“Reconstruction with high voltage” - How a substation is made fit for the future
Modern industrial processes need more than just electricity - they need security of supply, scalability and systems that can keep pace with increasing requirements. But what does this mean in concrete terms when an existing infrastructure such as a substation has to be comprehensively modernized - during ongoing operations and under constant time pressure?
We talk to Thomas, Business Unit Manager of Energy Technology at cts, about a project with many areas of tension: technological, logistical and social.
Thomas, you are currently overseeing a comprehensive structural and technical conversion project at an existing substation. Why was this step necessary?
“The technology was simply getting on in years,” begins Thomas. “We're talking about a substation with components that have been in operation for over 30 years in some cases - that's half an eternity in our industry.” However, it's not just about outdated technology, but about a structural transformation: “Our goal was to switch from analog technology to a digital grid structure - to be able to control more precisely, react faster and plan ahead better.”
The conversion is also a response to geopolitical and social developments: “Energy supply is a strategic issue today. We have to make ourselves less dependent on external influences - and that is only possible with an infrastructure that is prepared for the future.”
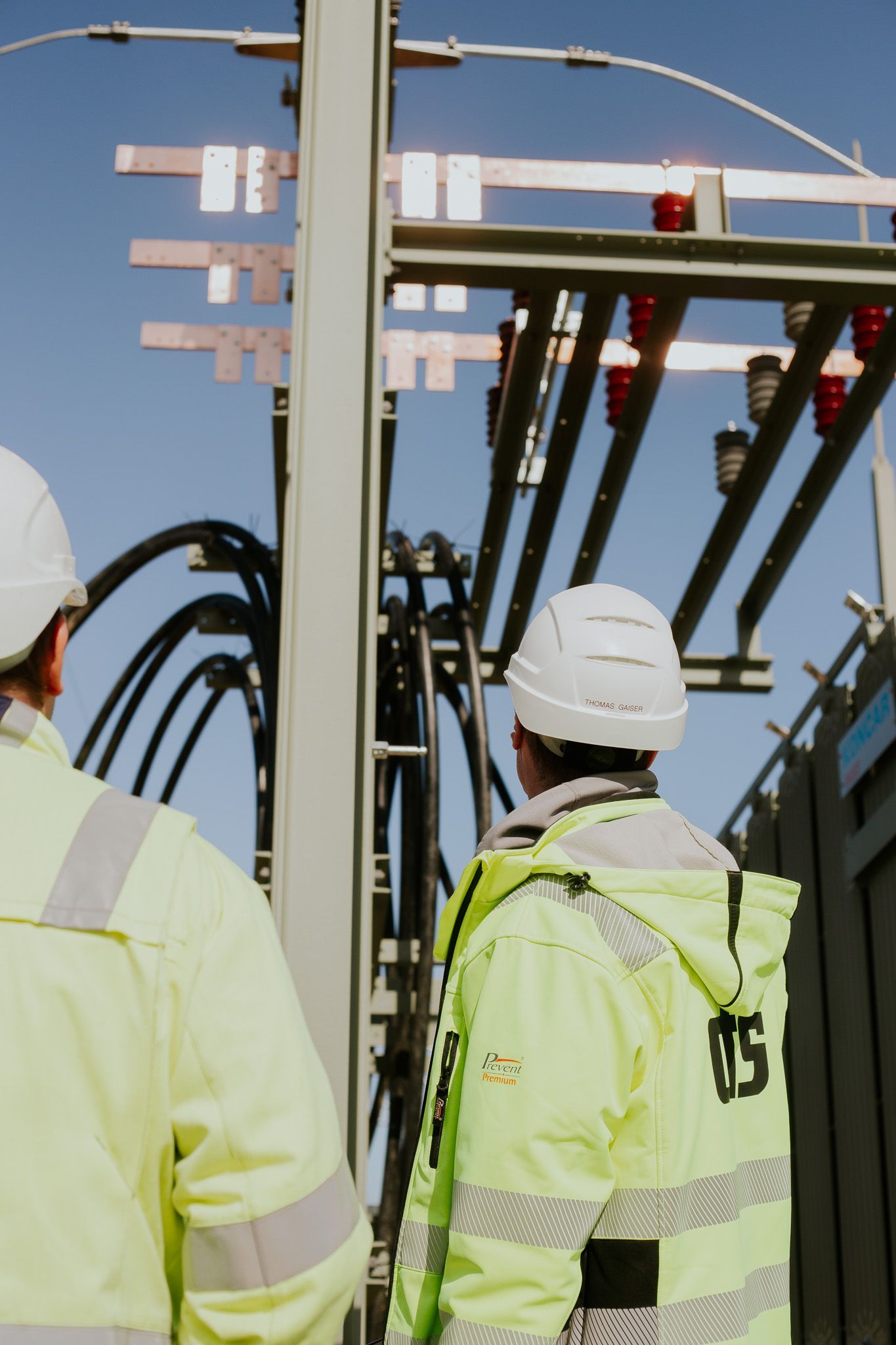
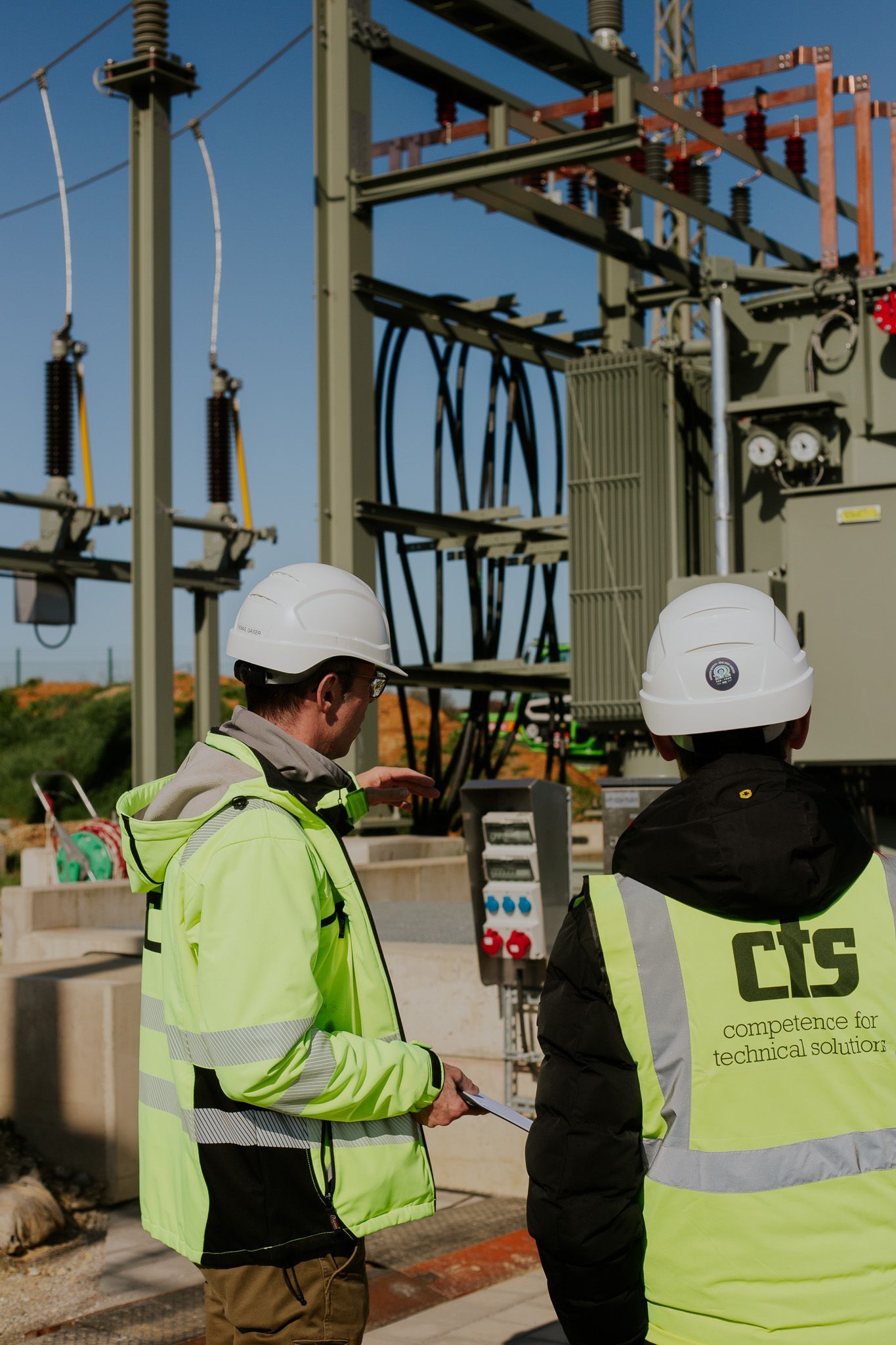
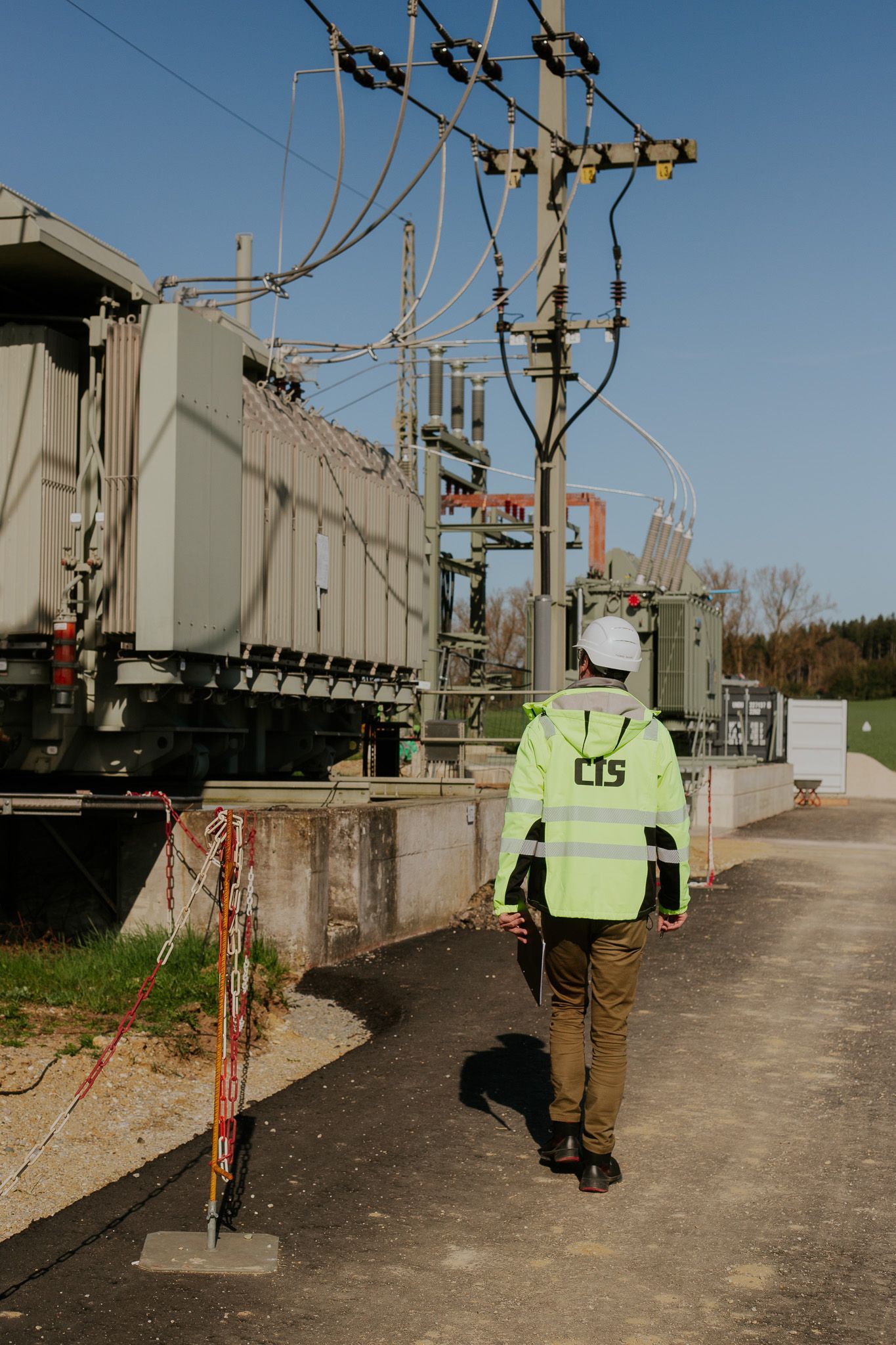
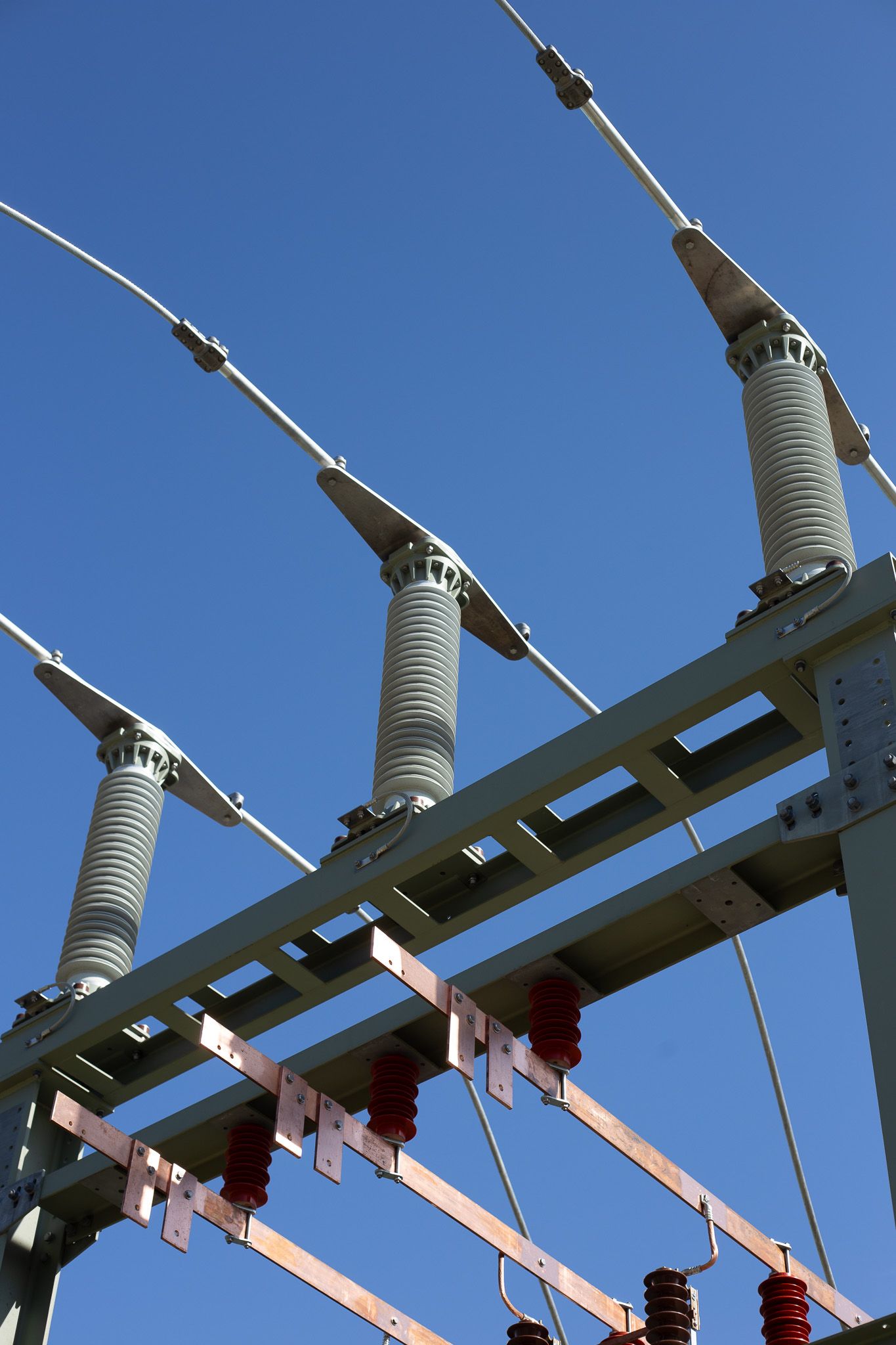
How does a project like this actually start - and what is typically the first critical point?
“In the past, the critical point was the technical implementation. Today, the challenge lies one step ahead: in the availability - of partner companies, of qualified personnel, of materials. That has completely changed.”
