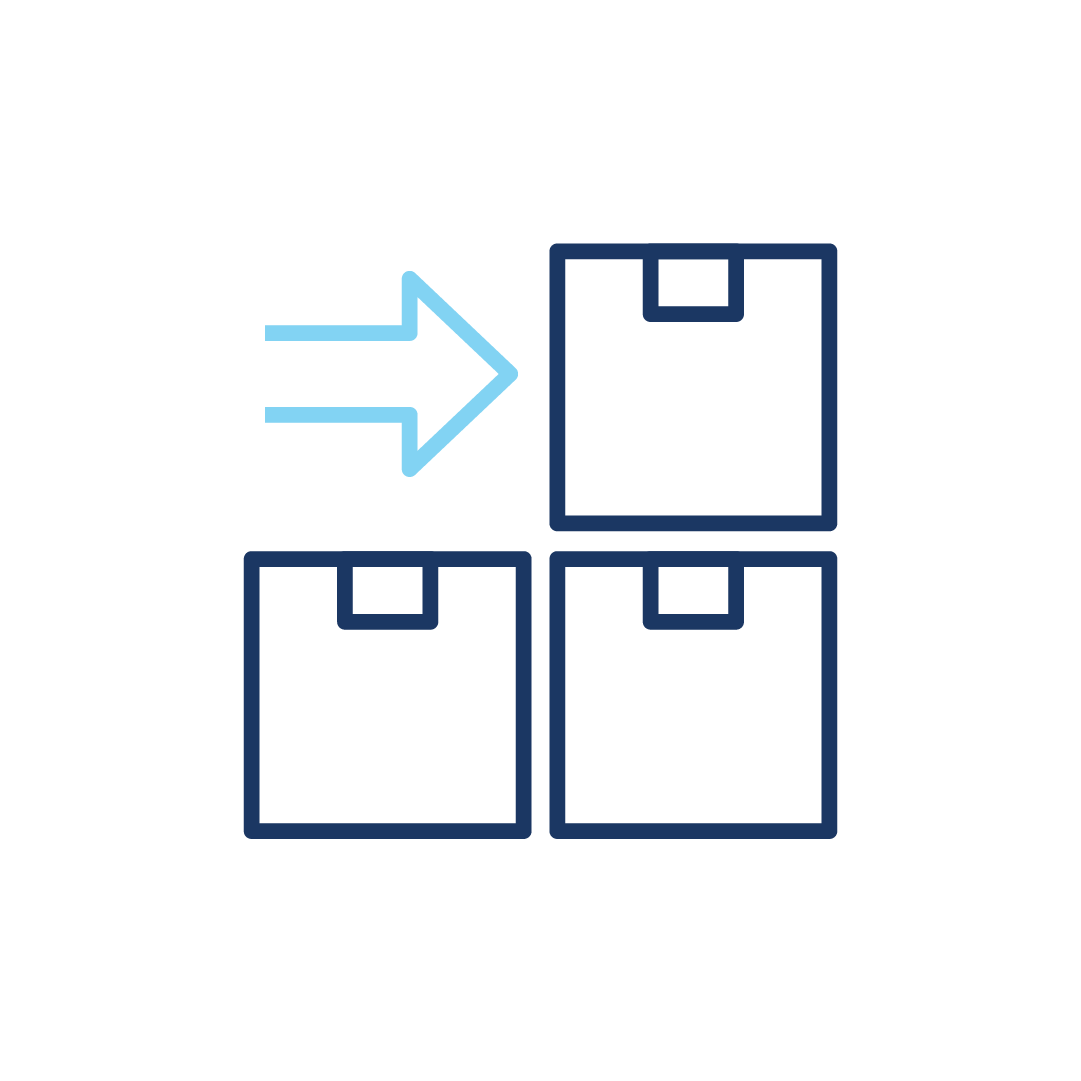
Dynamic buffering for parts, containers, or carriers
AUTONOUS MOBILE ROBOTS
Transport Solutions for Flexible, Decoupled Production Environments
Autonomous Mobile Robots (AMRs) handle repetitive transport tasks within production – reliably, flexibly, and without manual intervention.
They connect warehouses, buffers, and handover stations directly to the