Projektbericht: Prozessautomatisierung im Zillertal
Stillstand ist keine Option: Zum Montag muss die Milch wieder laufen
Früh am Morgen. Zwischen Milchtank und Ventilblock läuft der Betrieb, wie er seit Jahren läuft – und doch steht die größte Umstellung seit Jahrzehnten bevor. Denn in der österreichischen Erlebnissennerei Zilleratal wird das bestehende Prozessleitsystem durch ein vorhandenes PCS 7-System integriert. Weiters wird das PCS 7 hochgerüstet. Die Herausforderung: Die Umstellung muss komplett an einem Wochenende erfolgen – inklusive Schaltschrankumbau, Software-Inbetriebnahme und Signaltests. Neue Schrittketten, neue kontinuierliche Logiken, neue Visualisierung, neue Dokumentation. Was bleibt: die Erwartung, dass am Montag alles läuft wie vorher – unter zukunftsfähigen Voraussetzungen.
Was passiert, wenn eine Sennerei ihre komplette Automatisierungstechnik austauscht – und das unter laufendem Betrieb, mit enger Deadline und sensiblen Prozessen?
Wir haben mit Florian, Bauleiter bei diesem Projekt, und Andreas, Projektleiter und „Programmierer“ bei diesem Projekt, über die Herausforderung gesprochen, moderne Technik in einen gewachsenen Betrieb zu integrieren – ohne Kompromisse bei Sicherheit, Hygiene und Qualität.
Die Frage klingt erstmal banal. Doch wer die Sennerei betritt, merkt schnell: Mit der romantischen Vorstellung vom Milchkessel am offenen Feuer hat das nichts mehr zu tun.
„Die Sennerei ist nicht mehr so, wie man sich das früher vorstellt, dass der Bauer beim Fassl umrührt“, sagt Florian. „Auch hier ist alles automatisiert.“ Milch wird angeliefert, abgelegt, analysiert, verteilt – und in unterschiedlichen Linien verarbeitet.
„Das Ablegen ist der Einstieg in den Wirtschaftskreislauf“, erklärt Florian. „Milchtankwagen kommen rein, die Milch wird abgelegt und in verschiedene Tanks gepumpt. Dabei laufen Prozesse über Ventile, die öffnen und schließen, über Regelventile, über Temperatur- und Gütemessung – alles, was für die Verarbeitung wichtig ist.“ Auch das Labor ist direkt angebunden: „Dort werden Proben gezogen, Werte erfasst, die für den weiteren Prozess gebraucht werden.“
Aus der Milch entsteht vor Ort ein komplettes Produktspektrum – alles, was im Shop landet: Butter, Joghurt, Rahm, verschiedene Käsesorten. Damit das zuverlässig funktioniert, übernimmt cts die komplette prozessautomatisierungs-technische Umstellung.
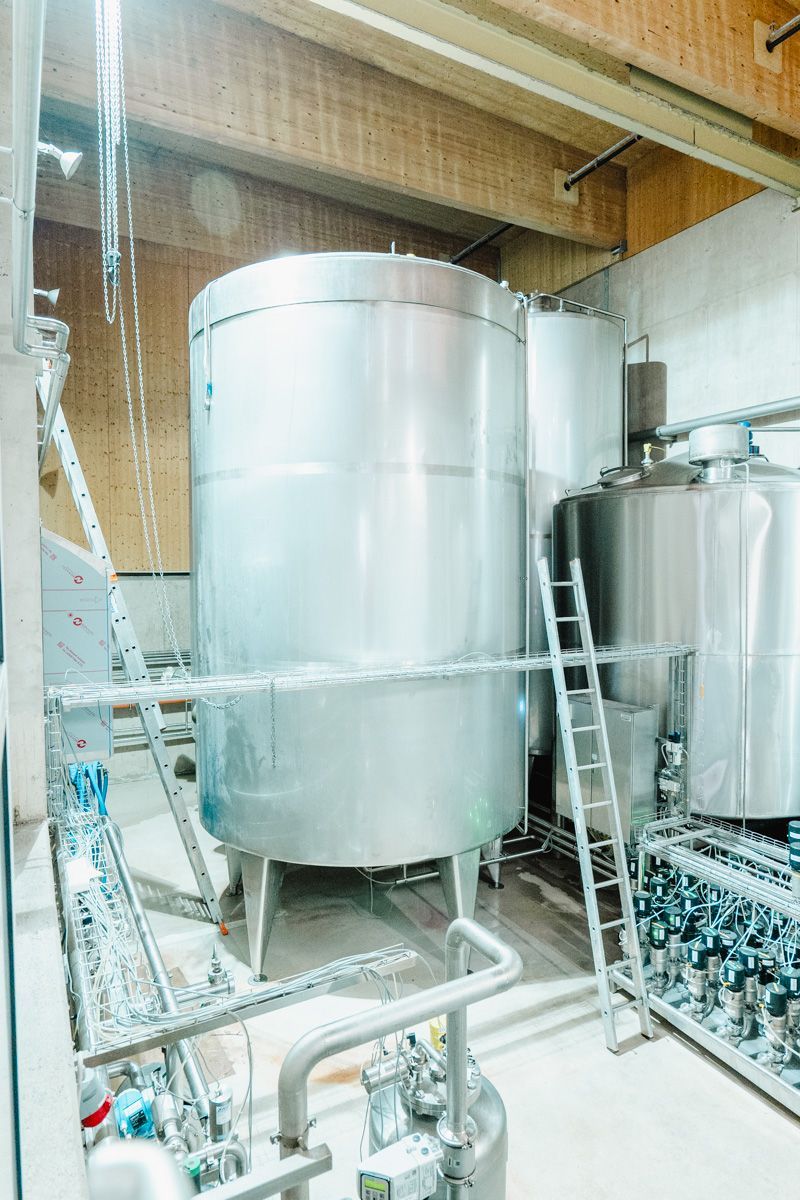
„Unsere Aufgabe ist: alles, was vom Sensor bis zur Software dazugehört“, so Florian. „Wir steuern die Aktoren und Sensoren an, ziehen neue Feldkabel, nutzen aber auch bestehende Sammelkabel. Wir bauen die Remote IOs ein und programmieren das neue System.“