We are forced to think about bottlenecks as early as the rough planning stage: “We have learned to standardize as much as possible. We'd rather plan a control cabinet that can do a little more than have to make expensive upgrades later on. This applies not only to the technical side, but also to logistics and project management.”
Standardization now minimizes risk: “We deliberately define components that are scalable - even if they are not needed in the first expansion stage. This makes us faster when the need arises and prevents costly planning adjustments.”
The substation will remain in operation during the conversion. How does it even work under voltage - in the truest sense of the word?
“We don't work under voltage - that's out of the question and far too high a safety risk,” explains Thomas. “Instead, we ensure that the respective field in the grid area is disconnected in advance of the conversion.”
To do this, the electricity grid must be intelligently reorganized. “We're talking about controlled grid switching here. This means that the energy flows are coordinated in such a way that there is no loss of power during the construction work and the supply to the connected consumers remains unrestricted.
This is not simply a matter of switching off a switch. “Before the actual conversion, we have to provide replacement systems, relocate all relevant connection points and ensure that all service obligations continue to be met. These processes have to interlock seamlessly - it's a highly complex process.”
Thomas describes the process as construction on the fly: “There is never a moment of standstill. Everything is timed so that work can continue as soon as a section is stress-free. Our claim is: Nobody should notice anything about the conversion - no interruption, no disruption, no uncertainty. Above all, occupational safety and the well-being of life and limb are at the heart of our work. Protecting the people on the site is our top priority.”
To achieve this goal, precise detailed planning is essential: “We pre-plan every step in detail - including all safety measures, all circuit diagrams, every logistical movement. This is the only way to ensure that we not only work safely, but also stay on schedule and within budget.”
What technical changes are being implemented - and what does “future-proof” mean in this case?
“At the heart of this is the switch from analog to digital technology,” says Thomas. “In future, data will no longer be transmitted via copper cables, but via fiber optic cables. This increases the volume and speed of data and enables a higher volume of data for network monitoring and control.”
At the same time, the modernization is a response to legal and ecological requirements: “With the new systems, we can reduce emissions and comply with regulatory standards more easily. In our case, digitalization is not a gimmick, but a necessary component of a functioning electricity grid.”
He emphasizes: “A substation does not generate electricity, but it distributes it - to where it is needed. That's why the strategic expansion of substations is crucial for grid stability - now more than ever.”