consumption points along the line, ensuring a continuous and synchronized material supply.
AMRs navigate freely in dynamic environments, adapt their routes in real time, and remain operational even as layouts change. By integrating AMRs, internal transport processes become standardized – relieving personnel from non-value-adding tasks.
CTS implements AMR solutions in collaboration with partners such as Omron, Agilox and MiR – vendor-neutral and tailored to your infrastructure. Existing systems can be integrated via modular interfaces.

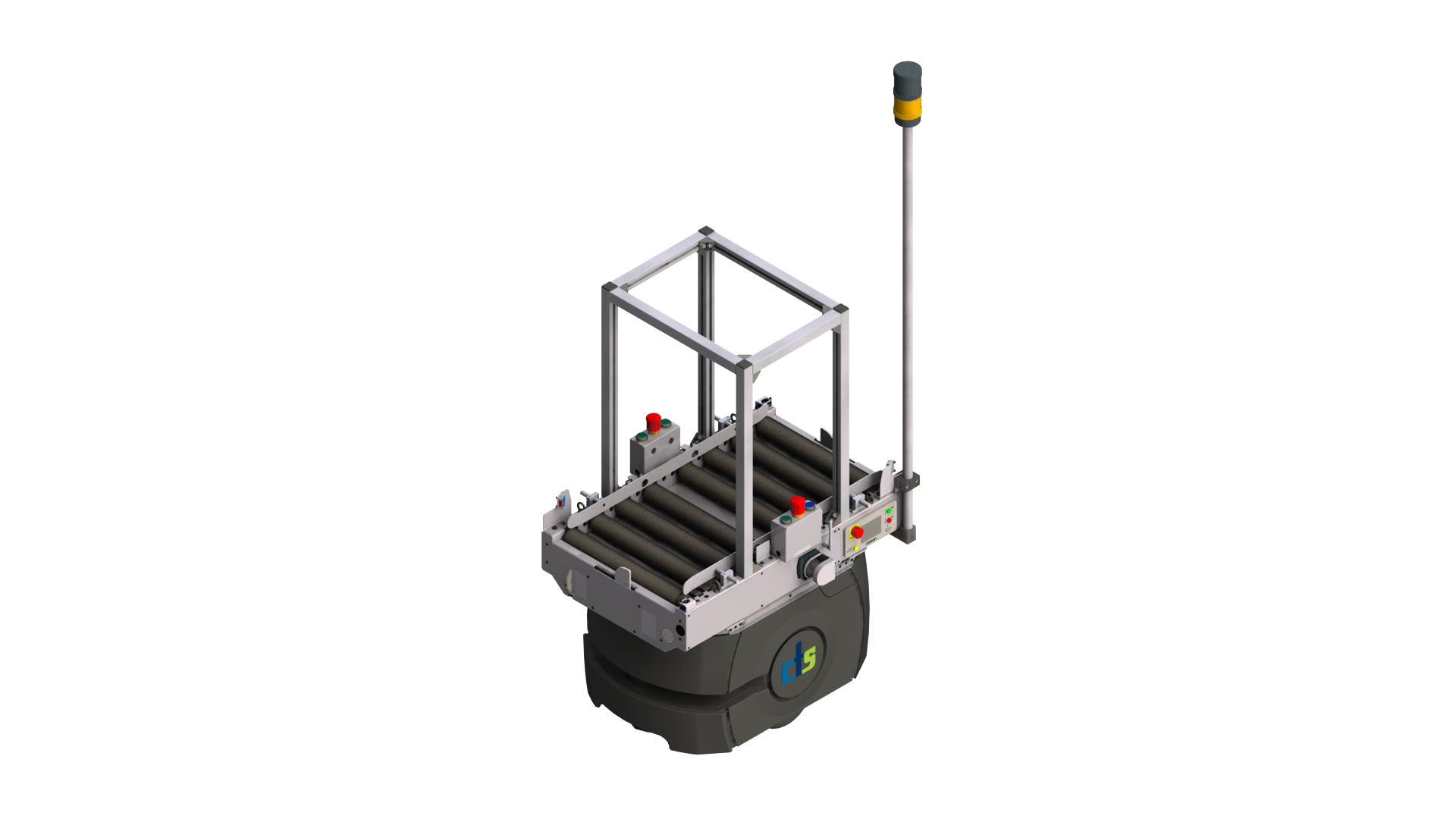
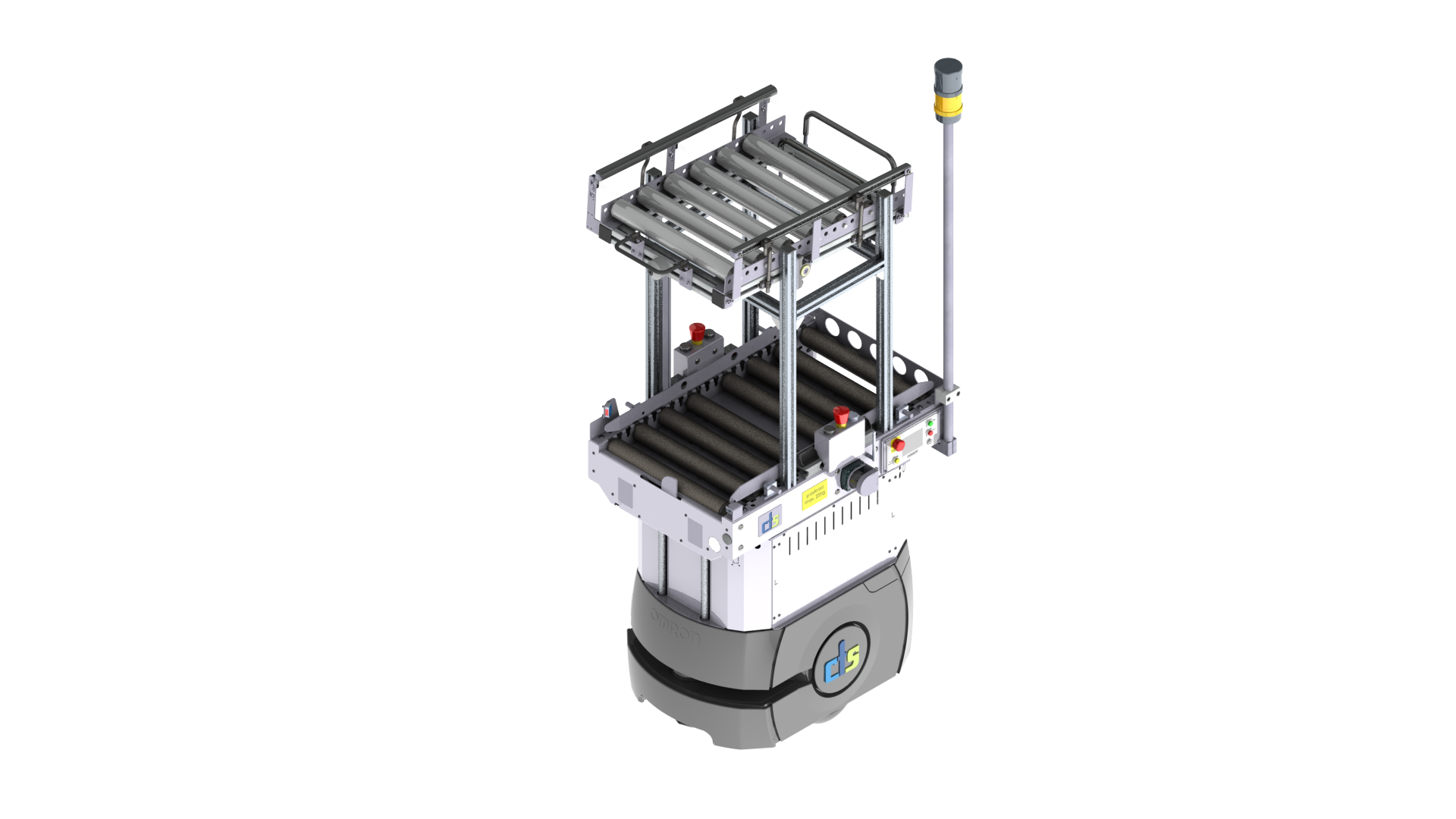
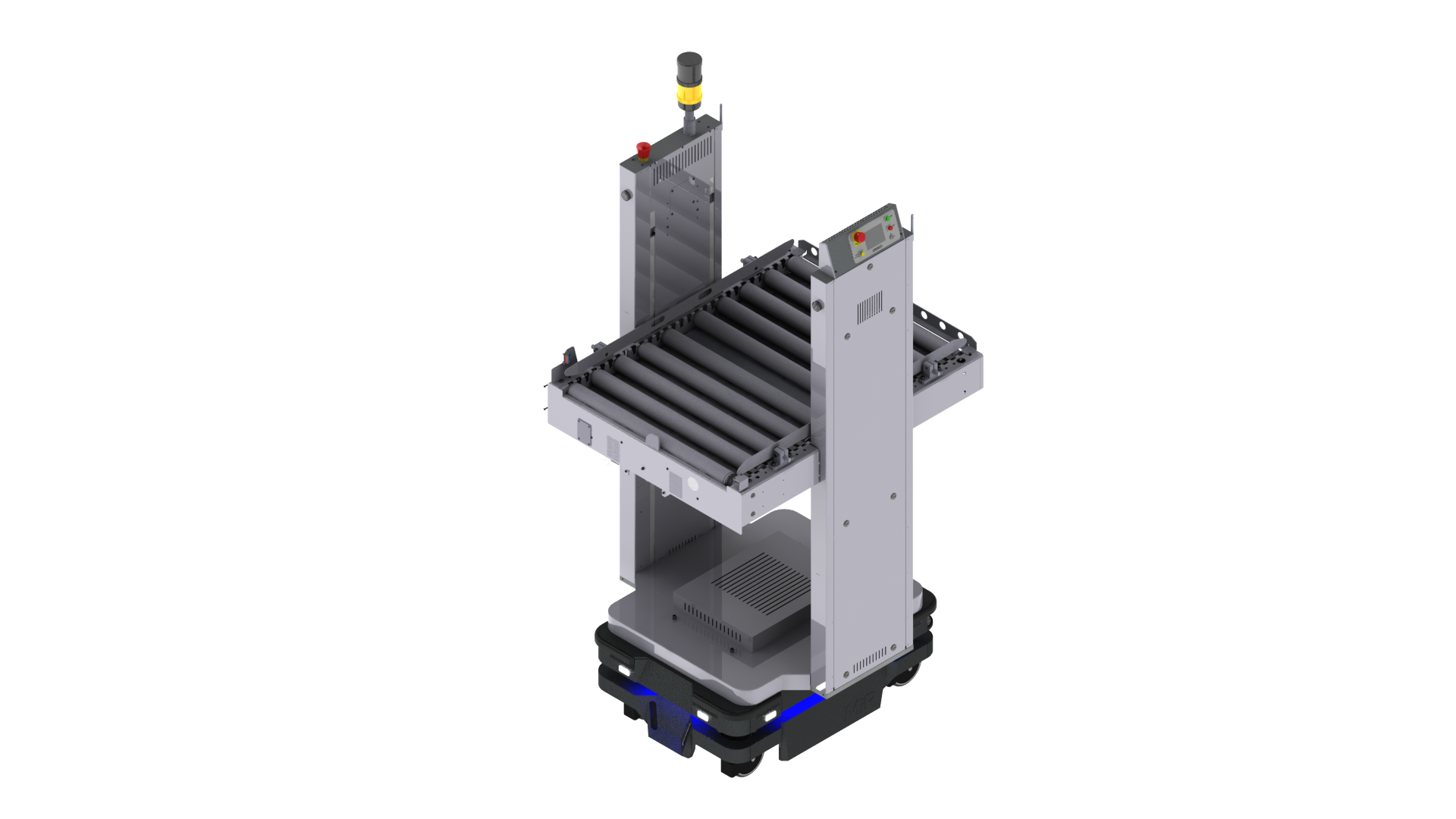
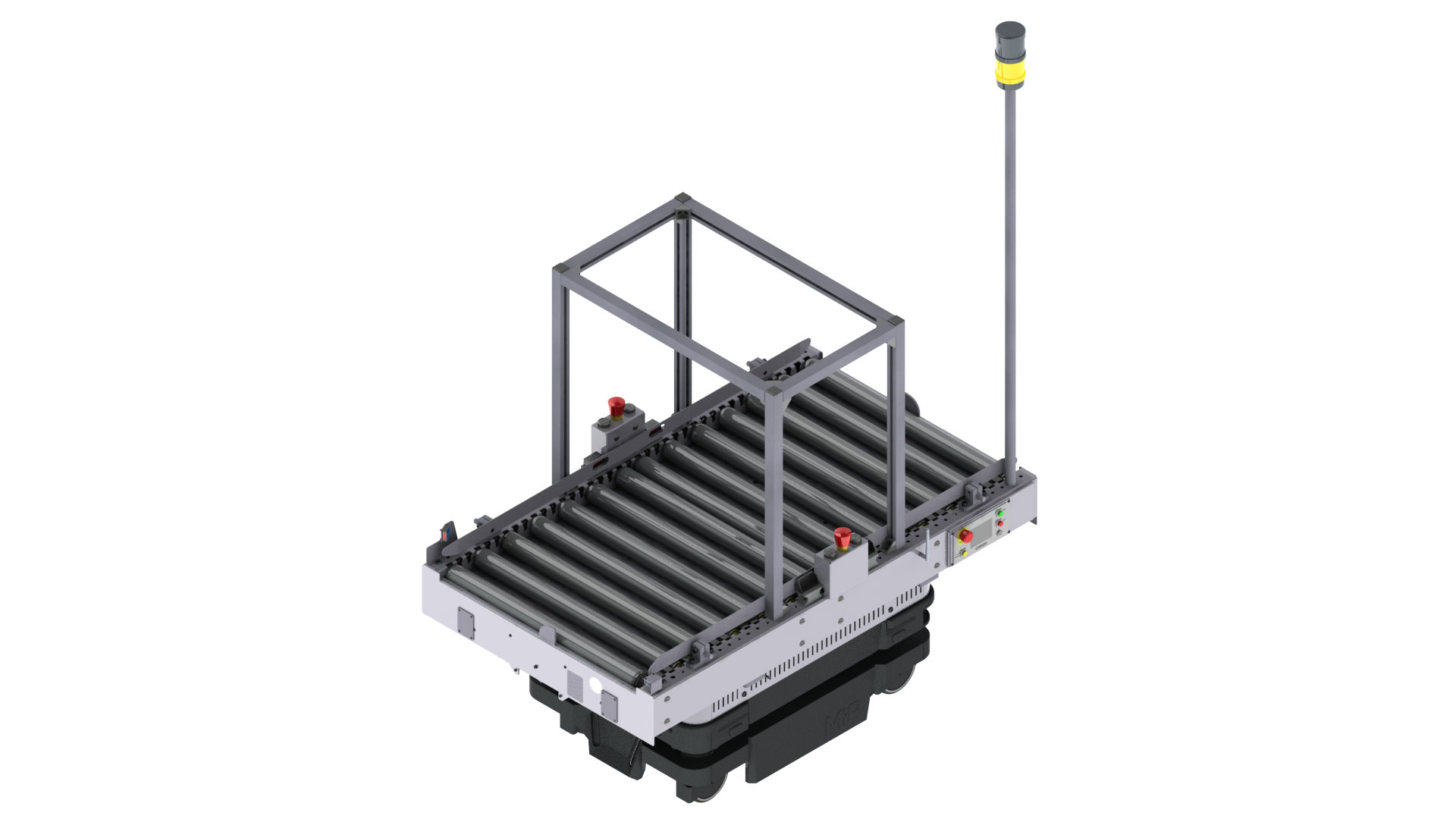
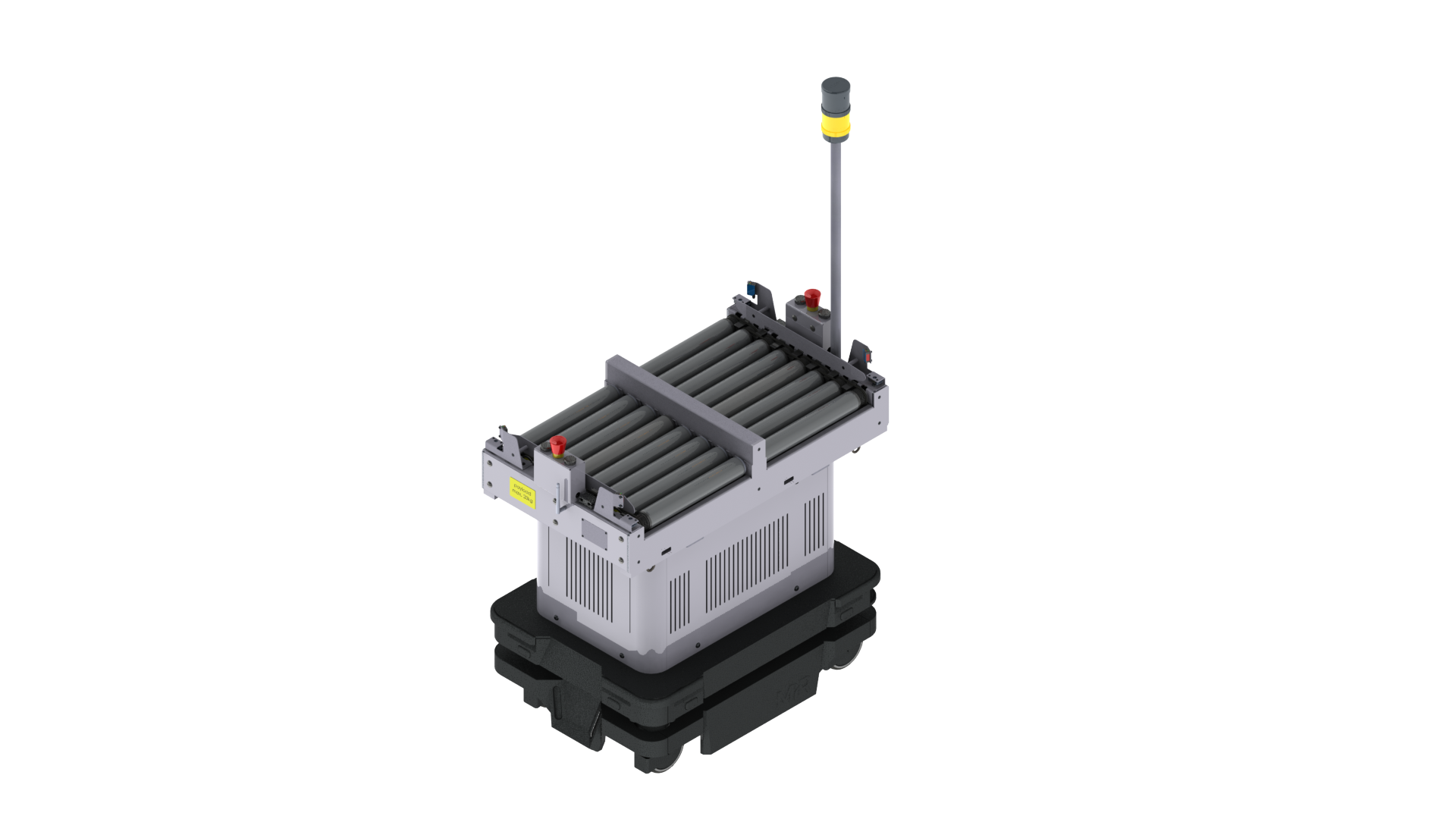
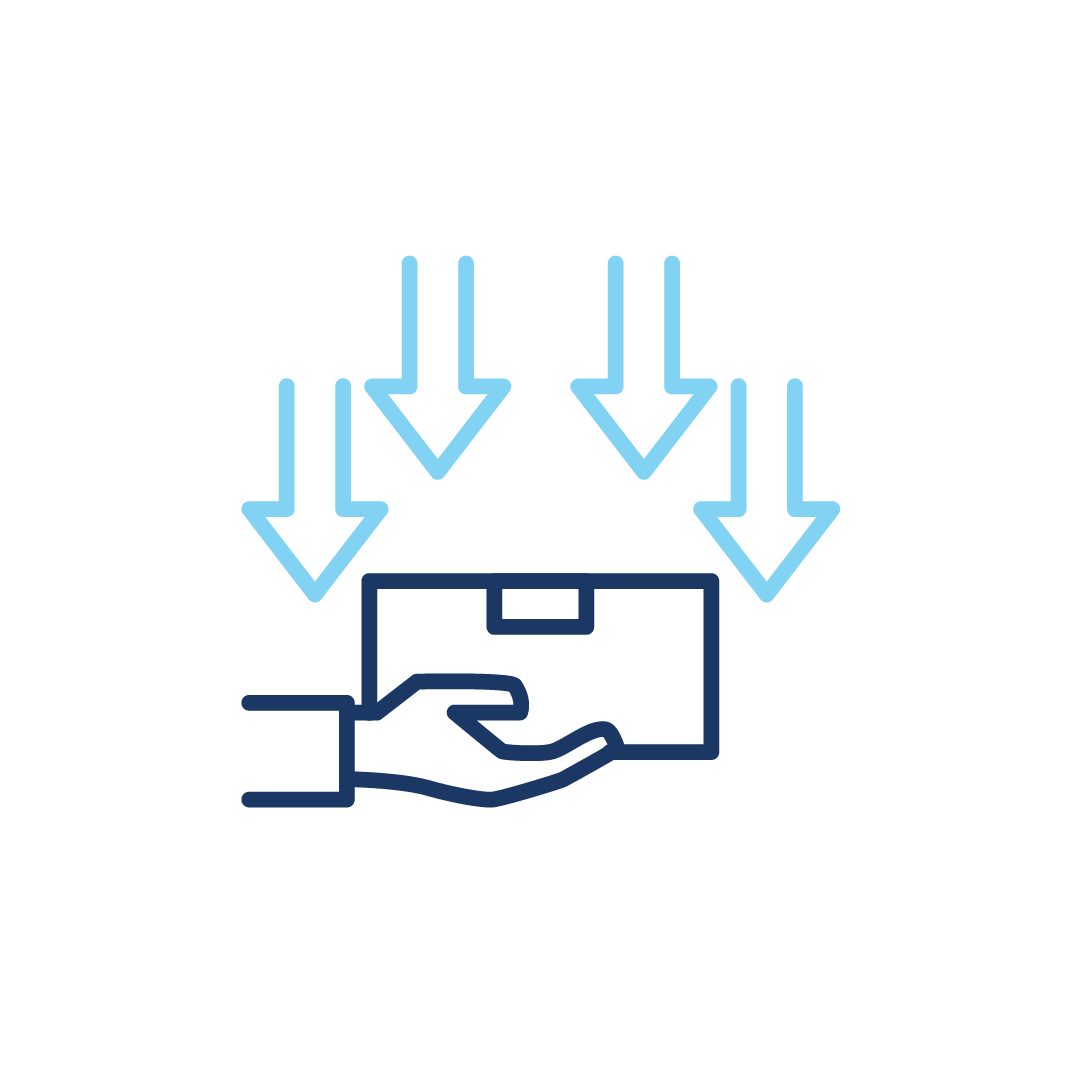