Vier neue Remote IOs wurden an unterschiedlichen Stationen in der Anlage installiert: im Tanklager, im Bereich für Butter, Joghurt und Rahm, im CIP-Raum für die Reinigung und im Maschinenraum. „Bisher war ein Foxboro-System im Einsatz, das integrieren wir in ein Siemens- System – teilweise übernehmen wir Bestehendes, teilweise ersetzen wir.“
Die entscheidende Phase beginnt mit dem geplanten Shut Down im September. „Am Freitag wenn die am Tag abgelegte Milch verarbeitet ist – dann wird alles abgeschaltet“, sagt Florian. „Wir arbeiten dann mit 35 Leuten in Tag- und Nachtschicht. Freitag, Samstag, Sonntag wird alles angeschlossen, inklusive dem Main Control Center. Und am Montagmorgen wird wieder Milch abgelegt – dann muss wieder alles wie gewohnt funktionieren.“ Trotz der Größe des Projekts bleibt Florian ruhig: „Wenn wir das Projekt mit Struktur angehen, dann wird es ein Erfolg.“
Was genau ist die Aufgabe von CTS in diesem Projekt – was machen wir vor Ort?
Unsere Aufgabe ist es, die bestehenden Anlagen zu erneuern und zu modernisieren – technisch, aber auch funktional. Das heißt: Wir programmieren die Software neu, entwickeln das Fließbild im Prozessleitsystem komplett neu und übertragen die bestehenden Funktionen in eine aktuelle, stabile Systemumgebung.
Ein zentraler Punkt war dabei: Die Maschinisten sollen sich im neuen System wiederfinden. Es war eine klare Anforderung, dass die Oberflächen so gestaltet sind, dass sie vertraut wirken. Es geht also nicht darum, alles neu zu machen – sondern darum, das Bestehende zu erhalten, dort wo es Sinn macht, und es in eine moderne Lösung zu überführen.
So vermeiden wir, dass die Bediener sich auf eine komplett neue Umgebung einstellen müssen – das reduziert Schulungsaufwand und Übergangsprobleme. Unser Ziel ist, den Umstieg so einfach und reibungslos wie möglich zu machen – technisch wie menschlich.
Wie sieht so ein Projekt von Beginn an aus?
Zu Beginn haben wir uns mit den Gegebenheiten vertraut gemacht und die Anlage besichtigt. Mit dabei waren sechs Monteure eines Partnerunternehmens, Andreas und ich. Gegen 13 Uhr kam der LKW aus Burgkirchen – mit den Remote IOs, Klebeetiketten und dem restlichen Zubehör.
Die RIOs wurden bei uns im Schaltschrankbau in Burgkirchen vorbereitet, speziell angepasst auf die hier vor Ort geltenden Anforderungen. Die Schaltschränke stehen in Hygienebereichen – aus Edelstahl, mit lebensmittelfähigen Dichtungen und komplett abgedichtet. Sie müssen keimfrei bleiben, deshalb kann dort auch nicht jeder einfach ran. Es hat auch nicht jeder einen Schlüssel, was die Zugänglichkeit bewusst einschränkt.
Aktuell laufen die ersten Arbeiten: Wir gehen nach R&I-Schema die einzelnen Messstellen durch, identifizieren sie und bekleben sie mit neuen Etiketten. Das hilft uns beim späteren Kabelziehen – und entspricht auch dem Wunsch des Betriebs, die gesamte Beschriftung der Messstellen sauber und einheitlich zu gestalten. Zwei bis drei Kollegen sind bereits direkt in der Umsetzung.