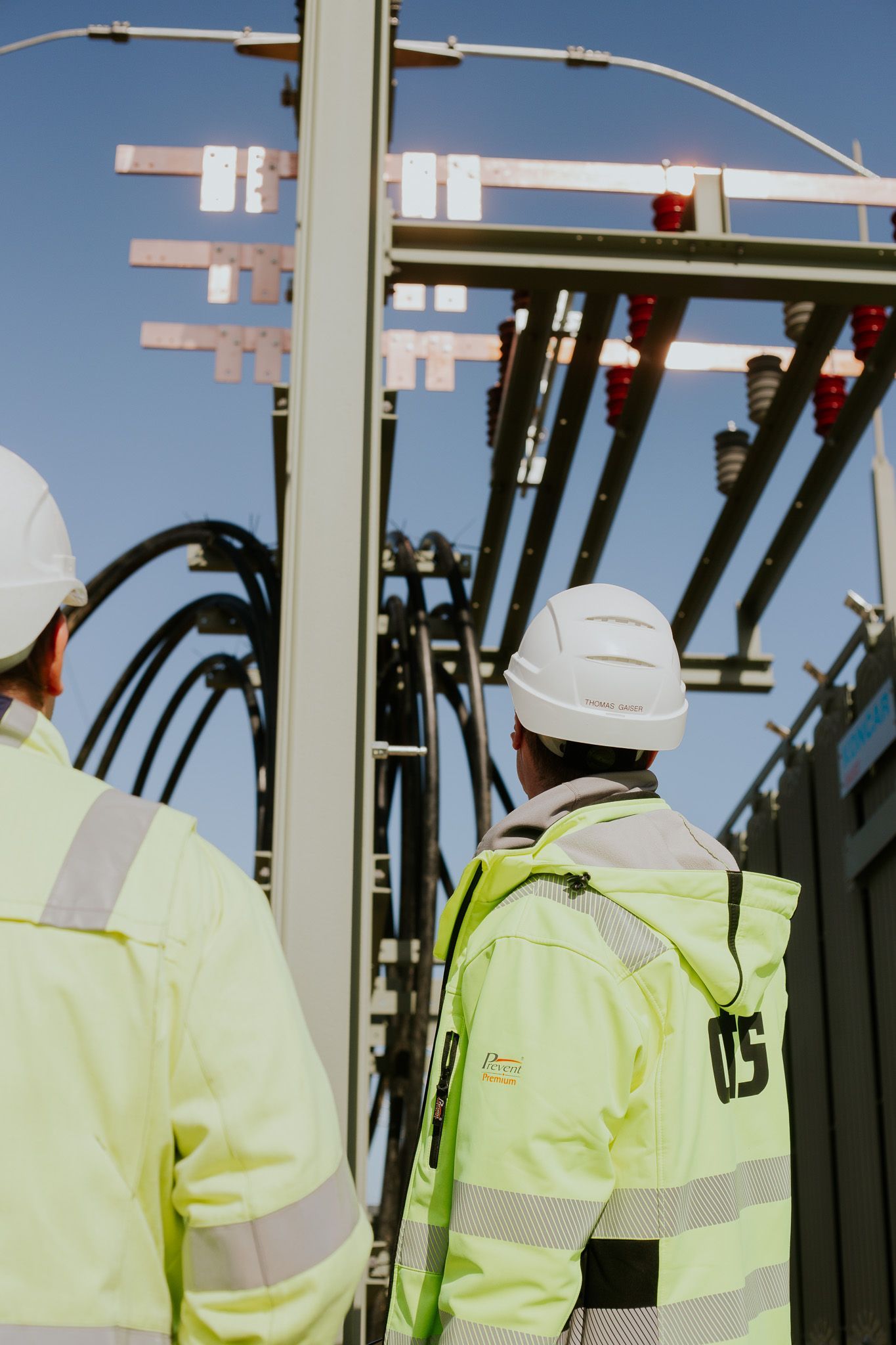
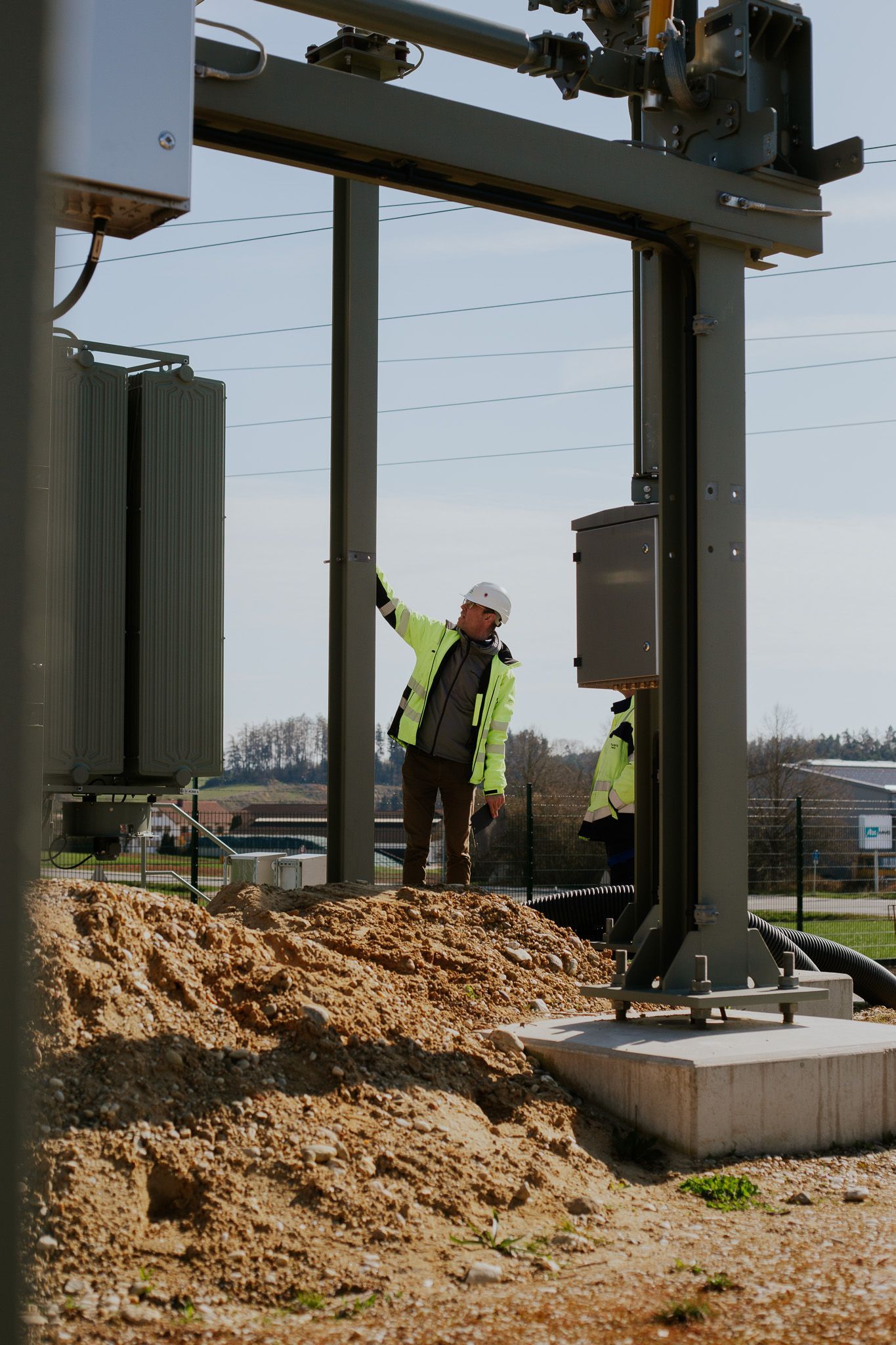
What are the biggest challenges in energy infrastructure projects today - technology, approval, interfaces?
“It's a rat's tail of issues that is now becoming a challenge. Technology, personnel, permits - everything is connected.”