Reduction of manual transports and empty runs
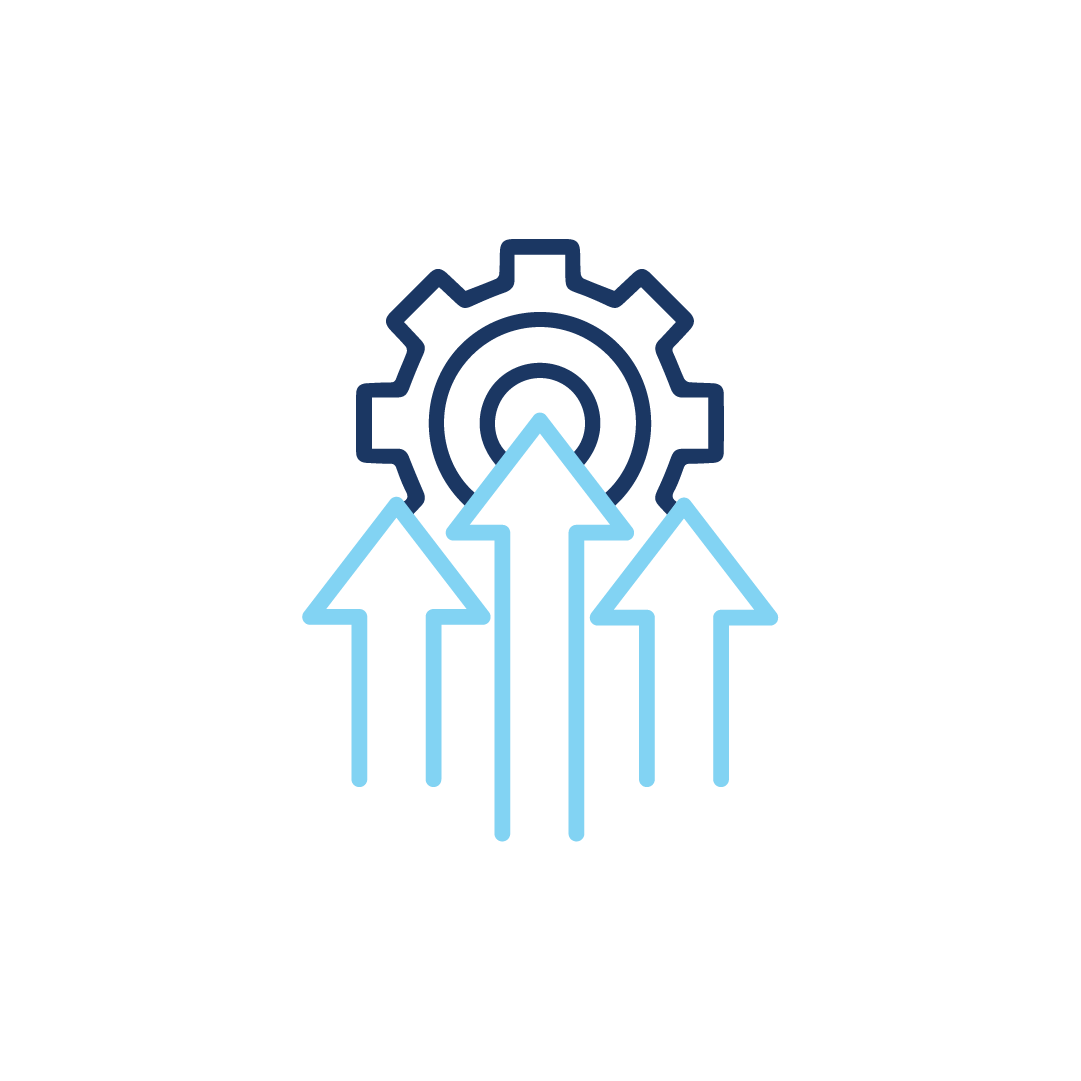
Personnel relief through automated material staging
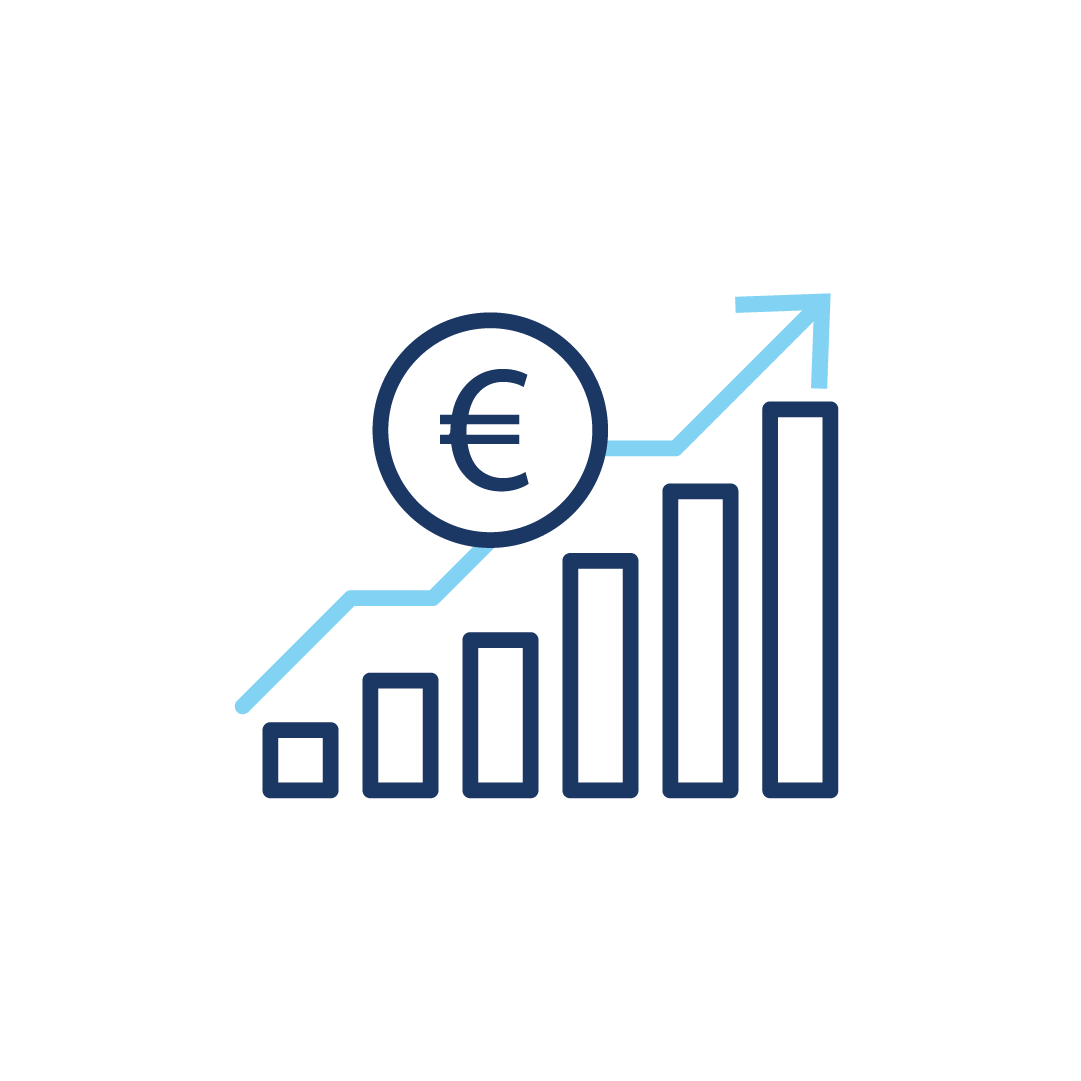
Scalable deployment for changing production requirements
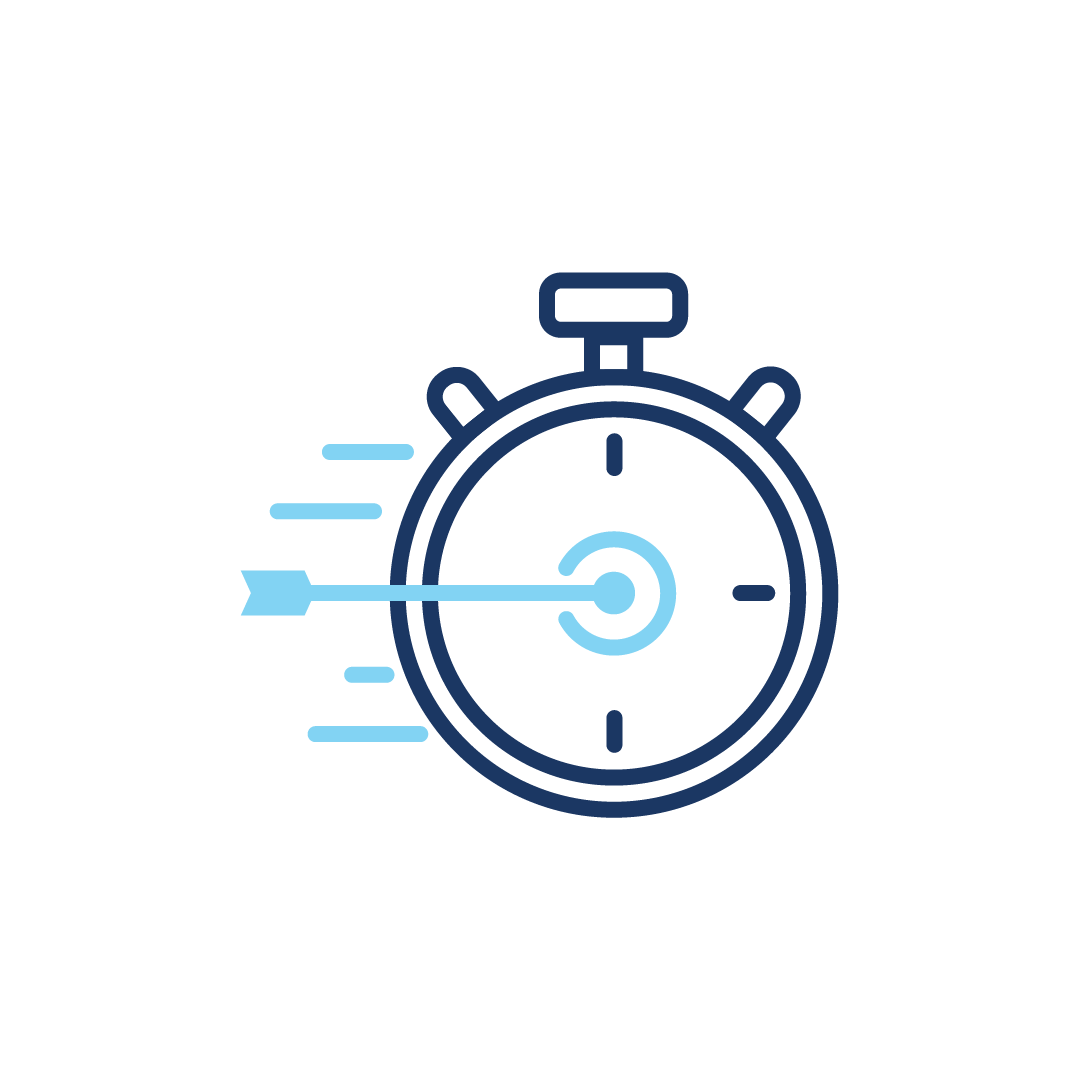
Just-in-time line supply with components, carriers, or containers
Seamless Integration of CTS Systems into Your Existing ERP or MES Setup