Parallel dazu laufen die Vorbereitungen für den Stichtag. Dann wird vom RIO aus ins Feld verdrahtet – zu Ventilen, Temperatur- oder Druckmessgeräten. An den RIOs selbst lassen sich viele Kabel schon jetzt anschließen. Die finalen Anschlüsse am Feldgerät erfolgen aber erst am Umstellungstag. Dann wird alles verbunden, ein Loop Check durchgeführt – und wenn das durchläuft, geht’s direkt weiter
Was war der Auslöser für das Projekt – warum wurde cts ins Boot geholt?
Das alte System war technisch und organisatorisch an seine Grenzen gekommen. Es gab nur noch einen Ansprechpartner, der sich mit dem System auskannte – und der hat das jahrelang allein betreut. Das wurde irgendwann ein Risiko. Wir wussten: Wenn wir das sauber auf neue Beine stellen wollen, dann so, dass wir unserem Kunden eine zukunftssichere Lösung aufbauen – dokumentiert, betreubar und langfristig tragfähig.
Wir wurden ursprünglich als Backup vorgesehen. Das damalige Foxboro-System wurde von einem Kollegen aus der Firma betreut – und wir sollten in die Lage versetzt werden, es im Notfall mitzubetreuen. Das war der Einstieg.
Andreas war vor acht, neun Jahren das erste Mal hier. "Ich habe mir damals den Bestand angesehen – da gab es bereits ein PCS 7-System – und mit Heinrich Kröll, dem Geschäftsführer der Erlebnissennerei Zillertal, über mögliche Optionen gesprochen. Ich habe ihm gesagt: Wenn ihr irgendwann upgraden wollt, könnt ihr das auch in Richtung PCS 7 machen. Siemens hatte das damals schon so groß ausgelegt, dass man das bestehende Foxboro-Automatisierung praktisch übernehmen konnte. Das hieß aber nicht: Ihr müsst das mit Siemens machen – das könnt ihr genauso gut mit uns umsetzen.
In den Jahren danach haben wir das Projekt immer wieder begleitet. Es gab erste Überlegungen, die Umstellung in Teilen zu realisieren, portionsweise. Aber es wurden andere Projekte priorisiert – und die Umsetzung hat sich hinausgezögert.
Als dann der endgültige Bedarf da war, haben wir gemeinsam entschieden: Wenn wir’s machen, dann machen wir’s auf einmal. Nicht nur eine Umstellung oder ein bisschen Modernisierung – sondern alles. Die gesamte Steuerung, alle Schaltschränke, alles an einem Wochenende."
Und was braucht es dafür technisch?
Man muss beides können: Das alte Foxboro-System „lesen“ und verstehen – und gleichzeitig PCS 7 sauber programmieren. Es gibt keine vollständige Spezifikation, die man einfach abarbeiten kann. Das ist systemspezifisch. Der Kunde kennt zwar die Funktionen – aber nicht alles bis ins Detail.
Wenn man so etwas in drei Tagen umstellen will, muss man das alte System wirklich durchdringen. Man muss es sozusagen „1:1 nachbauen“ – mit allen Funktionen. Sonst funktioniert es nicht.
Wie muss man sich dem Umstellungsprozess konkret vorstellen?
Die Umstellung erfolgt in einem sehr eng gesteckten, aber durchdachten Zeitfenster. Der letzte LKW kommt an einem Wochenende im September am Freitag, der erste wieder am Montag – dazwischen haben wir Zeit für die komplette Demontage der des alten MCCs (Main Control Center), die Installation der neuen Hardware, der Anschluss aller Feldgeräte und die Inbetriebnahme. Wir bereiten im Vorfeld intensiv vor: Das System wird auf einem Testsystem vorab in Betrieb genommen, alle Signale werden simuliert, die Software getestet. Dann treten wir mit rund 20 Kollegen in Tag- und Nachtschichten vor Ort an – und am Montagfrüh muss alles wieder laufen. Das wird sportlich, aber es wird funktionieren.
Viele stellen sich eine Sennerei eher handwerklich vor. Was hat Prozessautomatisierung damit zu tun?
Wenn man „Sennerei“ hört, denken viele an Handwerk. Wie automatisiert ist es hier wirklich?
Hier sind nur noch ausgewählte Arbeiten handwerklich, die man nicht automatisieren kann oder soll. Es geht auch in der Sennerei modern zu – die Prozesse werden wie in einer Fabrik gesteuert. Das beginnt bei der Anlieferung und geht über die Temperaturführung, die Ventilsteuerung bis hin zur CIP-Reinigung. Ohne Automatisierung würde das heute nicht effizient funktionieren.