Thomas is clear: “We have a massive shortage of skilled workers. It doesn't help if I have the equipment but no one can set it up. Or I have employees, but nothing they can install because the required equipment or material cannot be produced by the supplier.”
There are also infrastructural and social barriers: “When network operators say: we need a new hub here, you also need the right land. And this often belongs to private individuals who are opposed to a transformer station on their doorstep. There is a lack of acceptance.”
“In Germany, we are good at rejecting things that we simply need. Everyone wants electricity - but preferably without visible infrastructure. The “unsightly” wind turbines are another example of this.”
If you had to pick out one element of the project that is particularly underestimated - what would it be?
“Yes, of course: the civil engineering,” says Thomas without hesitation. “We were dealing with an existing conversion here - and in projects like this, the biggest surprises don't lurk in the technology, but in the ground.”
He reports that they came across a large number of unexpected contaminated sites: “There were old foundations, undocumented cable routes with disused cables, laid pipelines and sometimes even contaminated materials such as old, oil-insulated cables.” Many of these structures were not listed in the as-built plans or in the official documents. “That really messed up our schedule, every single one of these contaminated sites meant reassessing, possibly dismantling and disposing of them - all of which eats up resources and time.”
Thomas goes on to explain that this made civil engineering for the cable construction in particular much more difficult: “You always think that civil engineering is routine - dig a trench, lay the cable, close it again. But in the reality of an existing project, you can never be sure what awaits you below the surface.”
What role does switch cabinet construction play in this - and why is it a critical component for many customers?
“It is one of the most critical pillars in the entire process,” says Thomas. “The control cabinet is the backbone of our energy distribution. If the requirements in terms of scope, interfaces or expandability are not properly planned from the outset, the control cabinet quickly becomes a bottleneck in the project.”
He reports on a specific example from the current conversion: “A single relay was missing - tiny, but we couldn't install the entire control cabinet without this component. As a result, an entire section of our installation had to be re-timed.”
In addition, long delivery times for individual components - sometimes several weeks - made planning even more difficult. “That's why we rely on early ordering. “The control cabinet is the control center of the entire system. It's where everything comes together - and if it doesn't work, everything comes to a standstill.”
To what extent is this conversion also a contribution to the energy transition?
“In concrete terms,” emphasizes Thomas. “According to the current concept, additional options for feed-in fields are being planned. Depending on grid planning/management requirements, an additional transformer will also be planned and implemented. This is technically designed to connect so-called large-scale feeders directly to the grid via the transformer station.” Large-scale feeders - by this he means photovoltaic parks, wind turbines or biogas plants with outputs of around 12 MVA or more.
“These measures are necessary in order to be prepared for the higher energy demand. In this case, this has a huge impact on the design of our infrastructure.”
Thomas makes it clear that these projects make a direct contribution to the energy transition: “This not only makes the integration of renewable energy sources technically easier, but also makes more economic sense. We ensure that grids do not perceive these feeders as a burden, but as part of a new, more robust overall system.”
He summarizes: “The grid structure must become denser, more fragmented and more flexible. This is the only way we can guarantee security of supply even with growing demand and increasing volatility.”
And finally: What would you like to say to companies facing a similar modernization?
“Involve the people who will later be involved in the implementation - and as early as possible,” Thomas advises emphatically. “Decisions are often made during the feasibility study phase or the initial rough concept that have a massive impact on the subsequent implementation. If no one from the execution team is involved at this point, valuable perspectives are missing.”
In his view, many technical or practical challenges could be defused in the early phase: “It's not about anticipating everything in detail. But it helps enormously if someone points out early on: 'Pay attention to the space available here', or 'This type of cabinet won't be available in six weeks'. This not only saves costs, but also prevents delays and planning chaos.”
“It makes a difference whether a system works on paper or whether it can actually be implemented efficiently and under the given conditions. This is why the early involvement of implementation expertise is not an additional expense - it is a prerequisite for project success.”