sloXis – Middleware for Connected Material Supply
sloXis is not a new control layer – it’s an integration middleware that connects existing ERP, MES, WMS, and CTS systems to enable automated material flows across your factory.
The platform processes data such as order information, inventory levels, or machine statuses and translates it into actionable commands for CTS systems like storage units, buffer stations, or AMRs – from inbound logistics to precise line-side delivery. This enables demand-driven, real-time material handling without interfering with your core IT infrastructure.
Integration is vendor-agnostic and supported through standard interfaces or custom-developed connectors – making sloXis suitable for new and legacy production environments alike.
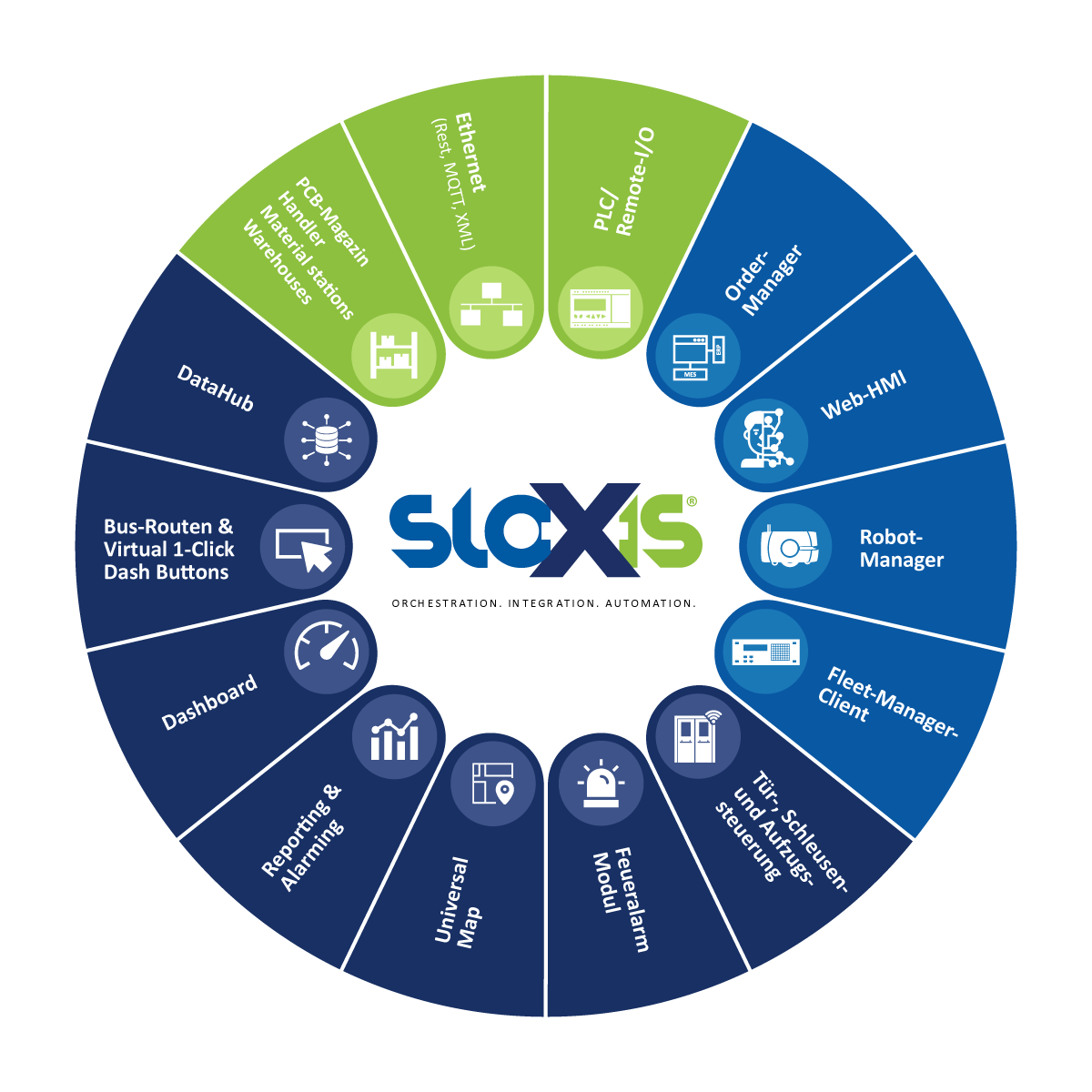
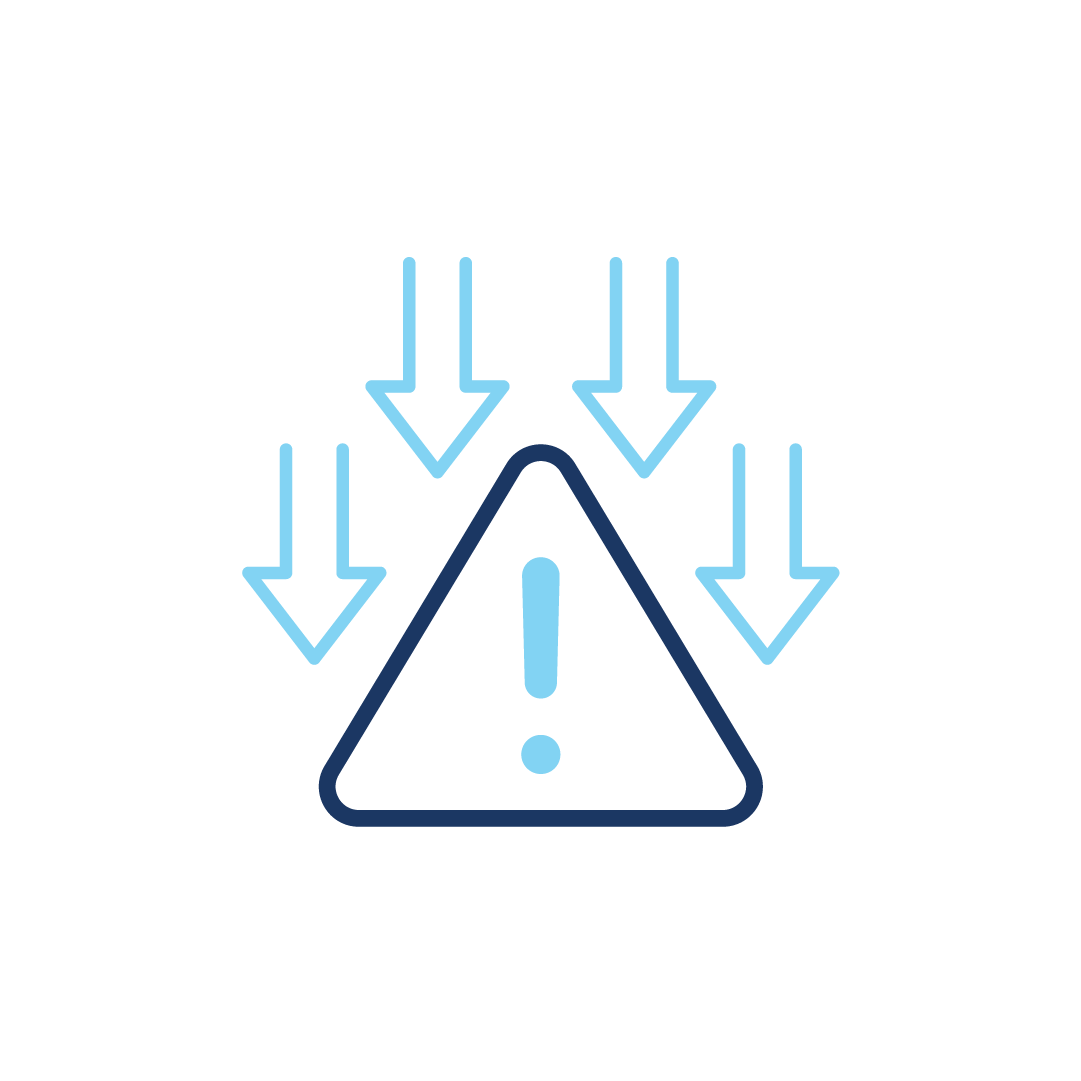
No interference with existing control systems
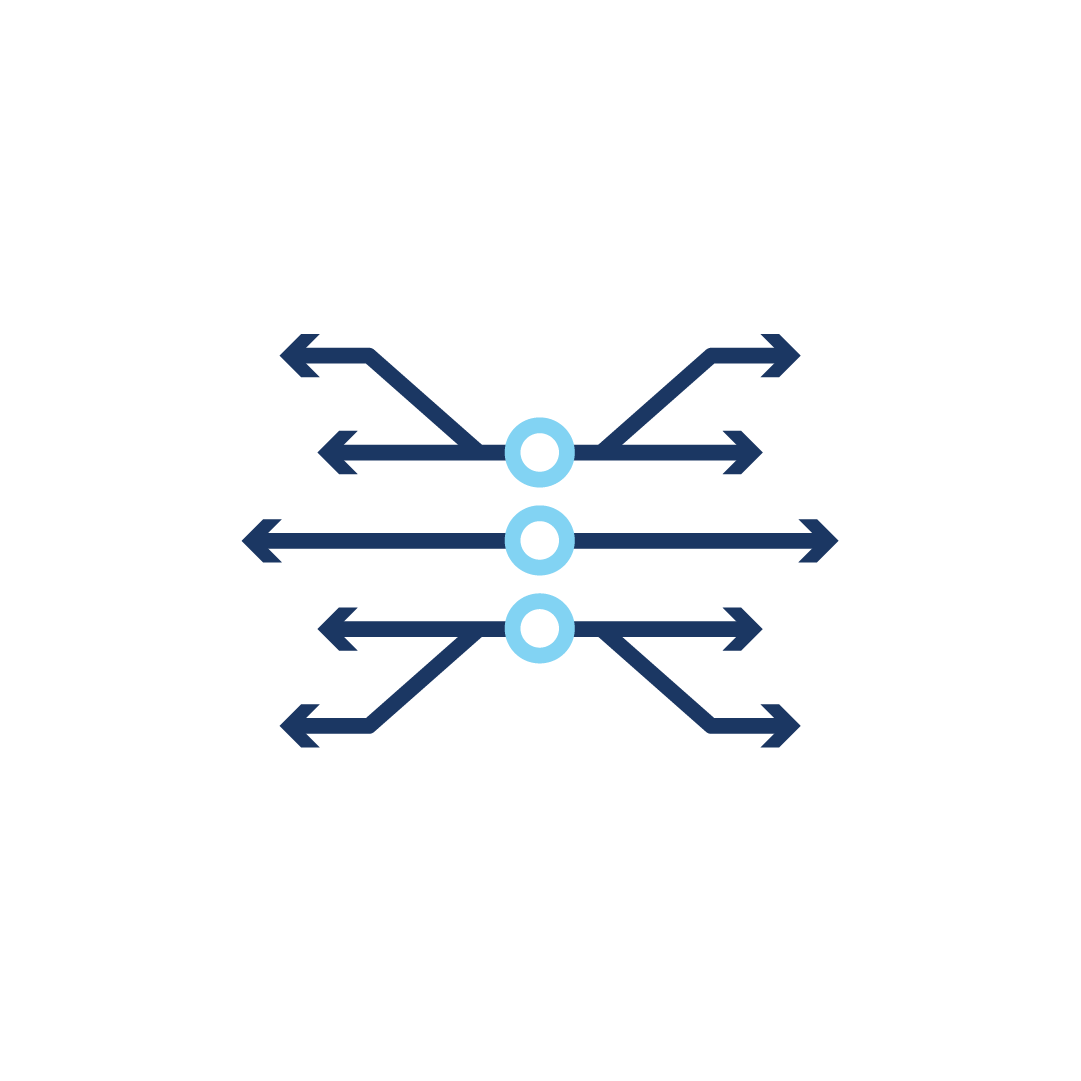
Middleware interface between ERP, MES, WMS & CTS automation
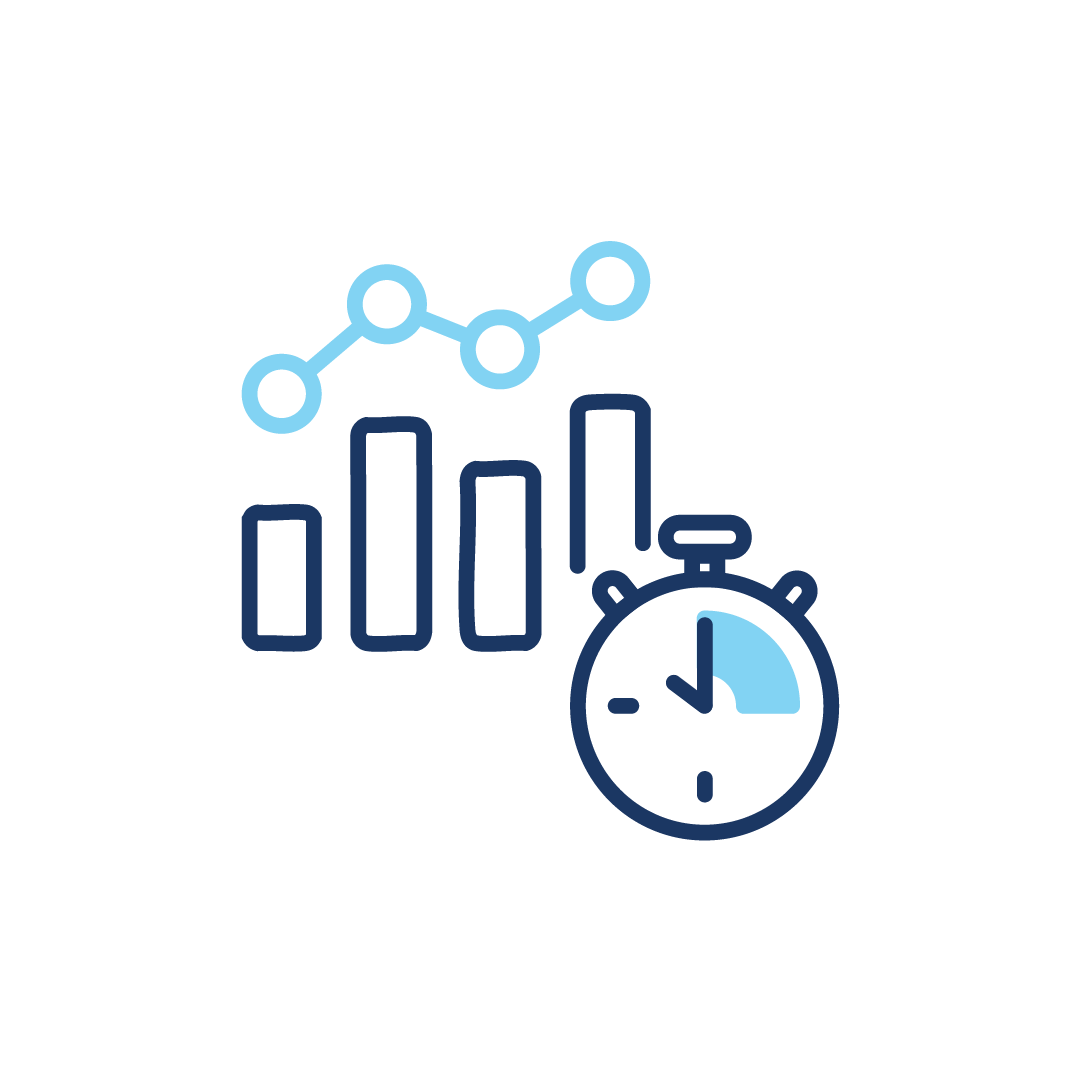
Automated material flow execution across storage and transport systems
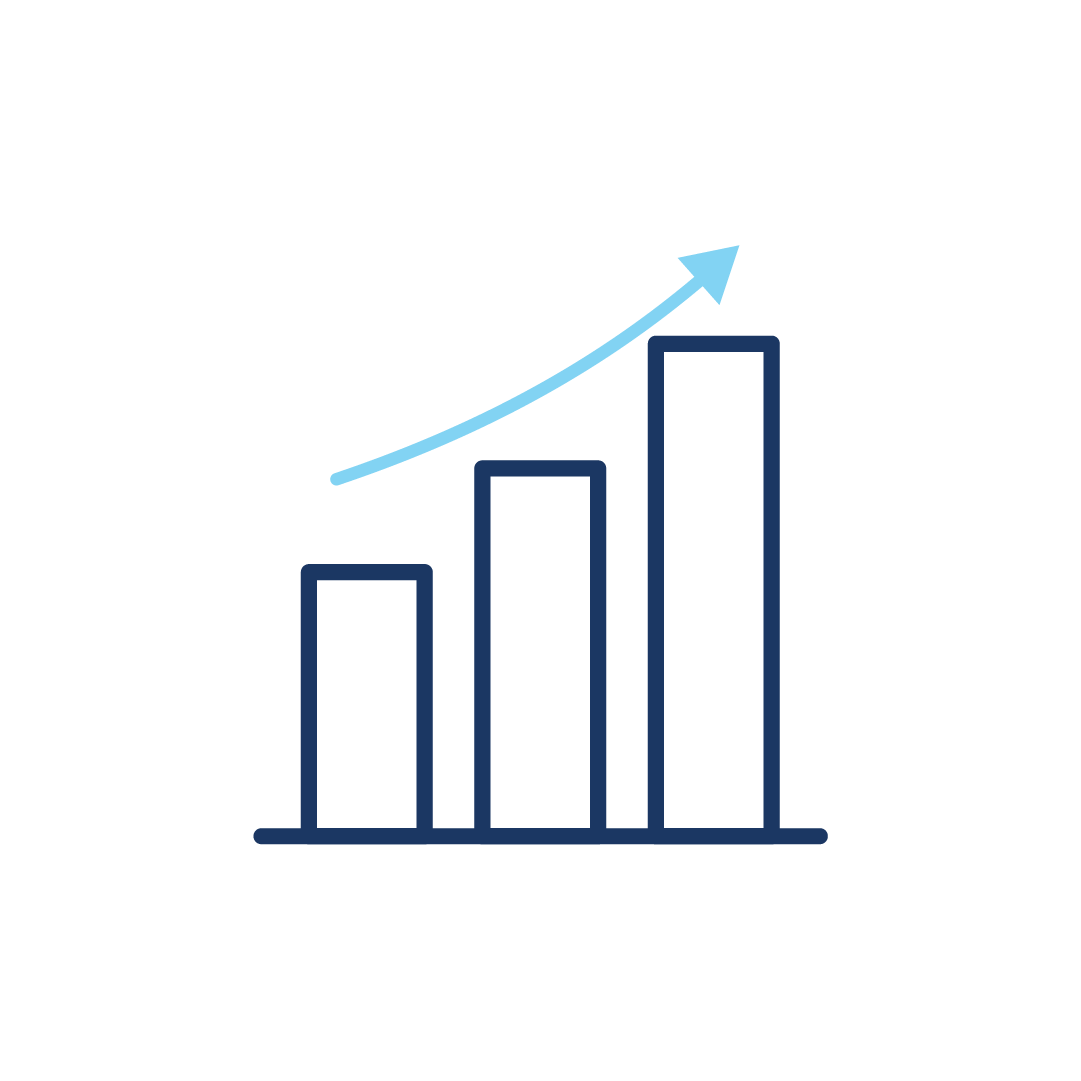
Flexible integration via standard protocols or tailored adapters
Focus on Smart Manufacturing
Discover how intelligent technologies streamline production processes, optimize material flows, and prepare your business for the challenges of tomorrow.
Focus on Smart Manufacturing
Discover how intelligent technologies streamline production processes, optimize material flows, and prepare your business for the challenges of tomorrow.