Welche Rolle spielt die Automatisierung in einem Lebensmittelbetrieb wie diesem?
Die Steuerung ist das Herzstück. Wenn etwas nicht läuft – sei es die Erhitzung, die Reinigung oder die Dosierung – dann steht der Prozess. Und weil wir in einem sensiblen Umfeld arbeiten, geht es nicht nur ums Laufen, sondern um Wiederholbarkeit, Nachvollziehbarkeit und Sicherheit. Wir haben bestimmte Anforderungen, auch in Richtung unserer Kunden – und da ist es essenziell, dass wir über ein System verfügen, das nicht nur funktioniert, sondern auch dokumentiert, was es tut.
Wie sieht das in der Praxis aus – wo genau setzt Automatisierung in der Anlage an?
Wir reden hier über den kompletten wertschöpfenden Weg – von der Anlieferung bis zum Käsefertiger. Das heißt konkret: Milch wird angenommen / abgelegt, eingelagert, im Rohmilchlager vorgehalten, dann zentrifugiert und pasteurisiert. Danach wird sie eingelagert, vorbereitet – als Rahm, Butter oder Sahne. Dort entsteht auch der Rohstoff für die Käsefertiger.
Die Käsefertiger selbst gab es schon im PCS 7 System. Aber der klassische Molkereiteil davor – ohne den geht es nicht. Der muss genauso funktionieren, sonst steht alles.
Es gibt natürlich noch händische Arbeit: Die Käseblöcke werden gereinigt, verarbeitet, vorverpackt. Butter wird manuell portioniert und verpackt. Aber alles, was Sinn macht zu automatisieren, soll auch automatisiert werden.
Ziel ist es, die Mitarbeitenden zu entlasten – so viel wie möglich. Zum Beispiel: Der Maschinist muss aktuell noch in die Anlage gehen und Koppelbögen umschließen. Auch das soll künftig automatisiert werden, damit man das direkt aus der Messwarte umsetzen kann.
Es geht nicht darum, Arbeitsplätze zu ersetzen – sondern darum, körperlich schwere oder gefährliche Arbeiten zu reduzieren. Automatisierung heißt hier: Schutz der Mitarbeiter, nicht Konkurrenz.
Was hat aus eurer Sicht den größten Einfluss auf die Produktqualität – wenn man Automatisierung, Validierung und Betrieb zusammendenkt?
Qualität ist immer das Ziel – aber in der Praxis entscheidet sie sich oft an vielen kleinen Punkten: an der Steuerung, an der Reinigung, an der Dokumentation. Wo liegt für euch der größte Hebel, um die Qualität wirklich abzusichern?
"Ganz klar: Präzision", sagt Florian. Der ganze Prozess muss präzise ablaufen. Die Milch muss genau die richtige Temperatur haben, die Reinigung muss exakt im vorgesehenen Zyklus passieren. Jeder einzelne Arbeitsschritt muss stimmen – sonst bricht das ganze System zusammen. Einfach gesagt: Ohne Präzision geht’s nicht.
Andreas: "Für mich sind es vor allem die Konzentrationen – zum Beispiel bei Lauge und Säure. Wenn die nicht stimmen, ist die Reinigungsleistung gefährdet. Und dann geht es um Reproduzierbarkeit: Ich muss sicherstellen, dass die Abläufe immer gleich ablaufen. Dabei helfen uns Trendaufzeichnungen – Temperaturverläufe, Durchflüsse, alle Prozesswerte, die wir im Nachhinein nachvollziehen können." Nur so lässt sich Qualität auch belegen.
Was ist aus eurer Sicht das Ziel des Projekts – also: Woran erkennt ihr, dass es erfolgreich war?
Wenn am Montag der LKW die Milch ablegen und anschließende gereinigt werden kann – dann war’s erfolgreich. Natürlich muss die Milch auch, wie gewohnt, weiterverarbeitet werden können. Das ist der Punkt, auf den alles hinausläuft.
Aber das ist natürlich nur das sichtbare Ergebnis. Das Projekt selbst läuft schon viel länger – die Entwicklung der Software und die Planung Hardware hat im Dezember des letzten Jahres schon begonnen. Und es geht nicht nur darum, dass am Ende Milch von A nach B gepumpt wird. Wichtig ist auch, dass der Kunde den Fortschritt sieht.
Er sieht, was passiert – an den Kabeln, an der Visualisierung. Er begleitet uns durch das ganze Projekt, will wissen, wo wir stehen, was getestet werden kann, wie der aktuelle Stand aussieht. Dieses Feedback läuft durchgehend mit – bis wir zum finalen Umstellungswochenende kommen.
Wir haben eine gute Vorlaufzeit, um genau diese drei kritischen Tage vorzubereiten. Der Kunde hilft tatkräftig mit – einfach, weil er seine Anlage genau kennt. Das ist für den Erfolg entscheidend